Machine safety is an essential part of any industry, and the ISO 12100:2010 risk assessment template is a valuable tool to ensure the safety of machinery and equipment. According to research by the United Nations Industrial Development Organization (UNIDO), machinery and equipment accidents account for 10-20% of workplace accidents worldwide.
Organizations must adhere to the ISO 12100:2010 standard to reduce the risk of these accidents, which offers a structured approach to identify hazards, analyze risks, estimate probability and severity, and effectively manage residual risks.
The ISO 12100:2010 risk assessment template is composed of several key components. It begins with identifying hazards from various sources, such as human error, equipment failure, or environmental conditions. After hazard identification, organizations must analyze the risks to determine the probability and severity of their occurrence.
Subsequently, the organization must evaluate and manage residual risk by implementing appropriate risk reduction measures. Additionally, the template must also adhere to legal requirements and regulatory standards.
This article aims to equip readers with valuable knowledge and resources to enhance safety practices in their respective industries. It provides insights into implementing an effective machine safety program and guidance on conducting ISO 12100 risk assessments.
Understanding and following the ISO 12100 risk assessment template, organizations can ensure the safety of their machinery and reduce the risk of workplace accidents.
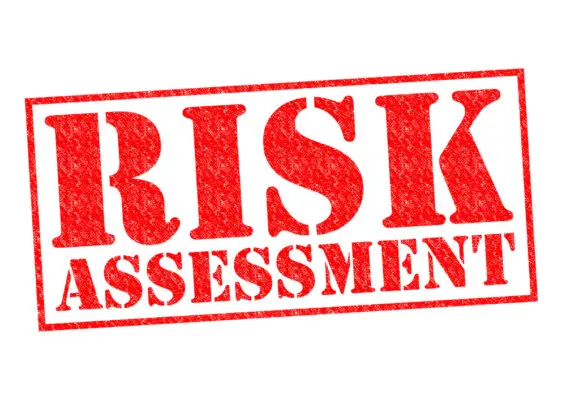
Definition of Risk Assessment
Using a risk assessment template such as ISO 12100 can provide numerous benefits to organizations.
Firstly, it helps ensure a systematic and standardized approach to risk assessment, allowing for consistency and comparability across different projects or industries.
Understanding the safety of machinery, particularly in the context of risk management, is a critical step in Occupational Health and Safety Management. Principles for design, as outlined in standards such as ISO 12100:2010 Safety Of Machinery, dictate that any potential failure mode, whether common cause failures or component failure, must be accounted for in the machine design process.
These principles guide machine builders from the design stage to installation. By considering factors such as space limit and the application of safety devices, they ensure that machinery is designed to minimize accident risks. This protects the machines from damage and safeguards the operators’ health.
Procter Machine Safety and Procter Machine Guarding, widely recognized in North America, have detailed safety requirements, including regulations about sharp edges, control actuators, and the design of displays.
Their guidance extends to the adequate use of control circuit devices, such as safety circuits with safety relays, and the appropriate management of power sources, including fluid power and the electrical power supply.
In addition to these design methods, other qualitative and basic terms must be understood in business terms.
This requires a combined knowledge of hazards, such as radiation, thermal, and other substance hazards, catalogued by the American Society of Safety Engineers.
The safety of machinery assessment includes looking at direct hazards and the combination of hazards to achieve an adequate risk reduction.
This often involves using additional tools, such as Compliance InSight Consulting’s unlocked spreadsheet tool, a visual tool for assessing the design and protective measures.
It’s important to note that risk assessment isn’t a one-time action. Annual operations reviews, constant noise comparison, and checking emission values are all part of maintaining compliance. It’s not just about the assurance of safety – the benefits of safety practices also include reduced damage to machinery and decreased danger for humans.
The principles of functional safety extend to control methods and the responsibilities of control systems designers. A critical part of this is understanding fault conditions, delivery conditions, and the degree of probability of potential hazards.
This basis of risk analysis forms the groundwork for successful risk reduction strategies, as detailed in various articles about risk reduction.
Effective machine safety is a comprehensive endeavour involving various aspects – from the design of machines, control of machines, and consideration of obvious hazards to the application of the concept of safety.
Industry best practices, adherence to safety standards, and continuous performance monitoring are essential to maintaining a safe and productive operational environment.
