Collaborative robots, or cobots, are increasingly used in various industries to work alongside humans and enhance productivity. While these robots offer numerous benefits, such as increased efficiency and improved safety, they also bring about potential risks that need to be carefully assessed and managed.
Risk assessment is a crucial step in ensuring the safe operation of collaborative robots. It involves the systematic identification and analysis of hazards associated with their use.
Conducting a thorough risk assessment, organizations can identify potential dangers and implement appropriate control measures to mitigate them.
This article focuses on the importance of collaborative robot risk assessment and introduces a template to aid this process.
The template provides a structured approach for hazard identification and analysis, enabling organizations to assess the risks associated with collaborative robots comprehensively.
Following this template, businesses can ensure the safe integration of cobots into their operations while minimizing the likelihood of accidents or injuries.
Adopting a robust risk assessment methodology is essential for safely harnessing the benefits of collaborative robots in diverse industrial settings.

What is a Collaborative Robot?
Assessing risks with collaborative robots is an important aspect of ensuring the safety and effectiveness of these advanced machines.
Collaborative robots, also known as cobots, are designed to work alongside humans in a shared workspace, and this proximity can introduce unique risks that need to be carefully evaluated.
As a Robot Integrator, you play a pivotal role in applying industrial robotics. With your expertise, the tasks of robots, from mobile industrial robots to standard robots, become a seamless part of the workflow.
Whether it’s manipulating the robot’s wrist or managing the robot cycle, your responsibilities are vast and varied.
It’s about understanding the current robot in use, future robot control development, and the potential of collaborative robot applications.
Standards such as 10218-2:2011 – Robots, 4ISO/TS 15066 – Robots, 8SS-EN ISO 10218-1:2011 – Robots, and ANSI/RIA R15.06-2012 Robot Safety Standard guide the design and safety protocols for facilities with robot systems.
These principles for design also encompass complex product design and design requirements for robot features and application requirements. The safety of nearby workers, worker interaction, and the compatibility of human workers with robots are all integral parts of this process.
Understanding the operating space is another essential part of a robot application integrator’s job, whether determining the maximum space, restricted space, or the volume of space encompassing the self-propelled and self-contained robot.
It’s all about ensuring an efficient and safe robot work cell. The presence of various hazards, such as thermal, electrical, or hazardous sources. These must be assessed during automatic operations like arc welding or assembly operations.
External devices, from accessory devices, 3-position enabling devices, limiting devices, and portable control devices, all play a significant role in the safe operation of robots.
Safety considerations also extend to cobot manufacturers and their ancillary equipment. Ensuring the right risk reduction and safeguarding level is crucial to maintain an acceptable level of safety.
Assessing tasks, including additional tasks that may arise from integrating new technologies or operations, forms a crucial part of the risk assessment process. Particular attention must be given to the arm of cobots, as it often interacts directly with worker operators.
The contact pressure during this interaction, pressure testing, and managing the hazard combination should be incorporated into a clear, easy-to-understand, consistent methodology, such as the Task-based Risk Assessment Methodology.
Documentation plays a significant role in this process. Documenting risk and decisions made and maintaining an all-inclusive document for reference is crucial for maintaining transparency and ensuring continuous improvement.
This documentation also helps facilitate the design risk assessment stage and guides organizations such as Design Safety Engineering Inc.
Administrative safeguards and Organizational measures are vital aspects of managing risk. Tools like the Tool Center Point and external tools, depending on the cobot model, come into play in ensuring the safety of Numerically Controlled Machine Tools.
Whether in manual mode or automatic, these measures help manage the source of control and potential application-related sources of risk.
In conclusion, a Robot Integrator is crucial in managing and implementing robot systems.
From the standard robot to the most complex cobot, their job involves a wide variety of tasks, ensuring the safety and efficiency of the workplace while enabling the exciting future of industrial automation.
Conducting a thorough risk assessment, organizations can identify potential hazards and implement appropriate mitigation strategies to protect human workers and collaborative robots.
Assessing Risks with Collaborative Robots
Examining the potential hazards of collaborative robots allows for a comprehensive understanding of their risks in various work environments.
A collaborative robot risk assessment template can be utilized to assess these risks. This template helps identify and evaluate potential hazards specific to collaborative applications.
