In the futuristic landscape of automation and artificial intelligence, robots have transcended science fiction to become an integral part of our daily lives.
Robots are performing tasks with increasing sophistication, from manufacturing floors to our living rooms. However, as their presence grows, so too does the concern over the potential risks associated with their operation.
The very characteristics that make robots so invaluable – precision, efficiency, and the ability to perform tasks in hazardous environments – can also present unique challenges and hazards. The possibility of malfunctions, software bugs, or even deliberate misuse can lead to situations where both people and property may be at risk.
“Robot Risk Assessment” is no longer a niche concern, but a vital process that ensures the safety, reliability, and ethical use of robotic systems in various industries. It’s a complex field that spans legal, ethical, and technical dimensions, requiring careful consideration and collaboration among experts.
In this blog post, we will delve into the intricacies of Robot Risk Assessment, exploring what it means, why it matters, and the key factors involved in creating a secure robotic ecosystem.
Whether you are a robotics professional, a policymaker, or simply someone fascinated by the rise of machines, this exploration will offer insights and knowledge into one of the most crucial aspects of modern robotic technology.
Join us as we navigate the fascinating world of robots, shedding light on the challenges and rewards of risk assessment and illuminating the path to a safer, more responsible future in robotics.
This article comprehensively examines robot risk assessment, focusing on the types of robots, potential hazards, and methods for evaluating risks associated with robotics systems.
The objective of this research is to analyze and assess the various risks that arise from the utilization of robots in different industries.
Definition of Robot Risk Assessment
Robot risk assessment is a critical process that involves identifying and evaluating potential risks associated with the use of robots. This assessment plays a crucial role in ensuring the safety of both humans and the robots themselves in various applications.
In robotics and machinery safety, there are several factors to consider to ensure the well-being of workers and the efficient operation of the systems.
One important aspect is the assessment of robot operations, which involves evaluating the potential hazards and risks associated with using robots in various industrial applications. This assessment helps in identifying the necessary control measures and implementing them effectively.
Robot manufacturers and integrators play a crucial role in ensuring the safety of robot systems. They are responsible for the robots’ design, assembly, and integration, taking into account the specific requirements of the application industry standards.
They need to consider factors such as the maximum and restricted space within which the robot will operate its tasks, and the proximity to nearby workers.
Control means and devices also play a significant role in maintaining safety in robot systems. This includes using a portable control device that allows the operator to control the robot’s motion and actions. Quality control of the robot system is also essential to ensure all safety measures are in place and functioning correctly.
In addition to control measures, other organizational and administrative controls need to be implemented. These may include using ancillary equipment, electrical and protective equipment, and establishing organizational measures to ensure safe operations.
It is also important to comply with applicable standards and regulations to ensure the safety of robot systems. These standards may vary depending on the industry and application, but they provide guidelines and requirements for risk reduction and safety measures.
Overall, the safety of robot systems is a multi-faceted approach that requires careful consideration of various factors. By following proper design, assessment, and control measures, robot manufacturers, integrators, and operators can ensure industrial robot systems’ safe and efficient operation.
One key area of concern in robot and machinery safety is the stability of the machinery in workplaces. Machinery instability can lead to accidents and injuries, so addressing this issue during the design and assembly process is important.
Design solutions such as adding stabilizing features, reinforcement structures, and anti-vibration measures can help improve the stability of machinery.
Furthermore, using numerically controlled machine tools introduces its own set of safety considerations. Machine manufacturers must ensure that the complete machine, including the application tools, meets safety standards and regulations.
The Tool Center Point, the reference point for the tool’s position, must be accurately defined to minimize the risk of accidents.
Additionally, specific safety measures must be taken in certain industries where explosive environments are present to prevent any potential ignition sources and minimize the risk of explosions.
A 3-step process can be followed to address these safety concerns: identify the hazards, assess the risks, and implement risk reduction measures. This process involves conducting a risk assessment (RA) to identify potential hazards and evaluate their risk level.
Examples of common hazards include collision between the robot and humans, entanglement in moving parts, and exposure to hazardous substances or environments. Once the hazards have been identified, appropriate control measures can be implemented to reduce the risks to an acceptable level.
In conclusion, ensuring the safety of robot and machinery systems requires a comprehensive approach that involves careful design, assessment of hazards and risks, implementation of control measures, and compliance with applicable standards and regulations.
