Task Based Risk Assessment is a systematic process to identify and evaluate potential risks associated with specific tasks in various settings.
It involves a comprehensive analysis of the tasks performed, their potential hazards, and the likelihood of occurrence. This approach aims to establish a hierarchy of controls to mitigate and manage identified risks effectively.
This article aims to thoroughly understand the task-based risk assessment process and its significance in ensuring safety and efficiency in various industries.
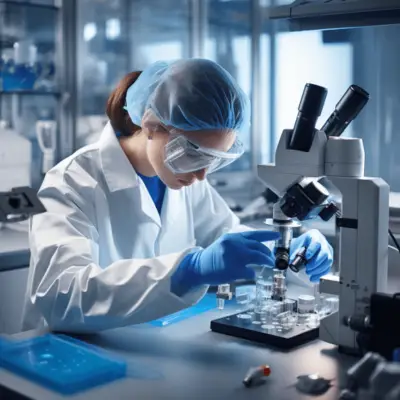
What is Task Based Risk Assessment?
Task-based risk assessment is crucial in ensuring the safety and well-being of individuals involved in various tasks. It involves identifying and evaluating potential risks and hazards associated with specific tasks, allowing for a comprehensive understanding of their potential dangers.
This type of risk assessment is important because it enables organizations to implement appropriate control measures, minimize accidents and injuries, and create a safer working environment for employees.
Why is Task-Based Risk Assessment Important?
Essential for ensuring workplace safety, a thorough risk assessment that focuses on tasks provides an objective evaluation of potential hazards.
Task-based risk assessment is important for several reasons:
- Identification of hazards: By analyzing tasks, potential safety and operational risks can be identified, allowing employers to understand the hazards associated with each task.
- Control measures: Task-based risk assessment enables the development of appropriate control measures to mitigate identified hazards. This ensures that workers and employees are protected from potential harm.
- Risk minimization: Through task-based risk analysis, employers can prioritize and allocate resources to minimize risks associated with specific tasks, ultimately reducing the likelihood of accidents and injuries.
Knowing the Potential Risks
This discussion will focus on the importance of hazard identification and potential hazards in the workplace.
It will also explore the safety standards and requirements that employers must adhere to to ensure the well-being of their employees.
Additionally, the discussion will address the issue of hazardous substances and the potential risks associated with their use.
Furthermore, it will discuss the growing concern about mobile device use in the workplace and its impact on safety.
Hazard Identification
One of the fundamental steps in risk assessment is identifying hazards. Hazard identification involves the systematic process of recognizing potential sources of harm in a given situation.
This process is crucial as it allows organizations to understand the risks associated with their operations and develop appropriate control measures. A team of experts should be assembled to effectively identify hazards, including employees familiar with the specific tasks and equipment involved.
Various methods can be used, such as reviewing relevant documents and standards, conducting on-site inspections, and engaging in employee discussions.
Hazards can be accurately identified and documented by considering the specific operation and equipment in use.
This information then serves as a foundation for implementing control measures to mitigate the identified risks and ensure the safety of employees and the overall workplace.
Qualitative risk analysis plays an essential role in the modern business environment, particularly when dealing with automation in manufacturing. Engineers can ensure risk is minimised by identifying and understanding the risk assessment tasks, especially in dangerous manufacturing tasks.
Common risk assessment examples often include compliance risk analyses, utilizing common risk assessment tools such as a compliant risk assessment spreadsheet. The details of risk assessments vary, but the end goal is always to develop effective risk strategies that protect both engineers at risk and the broader workplace.
A company can build a safety-conscious culture with the right training and control measures.
Effective risk assessment training underscores Control Reliability’s importance in handling internal and external events risks. The decision on preventative control measures, safety controls, and 25kg Control Measures – Comply should be based on in-depth analysis.
Control Measures like Area, Clear area, Full, MEWP, and Trained must align with the specific requirements of a situation. Control systems must be dynamic and adaptable, translating into effective controls that mitigate time-related hazards and increase awareness of hazards, even in complex hazard sites.
The involvement of workers in risk assessments is paramount, especially considering their experience and exposure to hazards. From the experienced worker to those new to the job, exposure of utility workers and other employees to risks must be managed and minimized.
Feedback on workers’ experiences and ergonomic solutions can create a market-leading solution that enhances employee morale. Collaborative operations that tap into workers’ collective experience lead to more cost-efficient and innovative solutions.