The assessment considers risk levels, safety measures, and functional safety requirements. It also considers applicable standards and guidelines related to collaborative robot use.
In addition, the design risk assessment focuses on worker interaction with the robot and ensures sufficient operating space for safe operation.
Implementing this template, organizations can effectively analyze and mitigate risks associated with collaborative robots, ensuring the safety of workers in their respective work environments.
Definition of Risk Assessment
Risk assessment is a crucial step in ensuring the safe operation of collaborative robots. It helps identify potential hazards and assess their likelihood and severity, allowing for implementing appropriate risk control measures.
Different types of risk assessments can be conducted, such as qualitative or quantitative assessments, depending on the level of detail required.
Using a risk assessment template designed for collaborative robots offers several benefits, including consistency in approach, time savings, and improved compliance with safety standards.
The Need for Risk Assessment
Conducting a thorough evaluation of potential hazards is essential to ensure the safe integration and operation of collaborative robots within various industrial settings.
The need for risk assessment arises from the complexity and potential risks associated with robotic applications.
Using a collaborative robot risk assessment template, organizations can follow a systematic approach to identify and mitigate potential hazards.
This includes considering factors such as the robot program, ISO standard requirements, and design risk assessment stage.
A task-based risk assessment methodology allows for a comprehensive evaluation of specific tasks performed by the collaborative robot, considering both operational and environmental factors.
In addition to technical measures, organizational measures are important in ensuring safe collaboration between humans and robots.
Therefore, conducting a thorough risk assessment is crucial for effectively implementing collaborative robot applications while maintaining worker safety.
Types of Risk Assessments
Different approaches can be used to evaluate the potential hazards associated with integrating and operating collaborative robots, including task-based evaluation methodologies and consideration of technical and organizational measures.
- Task-Based Evaluation Methodologies:
- These methodologies assess the potential risks associated with the robot’s tasks in an industrial setting.
- They involve analyzing factors such as robot motion, interaction with humans or other machinery, and the complexity of the task.
- Consideration of Technical and Organizational Measures:
- This approach involves considering both technical and organizational aspects when evaluating potential risks.
- Technical measures may include safety features incorporated by the robot manufacturer or recommended by regulatory bodies.
- Organizational measures involve ensuring proper training for the robot integrator, robot user, or robot application integrator.
Using these risk assessment types, stakeholders can systematically identify potential risks and implement appropriate control measures to mitigate them.
This allows for safer integration and operation of collaborative robots within a given industrial environment.
Benefits of Using a Risk Assessment Template for Collaborative Robots
Utilizing a standardized framework for evaluating potential hazards can provide a comprehensive and structured approach to identifying and managing the safety aspects associated with integrating and operating collaborative robots in industrial settings.
One way to achieve this is by using a risk assessment template designed for collaborative robots. This template serves as a guide, ensuring that all relevant factors are considered during the risk assessment process.
The benefits of utilizing a risk assessment template for collaborative robots are numerous. Firstly, it helps to ensure consistency across different assessments by providing a standardized format.
Secondly, it saves time and effort by providing pre-defined categories and questions that must be addressed. Lastly, it enhances accuracy by reminding assessors of potential hazards that may not have been considered otherwise.
To highlight these benefits further, consider the following table:
Benefits | Description |
---|---|
Consistency | Provides a standardized format for assessments |
Time-saving | Offers pre-defined categories and questions |
Accuracy | Reminds assessors of potential hazards |
Incorporating these keywords into the article section, readers will understand how to use a risk assessment template. It can be advantageous when evaluating the safety aspects of collaborative robots in industrial environments.
Hazard Identification and Analysis
This focuses on identifying hazards associated with collaborative robots and developing strategies to mitigate or eliminate these identified risks.
It also involves determining risk levels based on the severity and probability of occurrence and understanding the requirements for safety standards and regulations for robotic applications.
Systematically analyzing potential hazards, organizations can proactively address safety concerns and ensure compliance with established guidelines to create a safe working environment for both humans and robots.
