Injection moulding is a widely used manufacturing process in which molten plastic is injected into a mould to produce various products. Despite its numerous advantages, such as high production efficiency and cost-effectiveness, there are inherent risks associated with this process.
Understanding and assessing these risks is crucial to ensure the safety and well-being of workers and the quality of the final products. Incorporating continuous improvement into the risk assessment process can help identify opportunities for enhancements, leading to better maintenance plans, reduced costs, and higher product quality.
This article aims to provide a comprehensive overview of the risks associated with injection moulding and the safety measures that can be implemented for risk assessmentExamining the potential hazards, such as burns, electrical shock, and exposure to hazardous substances, this article will enable manufacturers to identify and evaluate the risk associated with their specific injection moulding operations.
Additionally, it will discuss various preventive measures and control strategies that can be implemented to mitigate these risks and create a safer working environment.
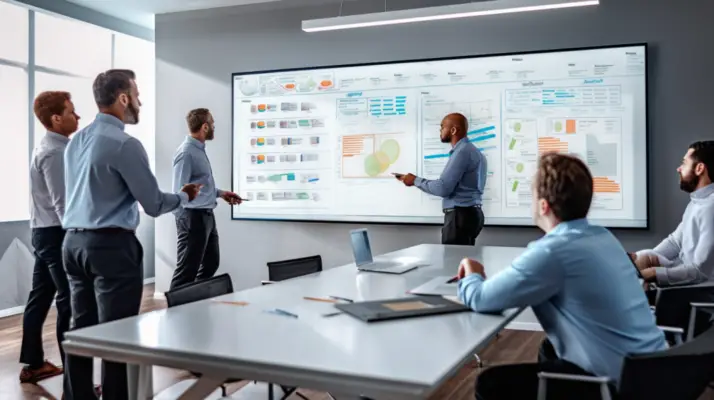
How To Conduct A Risk Assessment
Overview of the Injection Moulding Process
Understanding the operation of plastic injection moulding machines and the intricacies of manufacturing operations is vital, especially in the context of safety and risk management. These machines, responsible for the processing of nanocomposites, undergo a series of process steps that include Heating & Melting, Purging & Maintenance, and mould closure.
Each piece of equipment, from pressure sensors to pressure valves, is guided by rigorous standards such as the 1739-2009 Standard established by the American Society of Safety Engineers.
Nanocomposites have been increasingly used in medical applications due to their exceptional mechanical and antimicrobial properties. However, their production often involves using substances in dry powder form, which can pose additional, case-specific safety concerns. Styrene NIOSH, for instance, has been linked to reproductive effects and other toxicological effects.
To mitigate these risks, an in-depth nanomaterial risk assessment is crucial. This includes evaluating each emission source, managing water spillages that could disrupt operations, and using appropriate filter combinations to ensure an acceptable quality limit.
Moreover, water tank baths are common in these environments to cool and harden the moulded plastic. Yet, as with any piece of equipment, they are subject to the standards above, including the management of physical hazards and the need for regular purging and maintenance.
Administrative actions, such as setting guidelines for properly handling and disposing of materials, are also essential in preventing undue health risks. Furthermore, understanding the material’s properties, such as their potential use in medical applications or their toxicological effects, cannot be overstated.
These details provide critical information for managing the risks associated with plastic injection moulding processes.
Implementing these risk management strategies is necessary to meet regulatory standards and ensure the safe and efficient operation of plastic injection moulding machines.
Paying close attention to each process step and potential hazards, we can significantly enhance the safety of our production environments and, ultimately, the quality of our products.
The injection moulding process involves several components that work together to produce a final product. These components include:
- The mould: The mould shapes the molten plastic into the desired shape. It is typically made of two halves held together during the injection process.
- The injection unit: The injection unit is responsible for melting and injecting the plastic into the mould. It consists of a hopper, where the plastic pellets are fed, and a heating barrel, where the pellets are melted. Once the plastic is melted, it is injected into the mould through a nozzle.
- The clamping unit: The clamping unit holds the mould together and applies pressure to ensure proper moulding. It consists of two platens, which are moved by a hydraulic system. The clamping force is applied to keep the mould closed during the injection and cooling.
The injection moulding involves these three main components working together to produce high-quality plastic products.
Components of the Process
One critical aspect to consider when examining the components of the injection moulding process is the selection and design of the mould. The mould plays a crucial role in determining the quality and efficiency of the final product. It is important to choose a mould appropriate for the specific requirements of the injection molding process.
Factors such as material compatibility, part design, and production volume must be considered during the selection process. Additionally, the design of the mould should consider safety measures to minimize the risk of hazards during operation.
This includes proper venting, cooling channels, and ejection systems. Adhering to industry standards and regularly maintaining the mould and injection molding machines are also essential to ensure a safe and efficient production process.