By considering all these factors, companies can create a safe working environment for their employees and optimize the performance of their robot and machinery systems.
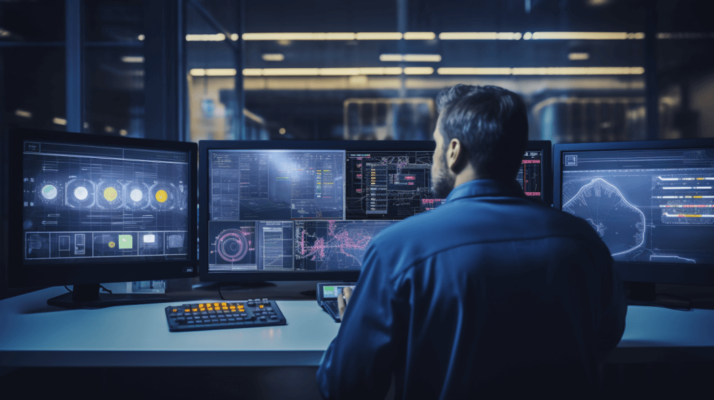
Benefits of Robot Risk Assessment
One advantage of conducting risk assessments for robotic systems is identifying potential hazards and mitigating them to ensure the safety of both humans and the surrounding environment.
Robot risk assessment plays a crucial role in robotics, particularly in industrial settings where industrial robots are widely used. By evaluating the potential hazards associated with robot systems, organizations can implement appropriate safety measures and protective measures to prevent accidents and injuries.
Risk evaluation allows for a thorough understanding of the risks involved in robotic systems, enabling organizations to meet the safety requirements and standards set by regulatory bodies.
These assessments provide valuable insights into the potential risks and help in developing strategies to minimize these risks, ultimately leading to improved safety and protection in robotic operations.
Types of Robots
This will focus on the various types of robots: industrial, mobile, collaborative, and autonomous robotic systems.
Industrial robots are typically used in manufacturing settings to automate repetitive tasks. They are programmed to perform specific actions with precision and efficiency, making them ideal for welding, painting, and assembly tasks.
Mobile robots, on the other hand, are designed to move and navigate in different environments. Depending on the terrain they must traverse, they can be equipped with wheels, tracks, or legs. Mobile robots are commonly used in warehouses, hospitals, and outer space exploration.
Collaborative robots, or cobots, are designed to work alongside humans, sharing the same workspace and collaborating on tasks.
Unlike traditional industrial robots, cobots have sensors and safety features that allow them to interact with humans safely. They are often used in industries where human-robot collaboration is necessary, such as assembly lines and healthcare.
Lastly, autonomous robotic systems can perform tasks independently, relying on artificial intelligence and advanced sensors to make decisions and execute actions.
These robots can operate without human intervention and are commonly used in applications such as autonomous vehicles, drones, and robotic vacuum cleaners.
Each type of robot has its own unique capabilities and applications, contributing to the advancement of automation and robotics in various industries.
Industrial Robots
Industrial robots have become increasingly prevalent in manufacturing due to their efficiency and productivity. These robots are designed to perform various tasks traditionally done by human workers. They are automated machines that can perform repetitive tasks with high precision and accuracy.
Industrial robots are used in different stages of the manufacturing process, including assembly, welding, painting, and material handling. They have advanced sensors and control systems to ensure safe and efficient operation.
However, the use of industrial robots also poses certain risks to workers. Therefore, conducting a thorough risk assessment of these robots and their associated equipment and processes is crucial.
This assessment includes analyzing the design and control of the robots, identifying potential hazards, and implementing necessary safety measures to prevent injuries to workers.
Mobile Robots
Mobile robots are increasingly being deployed in various industrial settings for material transportation, inventory management, and surveillance tasks.
These robots offer numerous benefits, including increased efficiency and productivity. However, they also pose potential risks to workers and equipment.
To ensure safe operation, it is crucial to implement adequate safety measures and conduct a thorough risk assessment process. Some key risk reduction measures for mobile robots include:
- Providing appropriate safety equipment, such as barriers and warning signs, to prevent collisions between the robots and humans.
- Implementing emergency stop systems and interlocks to halt robot operations in emergencies quickly.
- Regularly inspecting and maintaining the robotic systems to minimize the risk of malfunctions or failures.
