This article and review provides an in-depth review and analysis of joinery risk assessment practice, focusing on identifying and evaluating potential hazards in the industry. Risk assessment is a crucial component of occupational health and safety management, as it enables organizations to identify and mitigate potential risks to workers’ health and safety.
According to the U.S. Bureau of Labor Statistics, the joinery sector accounted for 1.2 million jobs in 2020, most of which are in the US. Organizations must undertake a thorough risk assessment process to ensure the safety and well-being of joinery workers in these countries.
This article begins by defining risk assessment and its importance in the joinery sector. It then presents an overview of the company details, emphasizing the significance of a detailed understanding of the organization’s operations, machinery, and processes in the risk assessment process
Furthermore, the article examines the hazards associated with woodworking machinery, such as wood dust and loud noises, and their potential impact on workers’ well-being. Additionally, it explores other health hazards related to joinery work, providing a thorough and analytical examination of the risks involved
This article aims to provide a comprehensive understanding of joinery risk assessment, enabling organizations to develop effective strategies for safeguarding workers’ health and safety
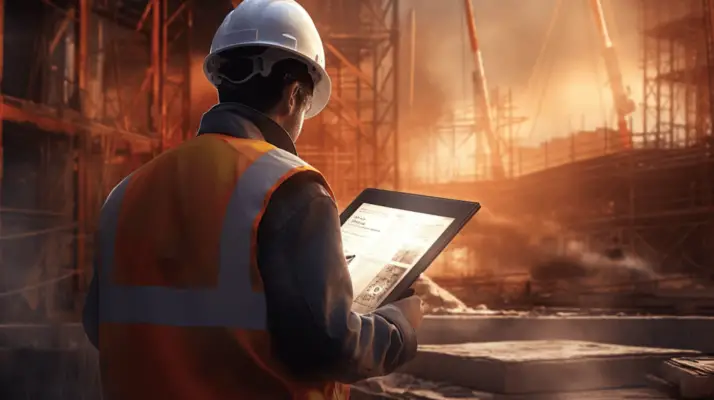
Concrete Pouring Risk Assessment
Definition of Risk Assessment
Joinery risk assessment is the process of identifying, evaluating, and controlling risks associated with joinery work.
The purpose of joinery risk assessment is to ensure the health and safety of workers and prevent accidents or injuries.
Types of risks in joinery may include hazards related to using tools and machinery, working at heights, handling heavy materials, and exposure to harmful substances.
Principles for managing health and safety risks in joinery involve implementing appropriate control measures, providing training and supervision to workers, regularly reviewing and updating risk assessments, and promoting a culture of safety within the workplace.
Purpose of Joinery Risk Assessment
The purpose of conducting a joinery risk assessment is to:
- Identify potential hazards and evaluate associated risks.
- Ensure the safety and well-being of workers.
- Minimize the likelihood of accidents or injuries during joinery operations.
This assessment is crucial in the joinery industry because:
- Employees are exposed to various tools, materials, and conditions that can pose significant risks
By conducting a thorough risk assessment, companies can:
- Identify specific hazards such as improper use of machinery, exposure to harmful substances, or inadequate safety measures
- Implement appropriate control measures
- Develop effective safety policies and procedures
The ultimate goal of a joinery risk assessment is to:
- Create a safe working environment for employees
- Minimize or eliminate unnecessary danger or harm during tasks.
Types of Risks in Joinery
Various hazards can arise in the joinery field, including potential dangers associated with the operation of machinery, exposure to harmful substances, or inadequate safety measures. Joinery work involves using various equipment and tools, such as saws, drills, and sanders, which can pose risks if not operated properly.
Additionally, using wood and other materials in joinery can generate dust and particles that may lead to respiratory and other issues, if inhaled. Joinery companies should prioritize employee training and ensure safety measures are in place to mitigate these risks
This includes providing employees covering proper personal protective equipment, implementing dust extraction systems, and conducting regular risk assessments. By addressing these and other issues and hazards, woodworking companies can create a safer work environment and reduce the likelihood of accidents or injuries.
Type of RiskDescriptionExampleMachinery-related risksDangers associated with operating machineryAccidental amputation from a table sawChemical hazardsExposure to harmful substancesContact with toxic wood preservativesInadequate safety measuresLack of proper safety protocolsAbsence of machine guards or safety switchesRespiratory risksInhalation of dust and particlesDevelopment of respiratory illnessesPhysical injuriesAccidents resulting in physical harmFalling objects causing head injuries
Type of risk
Principles for Managing Health and Safety Risks in Joinery
One crucial aspect to consider in the joinery field is the implementation of effective principles for managing health and other safety issues and risks.