Additionally, a risk assessment template can save time and resources by providing a framework that guides the identification, analysis, and evaluation of risks, reducing the need for starting from scratch for each assessment.
Overall, the ISO 12100 risk assessment template provides a comprehensive and widely recognized framework for organizations to effectively manage risks in their operations.
Benefits of a Risk Assessment Template
One advantage of utilizing a Risk Assessment Template is its ability to provide a structured framework for evaluating and managing potential risks, enhancing efficiency and effectiveness in the risk assessment.
The ISO 12100 risk assessment template is a valuable tool for organizations involved in machinery design and manufacturing, as it helps identify hazards, assess risks, and implement appropriate risk reduction measures.
Organizations can use a template to ensure that all necessary aspects of the risk assessment process are considered and documented consistently. This promotes a systematic approach to safety, reducing the likelihood of accidents and injuries associated with machinery operations.
The template also facilitates communication and collaboration among stakeholders by providing a common language and format for discussing and addressing safety concerns. Overall, incorporating a risk assessment template can greatly improve the quality and reliability of machinery risk assessments.
Benefits of Utilizing a Risk Assessment Template |
---|
Provides a structured framework for evaluating and managing potential risks |
Enhances efficiency and effectiveness in the risk assessment process |
Helps identify hazards and assess risks consistently |
Facilitates communication and collaboration among stakeholders |
Promotes a systematic approach to safety and risk reduction |
Overview of ISO 12100 Risk Assessment Template
Efficiently evaluating and managing potential risks becomes more attainable using a structured framework such as the ISO 12100 risk assessment template. This template promotes a systematic approach to safety and instills confidence in the reliability of machinery risk assessments.
The ISO 12100 risk assessment template provides a comprehensive and standardized method for identifying hazards, assessing risks, and implementing control measures to mitigate those risks. It guides users through each step of the risk assessment process, from hazard identification to determining residual risk.
Following the principles of risk assessment outlined in the ISO 12100 standard, organizations can ensure that all relevant risks are considered and addressed. This template also encourages the incorporation of expert knowledge and the consideration of foreseeable misuse or abnormal operating conditions.
The ISO 12100 risk assessment template offers a structured and thorough approach to evaluating and managing potential risks, resulting in a more accurate assessment of potential harm.
Hazard Identification & Risk Analysis
Firstly, the sources of hazards need to be identified to assess and manage risks effectively.
Secondly, a systematic process is required for identifying hazards and associated risks, which involves gathering information, conducting inspections, and analyzing data.
Thirdly, various mechanical hazards, such as moving parts, electrical systems, and noise, should be considered during hazard identification.
Lastly, different methodologies, such as fault tree analysis and failure mode and effects analysis, can be employed to analyze potential hazards and risks in a structured and systematic manner.
Sources of Hazards
Identifying sources of hazards is crucial in the ISO 12100 risk assessment template as it allows for objectively evaluating potential risks without relying on subjective judgments. By identifying the source of harm, such as a machine malfunction or a chemical substance, the risk assessment procedures can focus on assessing the potential dangers associated with that specific source.
This detailed risk estimation enables the elimination of hazards at their root rather than addressing the cumulative harm they may cause. By incorporating the principle of hazard analysis, the ISO 12100 risk assessment template ensures that all relevant hazards are identified and considered in the risk assessment process.
This thorough identification of sources of hazards contributes to a more systematic and comprehensive approach to risk assessment.
Process for Identifying Hazards and Risks
An essential step in ensuring workplace safety involves a systematic and comprehensive process for identifying hazards and assessing associated risks. This risk assessment process follows the ISO 12100 standard for machinery risk, which provides guidelines for the design of machinery to ensure the safety of operators and other personnel.
The process includes the identification of hazards, the estimation of risks through the use of a risk graph, and the implementation of controls to achieve sufficient risk reduction.
Following this process, organizations can ensure that their machinery is designed and operated in compliance with safety standards, minimizing the potential for accidents and injuries.
The table below illustrates the steps involved in the process of risk assessment and their corresponding functions:
Step | Function |
---|---|
1. Identification of hazards | Identify potential sources of harm |
2. Risk estimation | Assess the likelihood and severity of harm |
3. Implementation of controls | Implement measures to reduce or eliminate risks |
Systematically following this process, organizations can effectively manage and mitigate risks, ensuring the safety of their workers and compliance with safety regulations.
