To do a health and safety risk assessment you need to identify potential workplace hazards. This means surveying the environment and reviewing past incidents to make sure you cover everything. Then assess the risk of those hazards. Risk matrices can help you prioritise based on impact.
Once you have assessed the risk put in place controls to mitigate them e.g. use of PPE or engineering solutions. Review and update the risk assessment steps as circumstances change. For more information on advanced methods and challenges in this risk management process see further.
Summary
- Survey the workplace and review past incidents to identify potential sources of harm.
- Assess risk by evaluating the likelihood and severity of harm for each hazard.
- Implement controls that focus on elimination, substitution, engineering controls and PPE to mitigate risk.
- Record the risk assessment process to hold accountability and compliance and to review regularly for changes in the workplace.
- Use risk assessment tools like matrices and heat maps to prioritise hazards and inform risk decisions.
What is Risk Assessment
Understanding and conducting risk assessments is key to identifying and managing hazards in any workplace.
The risk assessment process is a systematic approach to risk communication and hazard identification which is essential for health and safety. By assessing risk you can identify potential hazards that might be harmed or could harm employees or customers.
This means informed risk management decisions so you can put in place the right controls. A risk assessment not only identifies risk but also assesses severity so your team can prioritise actions.
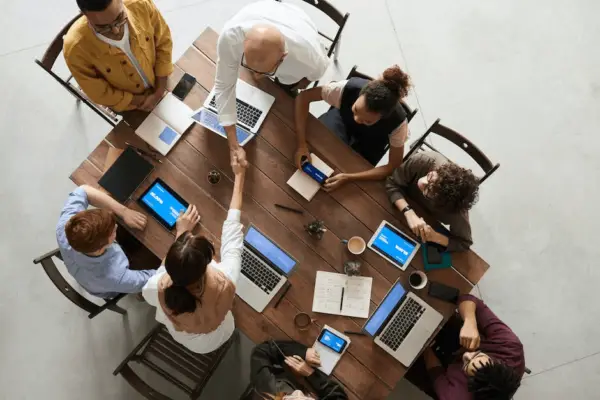
How the Risk Assessment Process Works
The risk assessment process is identifying hazards, analysing the risk and putting in place effective controls to mitigate harm. This is key to occupational health and safety.
During a full risk assessment safety teams do a full risk analysis to identify potential hazards that could affect employees. They use established risk criteria to prioritise safety hazards based on impact.
Analysing the risk means evaluating the likelihood and severity of harm, exposure and risk assessment steps, which informs decision making. Controls are then developed to reduce or eliminate the risk and make the workplace safer.
Hazards and Risks
Identifying hazards and risks means surveying the workplace to identify potential risks and sources of harm protecting workers. This means looking at obvious hazards like machinery or hazardous substances.
Risk identification includes reviewing past accident and near miss reports to identify potential hazards that may not be visible. You need to consider all aspects of work including remote workers and non routine activities which may introduce additional serious risk factors.
Analysis
Risk analysis is key to evaluating the impact of hazards by looking at uncertainties and their consequences. This is a systematic process that uses various risk assessment tools to assess operational risk.
To assess the risk you can:
- Identify hazards in the workplace.
- Analyse the risk for each hazard.
- Implement risk treatment to mitigate risk.
- Communicate the findings to stakeholders.
Assessing and Prioritising Risks
Organisations must assess each potential hazard that’s likelihood and severity to assess and prioritise risk.
By analysing the hazards they can determine injury severity and assign a risk rating using a risk matrix. This tool helps to visualise the relationship between the probability of occurrence and the impact of risk factors which is key to risk evaluation.
During the risk assessment process prioritising risk allows organisations to focus on the biggest issues and protect workers. Existing processes should be reviewed to ensure all the hazards identified and risks are identified and addressed.
Controls
After prioritising risk the next step for risk manager is to implement controls that mitigate risk control the identified hazards and protect workers, property and the environment. A safety professional should consider the following controls:
- Elimination: Remove the hazard where possible.
- Substitution: Replace the hazardous material with a safer alternative.
- Engineering Controls: Design the workplace to reduce risk exposure.
- Personal Protective Equipment (PPE): Provide the worker with the correct gear.
Implementing these controls ensures you are meeting the risk assessment and acceptable risk levels.
Also developing emergency procedures can support occupational health and occupational safety programs.
Documenting and Reviewing Risk Assessments
How can documenting and reviewing assessments ensure you understand and evaluate the risks and hazards in the workplace?
By doing a thorough risk assessment employers create a risk assessment plan that identifies the major hazards including biological hazards and physical hazards.
Documentation is a formal record of the assessment process, findings and conclusions. It’s accountability and compliance with legislation.
Reviewing assessments regularly allows you to address new hazards or changes to safety equipment. You must review your assessment regularly to keep the workplace safe.
Keeping documentation up to date not only meets the legal requirements but also a safety culture so all employees are aware of the risks and controls in place.
Risk Assessment Tools and Methods
Risk assessments use various tools and methods to identify and prioritise workplace hazards. These tools help risk managers to address chemical hazards, assess hazardous conditions and overall safety.
Here are a few:
- Risk Matrices – Visual tools to categorise risk by likelihood and severity.
- Heat Maps – Graphical representation of areas of concern.
- Bow-Tie Diagrams – Diagrams of the causes and consequences of risk.
- Risk Assessment Templates – Pre-filled templates to speed up the assessment process.
Using these tools helps with risk management and documenting near miss reports, allocating budget and integrating new processes to improve workplace safety.