Regular carpentry risk assessments should be conducted to identify potential hazards to ensure a safe working environment.
The control of health risks, such as eye injury, can be achieved through protective equipment such as safety goggles.
Risks from wood dust can be mitigated by wearing dust masks and implementing proper ventilation systems or extraction equipment.
Supervision for machinery is essential to minimize the risk of accidents.
Additionally, maintaining health surveillance records and providing appropriate training on handling hazardous substances are vital to prevent health hazards in joinery.
Adherence to these principles, joinery workshops can create a safe and healthy working environment for their employees.
Company Details
This discussion will focus on the obligations of employers and the responsibilities of employees in relation to risk assessment in the joinery industry.
Employers have a legal duty to ensure the health and safety of their employees, including conducting risk assessments to identify and address potential hazards. This involves implementing control measures and providing appropriate training and information.
On the other hand, employees are responsible for following the safety procedures put in place by their employers, taking reasonable care of their own health and safety, and reporting any concerns or incidents.
Obligations of Employers
Employers in the joinery industry have a legal obligation to ensure the safety and health of their employees by implementing appropriate risk assessment measures. This involves identifying potential hazards and evaluating the risk associated with each task.
A thorough assessment should consider various factors, such as loud noises from woodworking machinery or the installation of heavy machinery. To create a clear image, the following table provides an example of the types of hazards that may be encountered in joinery work and the corresponding preventive measures that should be taken:
HazardsPreventive MeasuresLoud noisesProvide hearing protection to workers operating noisy machinery.InstallationEnsure proper training and supervision for workers involved in equipment installation.Machine operationImplement correct safeguards and safety features on all machinery.Emergency proceduresDevelop and communicate clear emergency procedures to all employees.Method statementsPrepare detailed method statements for each task to guide workers and minimize risks.
Hazard
Following these guidelines, employers can fulfil their obligations to protect their workers and create a safe working environment.
Responsibilities of Employees
It is essential to understand the responsibilities of employees in ensuring a safe working environment. As mentioned, employers are primarily obligated to provide a safe workplace; however, employees also play a crucial role in maintaining health and safety standards.
Employees should familiarize themselves with carpentry risk assessment and be aware of common hazards in the joinery industry. They should adhere to health and safety legislation and actively participate in loss prevention activities.
Employees need to follow written instructions provided by employers regarding safe practices and the use of powered hand tools. Additionally, employees should undergo high-level health surveillance, which may be required in their field of activity.
Fulfilling these responsibilities, employees can contribute significantly to the overall safety and well-being of the workplace.
- Familiarize yourself with carpentry risk assessment.
- Identify common hazards in the joinery industry.
- Adhere to health and safety legislation.
- Participate in loss prevention activities.
- Follow instructions regarding powered hand tools.
- Undergo high-level health surveillance.
- Ensure a safe working environment.
- Contribute to the overall safety of the workplace.
- Promote well-being in the joinery industry.
Woodworking Machinery
It is crucial to have the correct safeguards in place to ensure the safety of workers and the machinery information prevent accidents. This includes installing safety features such as guards, emergency stop buttons, and safety interlocks on the machinery. Regular maintenance and inspections of extraction equipment should also be conducted to identify any potential hazards or malfunctions.
In addition, establishing proper emergency procedures is necessary to respond effectively to any unforeseen incidents. This includes training workers to respond to emergencies, further actions such as shutting down machinery information or off the machinery and evacuating employees covering the area safely. Clear communication channels should be established to alert everyone in the vicinity of any emergency situation quickly.
Furthermore, supervision is essential to ensure workers use the machinery correctly and properly and follow all safety protocols. Supervisors should be trained in the operation of the woodworking machinery and be knowledgeable about the safety guidelines. They should regularly monitor workers to ensure they safely and properly use the machinery and provide guidance or corrective action when necessary.
Implementing these measures, companies can create a safer working environment when using woodworking machinery. This protects workers’ well-being and reduces the risk of accidents and potential legal liabilities.
Correct Safeguards and Emergency Procedures
To ensure a safe working environment, it is crucial to implement appropriate safeguards and emergency procedures in joinery. Safety documents such as risk assessment forms are vital in identifying potential risks and outlining the necessary precautions.