Types of Mechanical Hazards to Consider
One aspect to consider when identifying hazards in the workplace is the various types of mechanical hazards that could pose a risk to workers. These hazards can arise from using equipment and tools and the operations involved in a particular process.
Following logical steps and familiarizing oneself with basic terminology is important to better understand these hazards.
When evaluating the probability of occurrence and the potential risk associated with mechanical hazards, it is essential to consider the type B or type C safety standards outlined in ISO 12100. To aid in this process, a bullet list of five types of mechanical hazards can be used:
- Moving parts: such as rotating machinery or conveyor belts.
- Energy sources: including electrical, hydraulic, or pneumatic systems.
- Falling objects: from shelves, storage areas, or elevated platforms.
- Noise and vibration: resulting from the operation of equipment.
- Ergonomic hazards: related to repetitive tasks or poor workstation design.
Methodologies for Analyzing Potential Hazards & Risks
Methodologies for analyzing potential hazards and risks involve systematic approaches that aid in identifying and evaluating the various aspects of workplace safety, ensuring a comprehensive understanding of the potential dangers and enabling effective strategies for mitigation.
One such methodology uses a risk assessment template, which provides a structured framework for assessing the risks associated with machinery and equipment. This template follows ISO standards and guides risk reduction by considering factors such as machine failure, potential harm, and operating conditions.
Using this template, organizations can assign risk levels to different hazards and calculate a risk score, which helps determine the priority for implementing control measures.
The goal is to achieve an acceptable risk level by implementing adequate risk reduction measures that align with the organization’s safety objectives and legal requirements.
Estimating Probability & Severity of Occurrence
In hazard identification and risk analysis, estimating the probability and severity of occurrence is crucial. There are several principles for assessing probability and severity, such as historical data analysis and expert opinions. These principles help in determining the level of risk associated with a hazard.
Establishing a risk level matrix is an important step in the process. This matrix provides a systematic framework for categorizing risks based on probability and severity. This matrix allows organizations to prioritize risk mitigation efforts and allocate resources accordingly.
Mitigating high-risk events requires the implementation of various strategies. These strategies can include implementing safety measures, redesigning processes or equipment, and providing training and education to employees. By taking these actions, organizations can reduce the likelihood and impact of high-risk events.
Principles for Assessing Probability and Severity
The assessment of probability and severity in the context of the ISO 12100 risk assessment template involves applying objective criteria and standardized measures to ensure an unbiased evaluation of the potential risks. To achieve this, the following principles for assessing probability and severity are followed:
- Principles for assessing probability:
- Use historical data, statistical analysis, and expert judgment to estimate the likelihood of a hazard occurring.
- Consider factors such as frequency, duration, and intensity of exposure to determine the probability.
- Consider the effectiveness of existing protective measures in reducing the probability of the hazard.
- Principles for assessing severity:
- Evaluate the potential consequences of a hazard, including injuries, fatalities, and damage to property or the environment.
- Consider the severity of potential injuries, such as minor, serious, or permanent disabilities.
- Assess the potential economic and environmental impacts resulting from the hazard.
Adherence to these principles, the ISO 12100 risk assessment template ensures a comprehensive evaluation of risks, facilitating the identification of appropriate risk reduction and protective measures.
Establishing a Risk Level Matrix
To establish a risk level matrix, one must consider various factors related to the potential hazards, their probability of occurrence, and the severity of their consequences. The ISO 12100 risk assessment template provides a systematic approach for evaluating these factors and determining the appropriate risk level.
The matrix is typically divided into categories, with probability and severity forming the axes. The probability is assessed based on the likelihood of an event occurring, while the severity is determined by the potential harm or damage resulting from the hazard.
Assigning numerical values or using qualitative descriptions, the risk level can be determined by intersecting the probability and severity values. This matrix helps prioritize hazards and guides decision-making regarding risk reduction measures.
It clearly and objectively represents the risks involved, enabling organizations to effectively manage and mitigate potential dangers.