Collaborative Robots
Collaborative robots, also known as cobots, have gained significant attention in recent years due to their ability to work alongside humans in various industrial applications. As collaborative robotics becomes more prevalent, ensuring robot safety is paramount.
Robot risk assessment is crucial in identifying potential hazards and implementing appropriate control measures. This assessment evaluates the risks of robot arms and their interaction with human operators.
By using an assessment tool, robot users can systematically identify, evaluate, and mitigate potential risks in industrial environments.
This process helps create safe work environments and ensures compliance with regulatory requirements.
Furthermore, thorough risk assessments enable organizations to implement necessary safety measures and protocols for collaborative robots, ultimately enhancing overall robot safety and minimizing the risk of accidents or injuries.
Autonomous Robotic Systems
Autonomous robotic systems have emerged as a prominent field of research and development, focusing on robotic entities’ independent operation and decision-making capabilities.
These systems are designed to perform tasks without human intervention, making them increasingly prevalent in various industries.
However, integrating autonomous robotic systems has inherent risks that must be assessed and mitigated.
- Hazard identification: Identifying potential risks and hazards associated with the operation of autonomous robotic systems is crucial. This involves conducting thorough assessments of the system’s components, functions, and interactions with humans and the environment.
- Risk of injury: Determining the potential for human injury or damage to property is an essential aspect of robot risk assessment. This involves evaluating the system’s speed, force, proximity to humans, and the potential for collisions or entrapment.
- Principles for design: Implementing safety principles during the design phase of autonomous robotic systems can significantly reduce the risk of accidents. This includes incorporating protective measures such as emergency stop buttons, safety barriers, and fail-safe mechanisms.
Potential Hazards of Robotics Systems
This discussion focuses on the potential hazards associated with robotics systems. Specifically, it addresses repetitive tasks and ergonomic hazards, human injury resulting from robot motion control algorithms, unforeseen interactions with people or objects in the environment, and security issues arising from poorly monitored network connections.
Repetitive tasks and ergonomic hazards can lead to musculoskeletal disorders and physical discomfort for operators. These hazards occur when operators are required to perform the same motion repeatedly or when the system design does not consider proper ergonomics.
Human injury from robot motion control algorithms can occur due to errors in programming or inadequate safety measures. If the algorithms controlling the robot’s motion are not properly designed or safety measures are not in place, there is a risk of injury to humans near the robot.
Unforeseen interactions with people or objects in the environment can pose a risk to humans and the robot. If the robot cannot detect and respond appropriately to unexpected interactions, it can cause harm to humans or damage to objects in its surroundings.
Poor monitoring of network connections can expose the system to security breaches and unauthorized access. If the connections to the robot’s network are not properly monitored, there is a risk that malicious actors could gain access to the system and cause harm or disrupt its operation.
Repetitive Tasks and Ergonomic Hazards
Repetitive tasks and ergonomic hazards in relation to robot risk assessment have been widely studied in academic literature.
These studies aim to identify and mitigate the potential risks associated with repetitive tasks robots perform in industrial settings. The evaluation of ergonomic hazards is crucial in ensuring the safety and well-being of human workers.
Some evaluation items in the assessment of repetitive tasks and ergonomic hazards include:
- Task repetition rate: The frequency at which the robot performs a task can contribute to developing chronic human injuries, such as musculoskeletal disorders.
- Loading station design: The design of the loading station where robots interact with human workers significantly minimises ergonomic hazards. Considerations such as height, reachability, and accessibility are crucial in preventing injuries.
- Module loading techniques: The methods used for loading modules onto robots can impact the ergonomic hazards human workers face. Efficient loading techniques can reduce the risk of injuries caused by lifting heavy objects repeatedly.
Understanding and addressing these repetitive tasks and ergonomic hazards is essential in ensuring the safe use of industrial robotics in various applications.
Human Injury from Robot Motion Control Algorithms
Human injury from implementing motion control algorithms in robotic systems has been a concern in academic research. The risk assessment of robots is crucial to ensure the safety of human operators and prevent accidents.
Robot motion control algorithms play a significant role in determining the movement and actions of robots, and any flaws or errors in these algorithms can potentially lead to human injury.
Various robotics and international standards have been developed to mitigate this risk to guide the assessment of robots and the implementation of safety measures. Table 1 provides an overview of some common mitigation measures that robot manufacturers can implement to minimize the risk of operator-injured robot accidents.