Carpentry risk assessments should be conducted regularly to identify common risks associated with joinery work, such as falls, tool hazards, and exposure to harmful substances.
Occupational risks, such as repetitive strain injuries and back problems, should also be considered. Protective equipment, such as gloves, safety goggles, and dust masks, should be provided to workers to minimize the risk of injury or illness. The dust resistance coefficient of such equipment should be evaluated to ensure its effectiveness.
Additionally, compliance with health safety legislation and adherence to health and safety protocols are essential in maintaining a safe working environment.
Supervision for Machinery Use
Supervision is essential for ensuring machinery’s safe and proper use in the joinery field. The carpentry risk assessment method statement and the program should include specific guidelines for supervising machinery use.
This includes identifying and addressing hazards associated with wood dust, such as the control of wood dust through good control, proper ventilation and personal protective equipment.
Supervision should also focus on installing architrave and balustrades, as these tasks require carefully handling materials and using high-risk handfed woodworking machines.
The woodworking industry is known for its noise from machinery, so supervision should ensure that workers are aware of and use appropriate hearing protection.
Effective supervision of machinery is crucial for maintaining a safe working environment in the joinery field.
Hazards from Wood Dust and Loud Noises
Health surveillance records play a crucial role in monitoring and assessing the health of workers exposed to wood dust and loud noises, allowing for early detection of any adverse health effects.
Appropriate protective equipment, such as respiratory masks and earplugs, is necessary to minimize the risk of respiratory and hearing problems associated with wood dust and noise exposure.
Additionally, noise control measures, such as soundproofing enclosures and proper machinery maintenance, can reduce noise levels and protect workers from noise-induced hearing loss.
Health Surveillance Records
Health surveillance records provide valuable information about the workers’ overall well-being and help identify potential risks and hazards in the joinery industry, creating a sense of urgency to prioritize implementing preventive measures.
These records encompass a wide range of data, including the task risk assessment form, generic risk assessment, and key risks. Analyzing these records, employers can identify persons at risk and develop specific strategies to mitigate those risks
Incorporating prewritten risk assessments and proactive risk management approaches, such as safety courses and premade health and safety management forms, can further enhance carpentry health and safety.
Additionally, maintaining a comprehensive library of hazards and regularly updating risk assessment documents can ensure that workers are aware of the potential dangers onsite. This includes dangerous equipment, such as high-risk hand-fed woodworking machines.
Furthermore, high-level health surveillance can monitor workers’ well-being and identify any potential health and safety issues related to their work in joinery.
Protective Equipment for Wood Dust and Noise Control
Previous studies have highlighted the importance of maintaining accurate health surveillance records within the joinery industry to manage and mitigate risks effectively. Building on this, the current subtopic focuses on using protective equipment for woodworking company dust and noise control as a crucial aspect of comprehensive carpentry risk assessment.
Wood dust poses significant cancer risks, making implementing appropriate measures to protect workers imperative. Risk assessment software can aid in identifying and evaluating the conditions for wood dust exposure and formulating effective control strategies.
Additionally, using protective equipment, such as respiratory masks and hearing protection, is essential to minimize the harmful effects of dust inhalation and injury from dust particles.
Health and Safety Executive (HSE) documents provide guidelines and joinery-specific health and safety documents that address a range of hazards, including equipment loudness, ensuring the overall health safety of joinery workers.
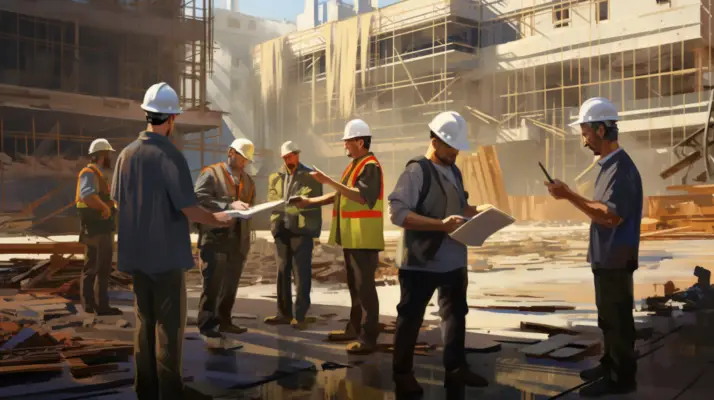
Definition Of Baseline Risk Assessment
Joinery workers are exposed to various carcinogens, such as formaldehyde, wood dust, and solvent-based paints. These substances can increase lung, nasal, and throat cancer risk.