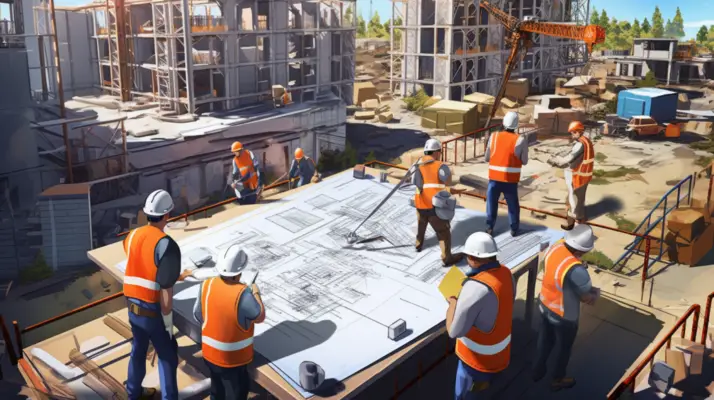
Identifying Hazards Associated With Collaborative Robots
Collaborative robots present potential hazards that must be identified to ensure a safe working environment.
One key hazard is using laser scanners, which detect human presence and stop the robot system motion if necessary.
Another hazard is the reliance on light curtains, which act as sensors to detect any intrusion into the robot’s workspace. It is crucial to assess these devices and ensure they function properly to prevent accidents.
Additionally, hazards may arise from the wide product range of collaborative robots available, each with its own unique features and capabilities.
Hazards associated with industrial robot applications must also be considered, such as potential risks during the assembly of robot systems or when operating mobile robots in dynamic environments.
Proper risk assessment is essential for identifying and mitigating these hazards to maintain a safe working environment with collaborative robots.
Developing Strategies to Mitigate or Eliminate Identified Risks
One effective approach to address the identified risks is to develop comprehensive strategies to mitigate or eliminate potential hazards associated with using collaborative robots.
These strategies should be based on the risk assessment template’s findings, which help identify specific hazards and their associated severity levels.
To mitigate or eliminate these risks, the following strategies can be employed:
- Robot Features: Implementing safety features such as force and speed limitations, collision detection systems, and emergency stop buttons can reduce the likelihood of accidents.
- Application Requirements: Ensuring the robot is used within its intended application limits and not subjected to tasks beyond its capabilities can minimize potential dangers.
- Design Safety Engineering: Incorporating safety engineering principles during robot design, such as providing protective barriers or designing robots with rounded edges, can reduce the risk of injuries.
Determining Risks Levels Based on Severity and Probability of Occurrence
After identifying the potential risks associated with collaborative robots, the next step is determining their levels based on severity and probability of occurrence.
This involves assessing the potential impact each risk could have on human safety and the likelihood of it occurring.
The severity refers to the extent of harm that could result from a particular risk, while the probability of occurrence measures the likelihood of that risk.
Combining these two factors can determine an overall risk level for each identified hazard.
This process allows organizations to prioritize risks and allocate resources to mitigate or eliminate them effectively.
The collaborative robot risk assessment template provides a structured approach to evaluating risks and ensures consistency in determining their levels across different scenarios.
Requirements for Safety Standards and Regulations for Robotic Applications
This focuses on three key points related to the requirements for safety standards and regulations for robotic applications.
Firstly, the ISO/TS 15066 standard is crucial for ensuring functional safety in industrial robot systems.
Secondly, when evaluating robotic applications, it is essential to consider applicable standards that address aspects such as electrical safety, machinery safety, and human-robot collaboration.
Lastly, risk assessments must encompass potential hazards associated with robotic applications, including collision risks, pinch points, entanglement hazards, and other factors that can harm humans or the environment.
ISO/TS 15066 Standard for Functional Safety of Industrial Robot Systems
The ISO/TS 15066 standard provides guidelines for ensuring the functional safety of industrial robot systems. These guidelines are important for the safe operation of collaborative robots.
The standard outlines specific requirements and recommendations to mitigate risks associated with various robot applications.
It covers maximum allowable forces and pressures, protective measures, speed and separation monitoring, contact force and pressure limiting.
Following these guidelines ensures the safe use of industrial robot systems.
Applicable Standards to Consider When Evaluating Robotic Applications
Applicable standards, such as ISO/TS 15066 and ANSI/RIA R15.06 robot safety standards, are crucial in evaluating robotic applications by providing specific guidelines and requirements for ensuring functional safety.