In daily operations, including Dermal Exposure Operations, adherence to standards like ANSI/RIA R15.06-2012 is vital. Complex situations like dermal exposure or emergencies involving critical equipment like display screen equipment may arise.
These situations require a core method like the DTB-HAZID method to implement control actions. The participation of people from the team of individuals, such as the assessment team, ensures a well-rounded understanding of occupational health risks and potential damage to health.
Keeping an eye on the bigger picture, it’s crucial to regularly conduct reviews such as the 11042250 Review and 23860542 Review.
Learning from accident history, including excavation-related accidents, and having ready access to documents and document supplements helps prevent severe or even Negligible Injuries.
This comprehensive approach also involves sharing deep knowledge with the company through ongoing customer dialogue. It’s a dynamic process considering design and ecological factors without succumbing to classical business limitations.
The use of industrial robots to enhance operations is a technological achievement and an embodiment of the comprehensive approach to safety and efficiency. From customisable hazard assessments to automation solutions that focus on the experience of workers, the entire landscape is evolving.
Embracing a comprehensive and collaborative approach to risk management, businesses can ensure that their operations are efficient but also safe, adaptable, and resilient.
The intersection of technology, worker engagement, and regulatory compliance creates a dynamic and exciting field full of opportunities and challenges.
Potential Hazards
Identifying potential hazards is critical in ensuring workplace safety, as it allows organizations to anticipate and mitigate risks that could harm employees or disrupt operations.
During the task risk assessment process, various potential hazards are assessed to determine the level of risk associated with each task. This assessment is typically conducted through qualitative and quantitative risk analysis methods.
Organizations often use a module-based approach to effectively assess potential hazards, breaking down tasks into smaller components for analysis.
This allows for a more detailed examination of each task and its associated risks. Risk questions guide the analysis, considering the likelihood and severity of potential hazards.
The level of task risk is then determined based on the analysis, taking into account the potential consequences and likelihood of occurrence.
Through this process, organizations can identify the risk associated with each task and develop appropriate control measures to mitigate risks. The residual risk figure is also calculated to assess the effectiveness of control measures in reducing risks.
Safety Standards and Requirements
Safety standards and requirements play a crucial role in ensuring workplace safety by establishing guidelines and regulations that organizations must adhere to to prevent potential hazards and protect employees.
Task-based risk assessment is a vital component of the risk assessment process, as it helps identify potential risks associated with specific tasks or activities. This process involves conducting a thorough task analysis, identifying potential hazards, and implementing appropriate control measures to mitigate the risks.
Safety controls are implemented to ensure compliance with safety standards and requirements, reducing the likelihood of accidents or injuries. A comprehensive control program should be implemented, which includes regular inspections, training programs, and ongoing evaluation of safety procedures.
Hazardous Substances
Properly handling and managing hazardous substances is essential in minimizing potential risks and ensuring the safety of the workplace and employees.
A systematic process known as task-based risk assessment is employed to achieve this. This process involves the identification of potential hazards associated with the use and handling of hazardous substances, followed by the implementation of appropriate control measures.
Risk assessment techniques, such as the task risk assessment module, are utilized to evaluate the level of risk and determine the necessary controls.
These controls can be categorized into engineering controls, which involve modifying the physical environment to eliminate or reduce the risk, and administrative controls, which involve implementing policies and procedures to manage the risk.
It is important to follow the control hierarchy, prioritising engineering controls over administrative controls. Adhering to safety requirements and implementing these control measures can effectively minimise the potential for injury and harm related to hazardous substances.
Mobile Device Use in the Workplace
Mobile device use in the workplace has become increasingly prevalent in recent years, posing potential risks to productivity and workplace safety. Risk assessment is essential in identifying and evaluating the hazards associated with mobile device use.
Mobile device use can affect employees’ health and well-being, as prolonged use can lead to musculoskeletal disorders, eye strain, and mental health issues. Accidents can also occur due to distractions caused by mobile devices.
Control measures should be implemented to mitigate these risks, such as providing ergonomic workstations, promoting regular breaks, and enforcing policies on responsible mobile device use. Legal requirements related to mobile device use should also be considered, especially in industries where safety regulations are stringent.
Overall, a comprehensive risk assessment is crucial in ensuring the safety and well-being of employees in the workplace.
Implementing a Systematic Process of Risk Assessment
The implementation of a systematic process of risk assessment requires the identification of a competent person who will be responsible for conducting the assessment. This person should have the knowledge and expertise to assess and evaluate potential risks accurately.