It is important for joinery workers to take proper precautions, further actions such as wearing personal protective equipment and implementing effective ventilation systems, to minimize their exposure to these hazardous substances.
Cancer Risks
Cancer risks associated with joinery work are a pressing concern that warrants attention and preventive measures. Joinery work commonly involves the manipulation of wood, which generates hardwood dust that poses health risks when inhaled.
The indoor dust environment in joinery workshops can expose workers to high levels of this hazardous dust. To mitigate these risks, joinery workshops should implement premade health and safety management forms to ensure proper risk assessment and control measures.
Additionally, professional equipment such as dedusting and industrial filtering installations can effectively remove harmful particles from the air. It is crucial to consider particle sizes, as smaller particles, such as plant fiber particles, can penetrate deep into the lungs and increase the risk of cancer.
Furthermore, high-risk handfed woodworking machines should be cautiously operated to minimize exposure to certain carcinogens. Understanding and addressing the cancer risks associated with joinery work is vital for protecting workers’ health and safety.
Frequently Asked Questions
What are the legal requirements for conducting a joinery risk assessment?
The legal requirements for conducting a risk assessment in joinery include identifying hazards, evaluating risks, implementing control measures, and regularly reviewing and updating the assessment to ensure compliance with health and safety regulations.
How often should a joinery risk assessment be reviewed and updated?
A joinery risk assessment should be reviewed and updated periodically to ensure the continued effectiveness of risk control measures. The frequency of review depends on factors such as changes in work processes, equipment, and legislation.
Are there any specific safety measures that need to be implemented when using woodworking machinery in a joinery workshop?
Specific safety measures that should be implemented when using woodworking machinery in a joinery workshop include providing adequate training to employees, implementing proper machine guarding, ensuring the use of personal protective equipment, and regularly maintaining and inspecting the machinery to prevent accidents.
What are the potential long-term health effects of exposure to wood dust in joinery work?
Exposure to wood dust in joinery work can lead to various long-term health effects. These may include respiratory issues such as asthma, chronic bronchitis, and nasal cancer. Implementing proper ventilation and personal protective equipment to mitigate these risks is important.
Are any training or certification programs available for joinery workers to enhance their knowledge and skills in risk assessment?
Training and certification programs are available for joinery workers to enhance their knowledge and skills in risk assessment. These programs offer comprehensive training on identifying hazards, evaluating risks, implementing control measures, and ensuring compliance with regulatory standards.
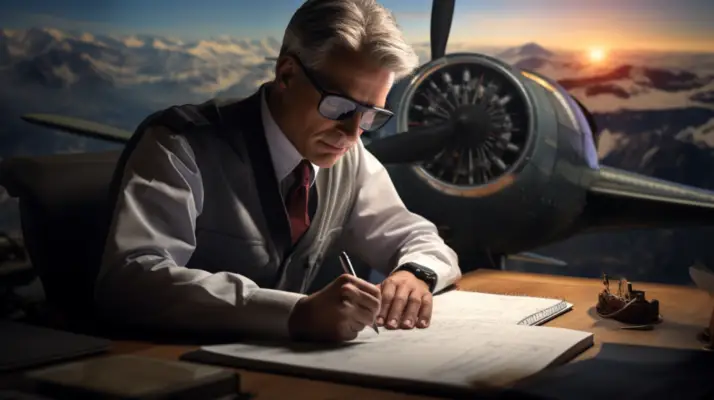
Definition Of Risk Assessment In Aviation
Risk assessment in the joinery industry is crucial to identify and mitigate potential hazards.
By assessing the risks associated with woodworking machinery, such as the risk of injury or accidents, and implementing proper safety measures, joinery companies can ensure the well-being of their employees.
Additionally, addressing health hazards like wood dust and loud noises through proper ventilation and hearing protection can prevent long-term health issues.
A comprehensive risk assessment is essential for maintaining a safe and healthy working environment in the joinery industry.
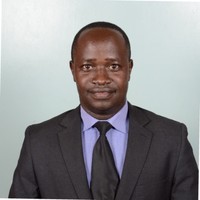
Chris Ekai is a Risk Management expert with over 10 years of experience in the field. He has a Master’s(MSc) degree in Risk Management from University of Portsmouth and is a CPA and Finance professional. He currently works as a Content Manager at Risk Publishing, writing about Enterprise Risk Management, Business Continuity Management and Project Management.