These standards are essential for facilities with robot systems as they outline principles for design, design requirements, and robot features. They also address the future development of robot control and task-based risk assessment methodology.
Design Safety Engineering Inc focuses on robots and robotic devices’ safety requirements for collaborative robots.
Potential Hazards That Must be Considered in Risk Assessments
When evaluating robotic applications, it is crucial to consider the potential hazards that may arise.
These hazards can include thermal, electrical, and hazard combinations that occur during automatic operations such as arc welding or assembly operations.
It is important to identify the hazardous sources and assess their risks accordingly.
Additionally, control measures should be implemented to mitigate these risks, such as using a portable control device as a control source for the robot.
Frequently Asked Questions
Are there any specific industry standards or regulations that govern the risk assessment process for collaborative robots?
Yes, specific industry standards and regulations govern the risk assessment process for collaborative robots. These standards ensure the safety of human workers and include ISO 10218 and ISO/TS 15066.
What are the key factors when conducting a risk assessment for collaborative robots in a manufacturing setting?
When conducting a risk assessment for collaborative robots in a manufacturing setting, key factors include identifying potential hazards, assessing the severity of risks, determining control measures, and ensuring compliance with relevant safety standards and regulations.
How can collaborative robot risk assessments help reduce workplace accidents and improve overall safety?
Collaborative robot risk assessments can reduce workplace accidents and improve safety by identifying potential hazards, evaluating their severity and likelihood, implementing appropriate control measures, and monitoring their effectiveness.
This systematic approach ensures proactive hazard management and continuous improvement in occupational safety.
What are some common challenges or obstacles faced during the risk assessment process for collaborative robots?
Common challenges faced during the risk assessment process for collaborative robots include determining appropriate safety measures.
Identifying potential hazards and risks, ensuring compliance with industry standards, integrating human-robot interactions, and adapting to changing technology.
Are any best practices or guidelines available to help organizations implement and maintain a collaborative robot risk assessment program?
Best practices and guidelines are available to help organizations effectively implement and maintain a collaborative robot risk assessment program.
These resources provide analytical, detailed, and concise information on the steps and processes of conducting a comprehensive risk assessment for collaborative robots.
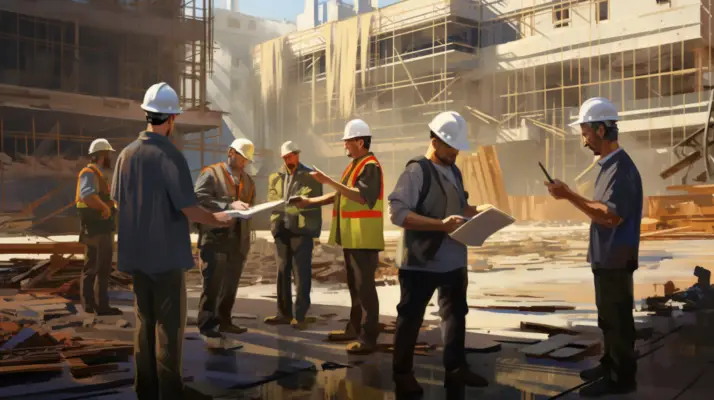
Conclusion
The collaborative robot risk assessment template is valuable in identifying and analyzing potential hazards associated with these advanced machines.
Conducting a thorough risk assessment, organizations can mitigate risks and ensure the safety of both human workers and collaborative robots in various work environments.
This template provides a systematic approach to hazard identification and analysis, enabling companies to make informed decisions regarding implementing and operating collaborative robots.
This creates safer and more efficient working conditions for all involved parties.
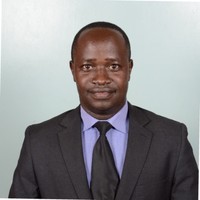
Chris Ekai is a Risk Management expert with over 10 years of experience in the field. He has a Master’s(MSc) degree in Risk Management from University of Portsmouth and is a CPA and Finance professional. He currently works as a Content Manager at Risk Publishing, writing about Enterprise Risk Management, Business Continuity Management and Project Management.