Industry Risk Assessments
Industry specific risk assessments are required to address the unique hazards and regulations each industry faces.
For example the food industry needs to assess food safety and hygiene, construction sites need to assess worker exposure to manual handling and workplace safety, in healthcare professionals assess risks to patient safety and data security.
These assessments help identify operational risks important hazards where individuals can be harmed especially when using new equipment. By understanding these hazards you can implement controls to mitigate the risk.
This focused approach meets industry regulations and safety standards, keeps the workplace safe and ultimately protects employees and stakeholders from the inherent risks in their industry.
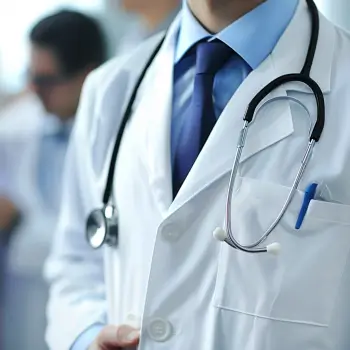
Common Issues and Limitations
One of the biggest challenges is identifying all the hazards during the risk assessment. This can lead to operational risks due to incomplete assessments such hazards and missed risks.
Also prioritising risk and allocating resources is another challenge. Organisations have limited financial resources and lack of expertise which can hinder the most effective risk assessment process.
Employee participation is crucial to get valuable insights but getting them to participate can be tough.
Key challenges are:
- Incomplete hazard identification
- Risk prioritisation
- Limited resources and expertise
- Getting employee participation
To overcome these challenges requires strategic planning and commitment from all levels of the organisation to improve the risk assessments.
Advanced Risk Assessment Methods
Organisations struggling with traditional risk assessments can benefit from advanced methods like quantitative risk assessment (QRA) and probabilistic risk assessment (PRA) which use statistical models to increase accuracy and reliability.
These methods use data to estimate the likelihood and impact of the risks identified, they are particularly useful in complex and high risk industries like nuclear and oil and gas.
By using QRA and PRA you can get more precise results to inform decision making and more effective risk management too.
But you need to recognise that these advanced methods require specialist expertise and resources which may not be available to all organisations.
Still they are worth considering for serious risk assessments.
Summary
A proper health and safety risk assessment is required to keep all safety related equipment in the workplace safe and employees well.
Organisations can manage risk by following a structured approach:
- Hazard Identification: Identify where harm can occur in the workplace.
- Risk Assessment: Evaluate the likelihood and severity of harm that can occur from each hazard.
- Control Measures: Eliminate or mitigate the identified risks.
- Review: Review and update the risk assessment regularly to keep up with changes in the workplace.
FAQs
How Often Should a Risk Assessment Be Done?
He says risk assessments should be done regularly, ideally annually or when there is a significant change in the workplace. Regular reviews ensure safety controls remain effective and compliant with current regulations and hazards.
Who Should Be Involved in the Risk Assessment?
A diverse team is required for effective risk management and assessments. Managers, employees and safety officers should be involved conducting risk assessments, sharing knowledge and experiences. This collective approach ensures thorough assessments and good practice across the organisation.
What Qualifications Do I Need to Do a Risk Assessment?
To do a risk assessment you need relevant qualifications such as occupational health and safety certifications, experience in hazard identification and knowledge of regulations. These qualifications ensure the risk management process is effective and compliant within the organisation.
Can Risk Assessments Be Done Remotely?
Yes, risk assessments can be done remotely. Many organisations use digital tools and virtual collaboration platforms. This way teams can assess hazards effectively and safety controls are still implemented even from afar.
What are the Legal Requirements for Risk Assessments?
Legal requirements for risk assessments vary by region but generally employers must identify hazards, assess risks and implement control measures. They must also document findings and review assessments regularly to stay compliant.
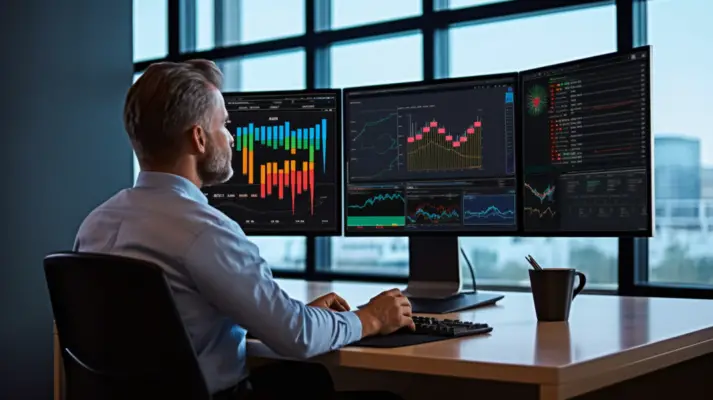
Summary
In summary, a health and safety risk assessment is required to identify and mitigate the hazards present in any environment.
By following a structured approach of hazard and risk identification and, risk analysis and prioritisation organisations can manage risk.
It may not be easy but advanced methods will get you more accurate results.
A proper risk assessment will protect individuals and create a safety culture across industries, for everyone involved
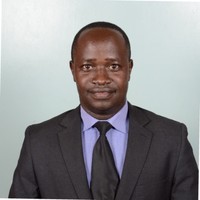
Chris Ekai is a Risk Management expert with over 10 years of experience in the field. He has a Master’s(MSc) degree in Risk Management from University of Portsmouth and is a CPA and Finance professional. He currently works as a Content Manager at Risk Publishing, writing about Enterprise Risk Management, Business Continuity Management and Project Management.