GMP (Good Manufacturing Practice) risk assessment is a crucial tool in the pharmaceutical industry for ensuring the safety, quality, and efficacy of drugs and healthcare products. It involves systematically identifying, evaluating, and controlling potential risks that may arise during the manufacturing process.
This article aims to provide an overview of GMP risk assessment by defining its scope and purpose, discussing different types of risk assessments, exploring its applications in the pharmaceutical industry, and highlighting the key components of a robust GMP risk assessment program.
GMP risk assessments are essential for compliance with regulatory requirements and international standards, such as those set by the Food and Drug Administration (FDA) and the World Health Organization (WHO). By proactively identifying and mitigating risks, pharmaceutical companies can prevent product recalls, adverse events, and non-compliance issues, safeguarding public health and maintaining the integrity of their operations.
Understanding the principles and methodologies of GMP risk assessment is crucial for pharmaceutical manufacturing, quality control, and regulatory affairs professionals.
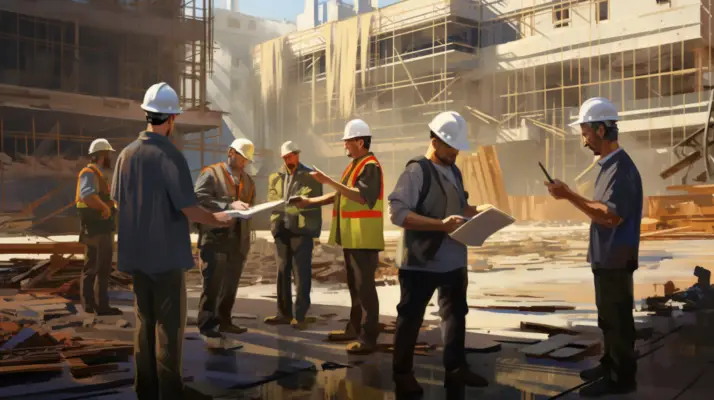
Definition of GMP Risk Assessment
The GMP risk assessment refers to the process of identifying and evaluating potential risks associated with Good Manufacturing Practices (GMP).
It involves a systematic approach to assess these risks‘ likelihood and severity and develop strategies to mitigate or control them.
The risk assessment process aims to ensure that GMP standards are implemented effectively and that products are manufactured safely and compliant.
Overview of the Risk Assessment Process
Examining the risk assessment process provides a comprehensive understanding of its various stages and procedures. Risk assessment is a crucial requirement in quality risk management, as it enables organizations to identify and evaluate potential risks that may impact their products’ safety, quality, and efficacy.
The process involves systematically identifying and analyzing risks and implementing controls to mitigate or eliminate them. Guidelines like those provided by regulatory agencies help ensure the risk assessment is standardized and consistent.
Risk analysis methods, such as failure mode and effects analysis (FMEA), hazard analysis, and critical control points (HACCP), can be employed.
Examples of risk assessment in the GMP context include assessing the risk of contamination in the supply chain or identifying potential hazards in manufacturing processes.
Risk assessment plays a crucial role in ensuring the safety and quality of products.
Types of Risk Assessments
This will focus on several types of risk assessments related to GMP, including:
- Qualitative risk assessment involves the subjective evaluation of risks based on expert opinions and past experiences.
- Quantitative risk assessment involves using numerical data and mathematical models to estimate the likelihood and impact of risks.
- Excipient risk evaluation: This aims to assess the potential risks of using excipients in drug manufacturing.
- Supply chain monitoring and control systems help ensure the quality and safety of raw materials and components used to produce medicines.
- Finished medicine quality assurance programs: These programs are established to verify the quality and safety of finished products before they are released to the market.
Qualitative Risk Assessment
Qualitative risk assessment analyzes potential risks without relying on subjective factors. It is an essential component of the quality risk management process in the pharmaceutical industry. This type of risk assessment evaluates risks based on their impact on patient safety and product quality.
It involves identifying and categorizing risk factors associated with manufacturing processes and control systems. By using a qualitative approach, the risk management process can prioritize risks and allocate appropriate resources to mitigate them effectively.
The table below illustrates the different risk levels and corresponding actions that can be taken to manage them:
Risk Level | Description | Action |
---|---|---|
High | Risks with a significant impact on patient safety | Implement immediate corrective actions |
Moderate | Risks with a moderate impact on patient safety | Develop mitigation strategies |
Low | Risks with a low impact on patient safety | Monitor and review regularly |
Conducting qualitative risk assessments, the pharmaceutical industry can proactively identify and address potential risks, ensuring the safety and quality of their products.