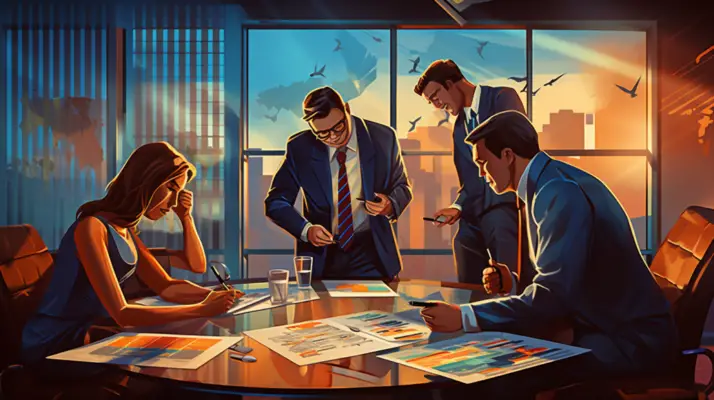
Strategies for Mitigating High-Risk Events
Strategies for mitigating high-risk events involve proactive measures aimed at reducing the likelihood and severity of potential hazards, ensuring the safety and well-being of individuals, and minimizing the impact on organizations.
These strategies are crucial in the context of the ISO 12100 risk assessment template, which provides a structured procedure for risk assessment. By following this template, organizations can identify and assess potential risks, determine the appropriate risk level, and implement effective mitigation strategies. The table below illustrates five key strategies for mitigating high-risk events:
Strategy | Description | Benefits |
---|---|---|
1. Engineering Controls | Implementing physical modifications or barriers to eliminate or reduce hazards. | Decreases the likelihood of accidents and injuries. |
2. Administrative Controls | Implementing policies, procedures, and training to minimize risks. | Enhances employee awareness and reduces the occurrence of harm. |
3. Personal Protective Equipment (PPE) | Providing personal protective equipment to employees. | Protects individuals from potential hazards. |
4. Emergency Response Planning | Developing and implementing plans for responding to high-risk events. | Enables prompt and effective response to minimize damages. |
5. Regular Monitoring and Review | Continuously assessing and updating risk management strategies. | Ensures ongoing effectiveness and compliance with legal requirements. |
Organizations can effectively manage and mitigate high-risk events by employing these strategies, ensuring individuals’ safety and operations’ continuity.
Evaluation & Management of Residual Risk
Evaluating and managing residual risk in the context of ISO 12100 risk assessment involves a systematic approach to identifying and addressing any remaining risks after implementing protective measures.
The iso 12100 risk assessment template provides a framework for evaluating and managing residual risk to ensure the safety of machinery and equipment.
The evaluation process involves identifying potential hazards, estimating the severity and likelihood of accidents, and determining the adequacy of risk reduction measures.
Managing residual risk requires a thorough understanding of the steps in risk assessment, including hazard identification, risk estimation, and risk evaluation.
Following these steps, organizations can effectively evaluate and manage residual risk, ensuring that appropriate measures are in place to minimize the potential for accidents and injuries.
Legal Requirements & Regulatory Standards
Legal requirements and regulatory standards are critical in ensuring the safety and compliance of machinery and equipment. Compliance with these standards is essential to minimize the risks associated with the operation of machinery.
The ISO 12100 risk assessment template provides a systematic approach to identifying and evaluating hazards during a machine’s design and operation stages.
To comply with legal requirements and regulatory standards, organizations must consider the following:
- Risk reduction measures: Implementing measures to reduce risks to an acceptable level by applying engineering controls, administrative controls, and personal protective equipment.
- Safety management systems: Developing and implementing safety management systems to ensure the effective identification, assessment, and control of risks.
- Safety devices: Incorporating appropriate safety devices such as emergency stop buttons, guards, interlocks, and warning signs to protect operators and other personnel from potential hazards.
Following these legal requirements and regulatory standards, organizations can enhance safety and prevent accidents in the workplace.
Implementing an Effective Machine Safety Program
This program should follow the guidelines set forth by ISO 12100, which provides comprehensive guidance on risk assessment and risk reduction in machinery.
One of the key aspects of a successful program is the identification and mitigation of electrical hazards. By incorporating safe design measures, such as proper grounding and insulation, the risk of electrical failures can be minimized.