Additionally, legal requirements and regulations must be considered during the risk assessment to ensure compliance and adherence to relevant laws and guidelines.
Initial risk analysis measures involve gathering relevant information and data to identify and assess potential hazards and risks. Developing a risk matrix can aid in categorizing and prioritizing risks based on their severity and likelihood.
Establishing a risk rating system for tasks enables a systematic approach to assessing and managing risks, allowing for implementing effective risk mitigation strategies.
Competent Person Responsible for Risk Assessment
To ensure the accuracy and thoroughness of the risk assessment, it is imperative to appoint a competent person with the necessary expertise and knowledge in the field.
A competent person plays a crucial role in conducting a comprehensive risk assessment. They are responsible for analyzing potential risks, identifying existing control measures, and determining the effectiveness of these measures.
The competent person should have a deep understanding of risk analysis measures and be capable of utilizing tools such as the risk matrix to assess the likelihood and consequence of each identified risk. They should also consider the organization’s risk tolerance and evaluate the initial risk against acceptable levels.
The competent person may also use a risk assessment template to guide the process and ensure consistency. Advanced risk assessment techniques, such as task-based risk assessment, may also be employed to assess risks associated with specific organisational tasks or activities.
Legal Requirements and Regulations
Legal requirements and regulations play a critical role in ensuring that organizations comply with established standards and guidelines related to risk assessment. These requirements and regulations are designed to protect employees from workplace hazards and minimize the risk of accidents or injuries.
Regular risk assessments are an essential part of this process, as it allows organizations to identify and evaluate potential hazards, assess the risk associated with each hazard, and implement appropriate control measures to mitigate those risks.
To illustrate the importance of legal requirements and regulations in risk assessment, the following table provides an overview of common workplace hazards, their associated risk ratings, and control measures that organizations may implement to minimize employee exposure to these hazards:
Workplace Hazard | Risk Rating | Control Measures |
---|---|---|
Chemical Exposure | High | Personal protective equipment (PPE), ventilation systems, proper handling and storage procedures |
Ergonomic Hazards | Medium | Proper workstation design, regular breaks, ergonomic equipment |
Slip and Fall Hazards | Low | Non-slip flooring, clear walkways, regular maintenance and inspections |
Initial Risk Analysis Measures
Conducting an initial analysis of potential risks is crucial for organizations to identify and evaluate potential hazards and assess the associated risk level.
One approach to conducting this analysis is through task-based risk assessment. This method involves breaking down the tasks or activities within an organization and analyzing the potential risks associated with each task.
The initial risk analysis measures typically include identifying the hazards, assessing the likelihood and consequences of those hazards, and determining the level of risk.
This process helps organizations prioritize their risk management efforts and allocate resources effectively to minimize potential harm and maximize safety for employees and stakeholders.
Developing a Risk Matrix
Developing a risk matrix involves categorizing potential hazards and assessing their likelihood and consequences to prioritize and allocate resources effectively for risk management.
Task-based risk assessment plays a crucial role in this process. By breaking down operations into specific tasks, organizations can identify hazards that workers may encounter.
These hazards can range from physical risks, such as exposure to harmful substances or working in confined spaces, to ergonomic risks, such as repetitive movements or awkward postures.
Once hazards are identified, the next step is to assess their likelihood and consequences. This involves analyzing the probability of an incident occurring and the severity of its potential impact on workers and operations. Control measures can then be implemented to mitigate these risks.
Developing a risk matrix provides a structured approach to prioritize risks and allocate resources efficiently. A software solution can facilitate this process, allowing for collaborative input from employees and ensuring a comprehensive assessment of risks.
This approach is especially relevant in industries where collaborative robots are being introduced, as they require careful evaluation of potential hazards and control measures to ensure the safety of workers.

Establishing a Risk Rating System for Tasks
Establishing a risk rating system for tasks involves assigning a numerical value to the likelihood and consequences of potential hazards, enabling organizations to prioritize and allocate resources effectively for risk management.
A task-based risk assessment is crucial in identifying and evaluating risks associated with specific organisational tasks.
The risk rating system provides a structured approach to assess and prioritize risks by considering the probability and potential impact of each hazard.
Organizations can objectively compare and rank each risk by assigning a numerical value to each risk, allowing for informed decision-making and resource allocation.