Quantitative Risk Assessment
Quantitative risk assessment provides a data-driven approach to evaluating and managing potential risks in the pharmaceutical industry, ensuring a comprehensive understanding of the magnitude and probability of adverse events. This method involves using numerical data to quantify risks, allowing for more precise decision-making in the industry.
In the context of the pharmaceutical industry, quantitative risk assessment involves several key steps:
- Identification of parameters: The first step is identifying the parameters relevant to the risk assessment process. This may include manufacturing processes, equipment, suppliers, and the supply chain.
- Collection of data: Quantitative risk assessment relies on reliable and accurate data. Therefore, data related to the identified parameters are collected from various sources, such as historical records, scientific literature, and expert opinions.
- Analysis and validation: The collected data are then analyzed using statistical methods to determine the probability and impact of potential risks. This analysis provides a quantitative understanding of the risks and helps prioritize them for effective risk management.
The pharmaceutical industry can make informed decisions regarding risk management, regulatory compliance, and approval processes by incorporating quantitative risk assessment alongside qualitative risk-ranking methods.
This data-driven approach enhances the industry’s ability to identify and mitigate risks, ultimately ensuring the safety and efficacy of pharmaceutical products.
Excipient Risk Evaluation
Excipient risk evaluation plays a crucial role in ensuring the safety and efficacy of pharmaceutical products. It involves thoroughly assessing the potential hazards associated with the inactive ingredients used in drug formulations.
The manufacturing process of pharmaceutical products involves the use of various excipients. These substances are added to the active pharmaceutical ingredient to facilitate the production and administration of the medicine.
While these excipients are inactive, they can still impact product quality and the overall safety profile of finished medicines. Therefore, conducting a comprehensive evaluation of excipient risks is essential to ensure pharmaceutical quality.
This risk management process involves using quantitative methods and risk assessment techniques. These techniques help identify, evaluate, and mitigate any potential risks associated with using excipients in drug formulations.
Manufacturers can make informed decisions regarding selecting and using excipients by employing a systematic risk evaluation method.This ultimately safeguards the overall quality and safety of medicines.
Supply Chain Monitoring and Control Systems
Supply chain monitoring and control systems play a crucial role in ensuring the integrity and reliability of pharmaceutical products. These systems effectively track and manage the flow of materials, information, and products throughout the supply chain network.
These systems utilize various risk indexes and the risk index method to evaluate and mitigate potential risks associated with the drug supply chain. Quality risk assessment techniques are applied to assess the risks associated with excipients, substances other than the active pharmaceutical ingredient in a drug product.
Control measures are then implemented to minimize these risks and ensure the assurance of supply chain integrity. Key factors addressed by these systems include supplier qualification, transportation conditions, and storage practices.
Pharmaceutical companies can use sophisticated monitoring and control systems to enhance their products’ safety and reliability. This ultimately benefits patients and the overall healthcare system.
Finished Medicine Quality Assurance Programs
Finished medicine quality assurance programs are essential for ensuring the integrity and reliability of pharmaceutical products by implementing effective measures to evaluate and control the various factors that impact the quality of finished medicines throughout the supply chain network.
One crucial aspect of these programs is the implementation of Good Manufacturing Practices (GMP) risk assessment. GMP risk assessment involves systematically identifying, evaluating, and controlling potential risks associated with manufacturing and distributing finished medicines.
This process helps mitigate risks from contamination, inadequate labelling, improper storage conditions, or substandard manufacturing practices. By conducting GMP risk assessments, pharmaceutical companies can proactively identify and address potential quality issues, ensuring that only safe and efficacious medicines reach the market.
These programs also play a vital role in meeting regulatory requirements and maintaining consumer trust in the pharmaceutical industry.
Pharmaceutical Industry Applications of GMP Risk Assessments
The pharmaceutical industry relies on GMP risk assessments to ensure the quality and safety of its products.
One key application of GMP risk assessments is evaluating manufacturing processes and their impact on product quality. Manufacturers can ensure consistent and high-quality production by identifying potential risks and implementing control measures.
Additionally, control systems are crucial in controlling manufacturing processes and minimizing the risk of deviations that could compromise product quality.
Regular examination of batch records is also essential in identifying and addressing any quality issues that may arise during manufacturing.
Manufacturing Processes and Product Quality
Manufacturing processes and product quality are crucial aspects that require thorough assessment in the context of GMP risk assessment. GMP risk assessments focus on identifying potential risks and implementing control measures to ensure the quality and safety of pharmaceutical products.
In manufacturing processes, GMP risk assessments involve evaluating the critical processing parameters and identifying critical control points. This assessment helps determine the appropriate control technologies and proposals to mitigate risks and maintain product quality.