Additionally, considering power-related dangers throughout the machine’s life cycle is crucial.
An effective machine safety program should focus on continuous evaluation, training, and improvement to ensure a safe working environment.
Adherence to ISO 12100 and implementing appropriate safety measures, organizations can reduce the risks associated with machinery operations.
How to conduct iso 12100 risk assessment
One crucial step in conducting a risk assessment according to ISO 12100 is to thoroughly analyze the potential hazards associated with the machinery.
The risk assessor must conduct a basic risk assessment by identifying and evaluating the hazards present in the machine. This involves examining the machine’s design, operation, and maintenance processes to identify any potential risks.
After identifying the hazards, the risk assessor must determine the likelihood of occurrence and the severity of each hazard.
Once the hazards have been assessed, the risk assessor can proceed with the risk reduction process. This involves implementing adequate risk reduction measures to eliminate or minimize the identified hazards.
The risk assessor must adopt an iterative process, continuously reviewing and revising the risk assessment as necessary.
Detailed risk reduction measures should be documented and implemented according to the ISO 12100 guidelines to ensure machinery safety.
Frequently Asked Questions
Are any specific industries or sectors that must comply with the ISO 12100 risk assessment template?
Some industries or sectors that must comply with the ISO 12100 risk assessment template include manufacturing, construction, and machinery. This template provides a systematic approach to identifying and evaluating potential hazards to ensure safety measures are implemented.
What are the consequences of not conducting a risk assessment according to ISO 12100?
Not conducting a risk assessment according to ISO 12100 can have various consequences. These may include an increased likelihood of accidents, injuries, financial losses, and potential legal and regulatory non-compliance.
Are there any common challenges or pitfalls in estimating the probability and severity of occurrence?
Estimating the probability and severity of occurrence in risk assessment can be challenging due to subjective judgments, lack of data, and uncertainties. Common pitfalls include overestimating or underestimating risks, relying on intuition rather than evidence, and ignoring potential interactions between hazards.
What are the key elements to consider in evaluating and managing residual risk?
In evaluating and managing residual risk, key elements include identifying and documenting residual risks, determining their acceptability, implementing risk control measures, monitoring their effectiveness, and continuously reviewing and updating the risk assessment process.
Can ISO 12100 risk assessment be used for new and existing machines?
The ISO 12100 risk assessment can be used for new and existing machines. This standard provides a systematic approach to identifying and evaluating hazards, assessing risks, and implementing risk reduction measures in the design and use of machinery.
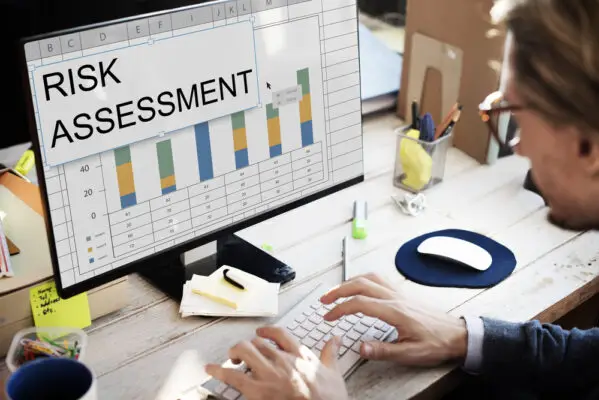
Conclusion
The ISO 12100 risk assessment template provides a structured approach to identifying and analyzing hazards to evaluate and manage risks. It guides organizations in meeting legal requirements and regulatory standards related to machine safety.
Organizations can prioritize and implement appropriate control measures by estimating the probability and severity of occurrence.
Evaluating and managing residual risk is crucial in ensuring a safe working environment.
Implementing an effective machine safety program based on ISO 12100 helps organizations reduce accidents and protect employees.
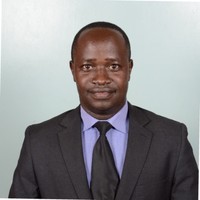
Chris Ekai is a Risk Management expert with over 10 years of experience in the field. He has a Master’s(MSc) degree in Risk Management from University of Portsmouth and is a CPA and Finance professional. He currently works as a Content Manager at Risk Publishing, writing about Enterprise Risk Management, Business Continuity Management and Project Management.