These measures include protective barriers, emergency stop buttons, and safety interlocks. The assessment of robots should encompass a thorough evaluation of the motion control algorithms to identify any potential hazards and ensure compliance with safety standards.
Mitigation Measures | Description |
---|---|
Protective barriers | Physical barriers that separate humans from the robot workspace to prevent accidental contact |
Emergency stop buttons | Buttons that can be pressed to immediately halt the robot’s motion in case of an emergency |
Safety interlocks | Mechanisms that ensure certain conditions are met before the robot is allowed to perform an action |
Speed and force limitations | Limiting the maximum speed and force exerted by the robot to reduce the risk of injury |
Safety training and education | Providing operators with proper training and education on the safe use and operation of the robot |
Unforeseen Interactions with People or Objects in the Environment
Unforeseen interactions with individuals or objects within the surrounding environment pose a potential challenge in ensuring the safety and effectiveness of motion control algorithms implemented in robotic systems.
A comprehensive robot risk assessment should be conducted to understand better and mitigate these risks.
This assessment should consider various factors related to the interactions between the robot and its environment, including people, objects, and machinery. Examples of potential interactions include collision with a person, entanglement with an object, or exposure to hazardous materials or biological agents.
The evaluation of these interactions should consider the specific characteristics of the robot, the environment in which it operates, and the loading conditions it may encounter.
By thoroughly assessing and addressing these potential risks, the safety and effectiveness of motion control algorithms can be enhanced in robotic systems.
- Consideration of potential collision risks with people or objects
- Evaluation of the risk of entanglement with objects in the environment
- Assessment of exposure risks to hazardous materials or biological agents
Security Issues from Poorly Monitored Connections to Networks
Inadequate monitoring of network connections can give rise to security issues, compromising the integrity and confidentiality of data transmitted by robotic systems. It is crucial to assess the risks associated with robot systems to ensure the safety and security of operations.
Security issues arise when network connections are poorly monitored, leaving room for unauthorized access or data breaches.
As part of the robot risk assessment, evaluations should be conducted to identify potential vulnerabilities in the network infrastructure. This includes assessing the control and robot programs for potential security loopholes.
Additionally, electrical hazards should be considered, as they can arise from poor network monitoring, potentially leading to safety risks for the industrial robot system and its surrounding environment.
Methods for Evaluating Risks Associated with Robotics Systems
This discussion focuses on the process of identifying potential risks and hazards associated with robotics systems, as well as establishing a risk assessment process.
Identifying potential risks and hazards is a crucial step in ensuring the safety and reliability of robotics systems. This involves analyzing the various components and functionalities of the system to identify any potential sources of danger or vulnerability.
Once potential risks and hazards are identified, a comprehensive risk assessment process can be established to evaluate these risks’ likelihood and severity and develop appropriate mitigation strategies.
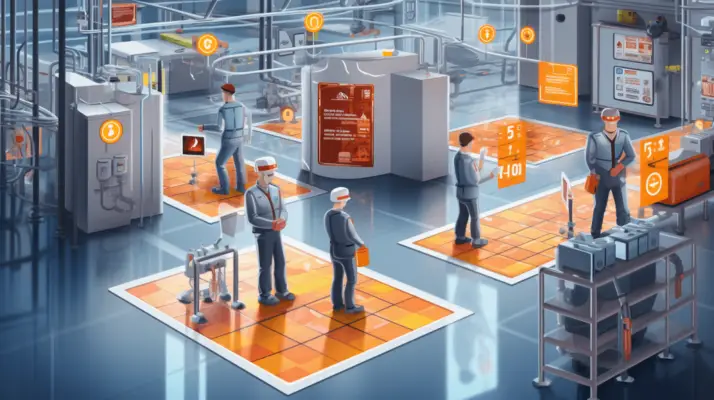
Identifying Potential Risks and Hazards
One key step in the process of robot risk assessment involves the identification of potential risks and hazards that may arise. This step is crucial in ensuring a proper risk assessment, allowing for the implementation of necessary safety measures.
Some key factors to consider when identifying potential risks and hazards in an industrial robot application include:
- Tool hazards: Assessing the potential dangers associated with the tools or end-effectors used by the robot, such as sharp edges or moving parts.