Additionally, GMP risk assessments include the assessment of excipient function, which evaluates the functionality and suitability of the non-active ingredients in the formulation.
Furthermore, validation programs are integral to GMP risk assessments as they ensure that the manufacturing processes and control measures effectively maintain product quality and comply with regulatory standards.
Controlling Manufacturing Processes with Control Systems
Control systems are pivotal in ensuring manufacturing processes’ efficiency, accuracy, and reliability, instilling confidence in the audience by promoting consistency and quality throughout the production line. By implementing control systems, manufacturers can effectively control hazards and mitigate potential risks, ensuring that products meet the required quality standards.
Control point systems are commonly used in GMP risk assessments to identify critical points in the manufacturing process where control measures are necessary. These systems help identify and evaluate potential risks associated with each manufacturing step, allowing manufacturers to implement appropriate control measures to minimize the likelihood of product defects or deviations.
Common risk assessment methods, such as Failure Mode and Effects Analysis (FMEA) and Hazard Analysis and Critical Control Points (HACCP), assess the various components of excipient risk, ensuring that manufacturing processes are properly controlled and meet the required quality standards.
Components of Excipient Risk | Control Measures |
---|---|
Raw Material Quality | Supplier audits, material testing |
Manufacturing Process | Process validation, equipment calibration |
Packaging and Labeling | Inspection, label verification |
Storage and Distribution | Temperature control, proper handling |
Examination of Overwhelming Majority of Batch Records for Quality Issues
An extensive review of the overwhelming majority of batch records reveals a meticulous examination for any potential quality issues, allowing for a comprehensive evaluation of the manufacturing process and ensuring adherence to rigorous quality standards.
This examination is crucial for the classification of risks and the discussion of risk management strategies. Manufacturers can identify any deviations or potential problems during production by thoroughly documenting process risks and conducting an earlier risk assessment. This helps in meeting compliance requirements and ensuring the assurance of supply chain integrity.
To ensure consistency and efficacy, examining batch records also focuses on critical parameters, such as the finished medicine composition. By incorporating controls in batch record examination, manufacturers can maintain high-quality standards and minimize the risk of defects or errors in the final product.
Key Components of a GMP Risk Assessment Program
The key components of a GMP Risk Assessment program include:
- Identification and evaluation of potential risks and hazards.
- Conducting a comprehensive analysis of the manufacturing process.
- Identifying areas where risks may arise.
- Evaluating the potential impact of these risks on product quality and patient safety.
Establishing an effective system to monitor risks and hazards is crucial in ensuring ongoing compliance with GMP regulations. This includes:
- Implementing regular inspections, audits, and testing procedures.
- Identifying any emerging risks or hazards.
- Taking appropriate corrective actions to mitigate them.
Identification and Evaluation of Potential Risks and Hazards
Identifying and evaluating potential risks and hazards in the context of GMP involves systematically analyzing and assessing various factors that could threaten the quality, safety, and efficacy of pharmaceutical products. This crucial aspect of risk assessment requires a comprehensive understanding of the approaches and terms used in the field.
To make the process more manageable, an unordered bullet list can be utilized, including the following:
- Approximation of risk: Determining the likelihood and severity of potential risks.
- Clarity on risk: Ensuring a clear understanding of the identified risks.
- Detectability of risks: Assessing the ability to detect and mitigate risks effectively.
- CGMP requirements: Complying with the current Good Manufacturing Practice regulations.
Furthermore, evaluating potential risks and hazards in GMP must encompass the assurance of supply chain integrity, as the overwhelming majority of pharmaceutical products involve a complex drug supply chain.
Following these principles and considering various factors, identifying and evaluating potential risks and hazards in GMP can help safeguard the quality and safety of pharmaceutical products.
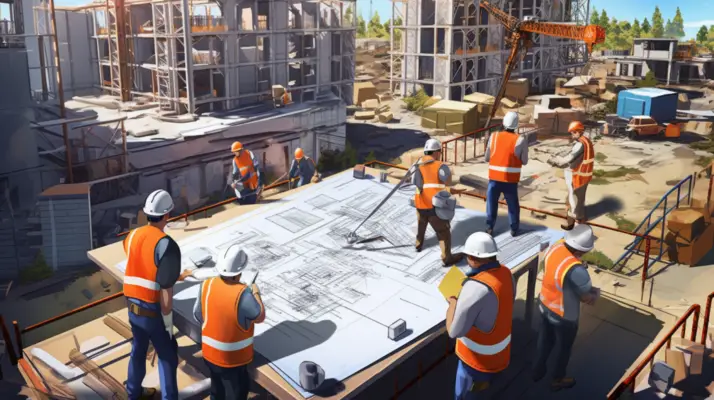
Establishing an Effective System to Monitor Risks and Hazards
This is a crucial step in ensuring the safety and quality of products in various industries, including the aerospace, biopharma, and chemical industries.