This system helps organizations focus on addressing high-risk tasks first, reducing the likelihood and severity of incidents.
A well-established risk rating system also promotes consistency and transparency in risk management practices, facilitating effective communication and collaboration among stakeholders.
Establishing a Hierarchy of Controls
Implementing a hierarchy of controls is essential for effectively managing risk and reducing the likelihood of workplace hazards.
A task-based risk assessment is a systematic approach to identifying potential hazards and evaluating the associated risks within specific work tasks.
Organizations can prioritize and implement the most effective measures to eliminate or minimize these risks by establishing a hierarchy of controls.
The hierarchy typically includes five levels: elimination, substitution, engineering controls, administrative controls, and personal protective equipment.
Elimination involves removing the hazard altogether, while substitution seeks to replace it with a less hazardous alternative.
Engineering controls focus on isolating or enclosing the hazard, while administrative controls involve changing work practices and procedures.
Personal protective equipment is a last resort to protect workers from remaining risks.
Frequently Asked Questions
How Can I Effectively Communicate the Findings of a Task-Based Risk Assessment to My Team Members?
Effective communication of task-based risk assessment findings to team members involves clearly and concisely presenting the assessment results, using appropriate visual aids and easily understood language. It is important to address any potential concerns and provide actionable recommendations for risk mitigation.
What Common Examples of Tasks Would Require a Task-Based Risk Assessment?
Tasks requiring task-based risk assessment include working at heights, operating heavy machinery, handling hazardous materials, working with electrical equipment, and performing manual handling activities. These tasks involve potential risks that must be identified and managed to ensure safety.
Are There Any Legal Obligations or Regulations That Require Organizations to Conduct Task-Based Risk Assessments?
Organizations may have legal obligations or be subject to regulations that require them to conduct task-based risk assessments. These assessments help identify and mitigate potential risks associated with specific tasks, ensuring the safety and well-being of workers and compliance with legal requirements.
How Frequently Should Task-Based Risk Assessments Be Conducted Within an Organization?
The frequency at which task-based risk assessments should be conducted within an organization depends on various factors, including the nature and complexity of tasks, the level of risk involved, and any legal or regulatory requirements applicable to the organization.
What Are the Potential Consequences of Not Conducting a Task-Based Risk Assessment for an Organization?
The potential consequences of not conducting a task-based risk assessment for an organization include an increased likelihood of accidents, injuries, and financial losses.
The organization is exposed to potential harm and liabilities without identifying and mitigating risks.
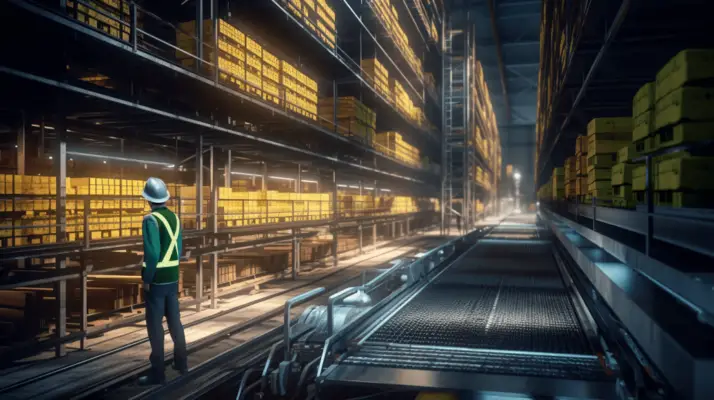
Conclusion
Task Based Risk Assessment is a systematic process used to identify and evaluate potential risks associated with specific tasks. Focusing on the tasks rather than the overall project or organization allows for a more detailed and accurate assessment of risks.
This article has discussed the importance of understanding potential risks and the steps involved in implementing a systematic risk assessment process.
Additionally, it emphasized the need to establish a hierarchy of controls to mitigate and manage these risks effectively.
Task Based Risk Assessment is a valuable tool in ensuring the safety and success of any project or task.
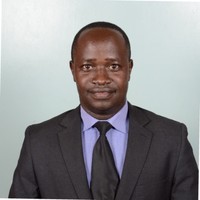
Chris Ekai is a Risk Management expert with over 10 years of experience in the field. He has a Master’s(MSc) degree in Risk Management from University of Portsmouth and is a CPA and Finance professional. He currently works as a Content Manager at Risk Publishing, writing about Enterprise Risk Management, Business Continuity Management and Project Management.