- Space limitations: Evaluate the workspace where the robot will operate to identify any potential obstructions or restricted areas that may pose risks.
- Light curtains: Analyzing the effectiveness of light curtains or other safety devices to detect human presence and ensure safe operation.
Establishing a Risk Assessment Process
Establishing a systematic and structured process is essential for comprehensively evaluating potential hazards and risks in industrial robotics.
This process involves assessing various aspects of robot operations, including the robot wrist, self-propelled and self-contained robot, current robot, and other industrial robot solutions.
Control engineering principles are utilized to analyze the functionality and safety of the robot, considering factors such as the operating space and worker interaction.
Additionally, a thorough examination of peripheral equipment, such as sensors and safety devices, is crucial to ensure the system’s overall safety.
Compliance with electrical safety standards is also essential to minimize the risk of electrical hazards.
Frequently Asked Questions
What Are Some Common Challenges Faced in Implementing a Robot Risk Assessment Program?
Some common challenges faced in implementing a risk assessment program for robots include determining the appropriate level of risk, identifying potential hazards and their likelihood, addressing uncertainties, and ensuring compliance with regulatory requirements.
Are There Any Regulatory Frameworks or Standards in Place for Robot Risk Assessment?
Regulatory frameworks and standards play a crucial role in ensuring the safety and effectiveness of various technologies.
In the case of robot risk assessment, it is important to examine if any such frameworks or standards exist to guide the process.
How Do Organizations Typically Address the Potential Risks Posed by Collaborative Robots (Cobots)?
Organizations typically address the potential risks posed by collaborative robots (cobots) through a systematic risk assessment process.
This involves identifying and evaluating hazards, implementing safety measures, and monitoring the performance of cobots to ensure ongoing safety.
Can You Provide Examples of Real-Life Incidents or Accidents Caused by Robots That Highlight the Need for Effective Risk Assessment?
Real-life incidents and accidents caused by robots serve as examples that emphasize the necessity for effective risk assessment.
These incidents highlight the importance of identifying and mitigating potential hazards associated with robotic systems.
What Role Does Human Error Play in Robot-Related Accidents, and How Can It Be Mitigated Through Risk Assessment?
Human error can play a significant role in robot-related accidents. Effective risk assessment can help mitigate this by identifying potential human error factors and implementing appropriate safeguards, training, and procedures to minimize the likelihood of errors occurring.
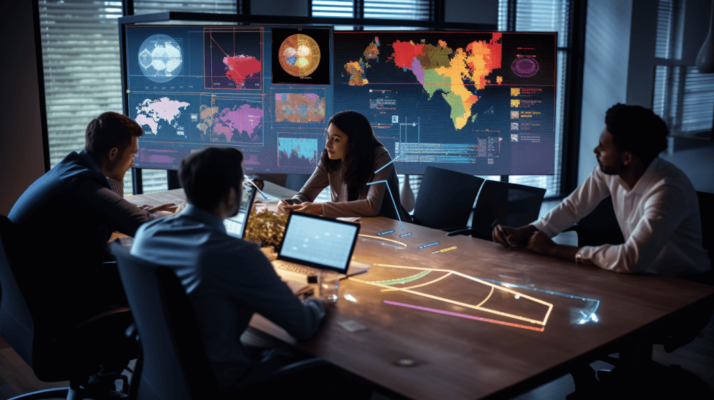
Conclusion
In conclusion, robot risk assessment is a crucial process in ensuring the safety and effectiveness of robotics systems.
Organizations can identify and mitigate risks to protect humans and robots by evaluating the potential hazards associated with different types of robots.
Various methods, such as hazard analysis and risk matrix, can be utilized to assess the risks involved thoroughly.
Through a detail-oriented and analytical approach, organizations can make informed decisions and implement necessary safety measures to minimize the risks associated with robotics systems.
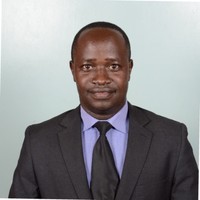
Chris Ekai is a Risk Management expert with over 10 years of experience in the field. He has a Master’s(MSc) degree in Risk Management from University of Portsmouth and is a CPA and Finance professional. He currently works as a Content Manager at Risk Publishing, writing about Enterprise Risk Management, Business Continuity Management and Project Management.