A 3-column and 5-row table is included below to understand this topic comprehensively. This table highlights the key considerations and parameters that must be monitored in different drug distribution or supply chain stages.
It also emphasizes incorporating specific component parameters during the risk assessment. This approach to regulation aligns with the eugmp requirements and provides valuable guidance for industry professionals involved in drug approval activities.
Stage of Drug Distribution Chain | Key Considerations | Parameters to Monitor |
---|---|---|
Manufacturing | Contamination | Quality control tests |
Packaging and Labeling | Mislabeling | Correct labeling |
Storage and Transportation | Temperature | Cold chain management |
Wholesale and Retail | Counterfeiting | Track and trace system |
Patient Use | Adverse reactions | Post-marketing surveillance |
Frequently Asked Questions
What are the benefits of conducting a GMP risk assessment in the pharmaceutical industry?
Conducting a GMP risk assessment in the pharmaceutical industry provides numerous benefits. It ensures compliance with regulatory requirements, identifies potential hazards, mitigates risks, enhances product quality, promotes patient safety, and fosters continuous improvement in manufacturing processes.
How often should a GMP risk assessment be conducted in a pharmaceutical manufacturing facility?
A gmp risk assessment should be conducted periodically in a pharmaceutical manufacturing facility to ensure compliance with Good Manufacturing Practices. The frequency of the assessment may vary depending on the specific requirements and risks associated with the facility.
What are the common challenges faced when implementing a GMP risk assessment program?
Common challenges in implementing a GMP risk assessment program include lack of awareness among staff, resistance to change, difficulty in identifying and prioritizing risks, limited resources for conducting assessments and ensuring consistent follow-up and corrective actions.
Are there any regulatory requirements or guidelines that govern GMP risk assessments in the pharmaceutical industry?
Regulatory requirements and guidelines, such as those from the International Council for Harmonisation of Technical Requirements for Pharmaceuticals for Human Use (ICH), govern risk assessments in the pharmaceutical industry to ensure compliance with Good Manufacturing Practices (GMP) standards.
Can you provide examples of real-life scenarios where a GMP risk assessment has helped identify and mitigate potential risks in pharmaceutical manufacturing processes?
Real-life scenarios in the pharmaceutical industry have demonstrated the effectiveness of GMP risk assessments in identifying and mitigating potential risks in manufacturing processes. For example, a risk assessment identified contamination risks in a production line, leading to the implementation of preventive measures and quality improvements.
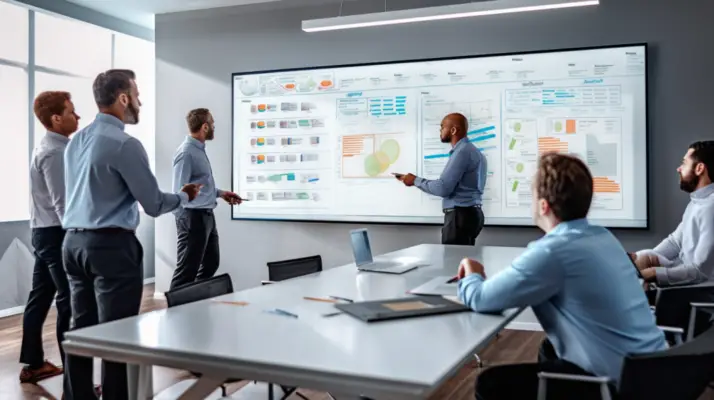
Conclusion
GMP risk assessment is a crucial tool in the pharmaceutical industry to ensure the safety and quality of products. By identifying potential risks and implementing appropriate measures, companies can mitigate the likelihood of adverse events and non-compliance with regulations.
Different types of risk assessments, such as hazard analysis and critical control points (HACCP) and failure mode and effects analysis (FMEA), are utilized to address various aspects of the manufacturing process.
A comprehensive GMP risk assessment program should include the following:
- Clear objectives.
- Robust methodologies.
- Regular reviews to maintain effectiveness.
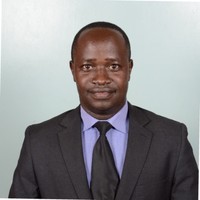
Chris Ekai is a Risk Management expert with over 10 years of experience in the field. He has a Master’s(MSc) degree in Risk Management from University of Portsmouth and is a CPA and Finance professional. He currently works as a Content Manager at Risk Publishing, writing about Enterprise Risk Management, Business Continuity Management and Project Management.