Risks Associated with Injection Moulding
One key risk involves using plastic materials, which can release hazardous fumes during the moulding process.
Another risk is associated with operating injection moulding machines, which can pose a potential electric shock hazard.
Therefore, workers in this industry must be aware of these risks and take appropriate safety measures to mitigate them. Fostering a safety culture in injection moulding facilities is crucial, as it promotes a positive attitude towards safety among workers, managers, and stakeholders.
Plastics Industry
The plastics industry, characterized by its diverse range of polymer materials and manufacturing processes, plays a key role in the global economy as it caters to the growing demand for plastic products in various sectors.
The injection molding process, a common method used in the plastics industry, involves injecting molten plastic material into a mold to create a desired shape. While this process offers numerous benefits, such as high production rates and complex part geometries, it poses certain risks.
The injection of plastic material at high temperatures can release hazardous fumes, which can have detrimental effects on human health. To mitigate these risks, safety measures such as wearing safety glasses and using safety devices like safety covers are essential. Additionally, fire suppression systems are crucial in managing fire hazards in injection molding facilities, ensuring a comprehensive safety strategy.
Ensuring proper ventilation and implementing safety protocols is crucial to safeguarding workers from potential health risks associated with injection molding.
Safety MeasuresDescriptionImportanceSafety GlassesProtect the eyes from hazardous fumes and potential debris.Essential for personal safety.Safety DeviceSafety covers prevent accidental contact with hot components.Crucial to prevent injuries.VentilationProper ventilation removes hazardous fumes from the working environment.Necessary for maintaining a safe workplace.Safety ProtocolsImplementing and following safety protocols ensures workers’ well-being.Vital for preventing accidents and health risks.Employee TrainingProviding comprehensive training on safety procedures and equipment usage.Essential for promoting a safe work culture.
Safety measures
Plastic Material
Polymer materials, commonly used in the plastics industry, are versatile substances that can be molded into various shapes and forms to meet the demand for plastic products across different sectors.
It is important to ensure proper safety measures when working with plastic materials. The injection unit of a horizontal injection molding machine must be properly guarded to prevent any accidents or injuries.
Additionally, the high pressure involved in the injection molding process requires operators to wear appropriate personal protective equipment, such as respiratory and eye protection, to protect against any potential fumes or hazards. This is crucial for maintaining a safe working environment.
Furthermore, proper processing techniques and quality control measures should be implemented to ensure the final plastic products meet the required standards.
Injection Molding Machines
Utilizing injection molding machines is crucial in producing various plastic products because they can mold polymers into different shapes and forms.
These machines play a vital role in injection molding by melting the plastic material into a molten state and then injecting it into a mold cavity to form the desired product.
However, there are certain risks associated with the operation of these machines. Some of these risks include trip hazards due to the movement of machine parts, exposure to toxic fumes that can lead to adverse health effects, and the release of particles, such as styrene, which can negatively impact the respiratory system.
To mitigate these risks, it is important to implement corrective actions, such as installing carbon filters for capturing toxic fumes and ensuring proper heating and ventilation systems are in place to minimize the release of harmful particles.
Hazardous Fumes
Hazardous fumes emitted during injection molding can pose significant health risks to workers and should be effectively controlled and mitigated.
Exposure to fumes in the plastics processing industry necessitates a comprehensive occupational risk assessment to ensure the safety of workers.
The injection molding process involves the heating and melting plastic materials, which can release volatile organic compounds (VOCs) and other toxic substances into the air.
These fumes contain airborne particles that can be inhaled by workers, leading to various health hazards such as respiratory problems, eye irritation, and allergic reactions.
To minimize the risks associated with hazardous fumes, proper ventilation systems, such as local exhaust ventilation (LEV), should be implemented to remove the fumes at the source.
Additionally, workers should be provided with personal protective equipment (PPE) to reduce their exposure to fumes.
Regular air quality monitoring and comprehensive training programs are essential to ensure a safe working environment.
Electric Shock
Electric shock is a potential hazard that workers in the plastics processing industry may encounter during manufacturing. This risk arises from using electrical equipment and machinery in injection moulding applications.
Several sources can contribute to electric shock incidents, such as faulty wiring, inadequate grounding, or improper handling of electrical components.
To mitigate this risk, employers should implement safety measures, such as providing workers with insulated gloves and footwear and ensuring that all electrical equipment is properly maintained and regularly inspected. Additionally, employees should receive training on proper lockout/tagout procedures to prevent accidental contact with live electrical circuits. Emergency response training and well-defined procedures are also essential for effectively managing electrical hazards and ensuring worker safety during emergencies.
It is also crucial to have appropriate filters and ventilation systems to minimize the risk of chemical reactions and occupational health issues caused by electrical equipment.
A comprehensive approach to electrical safety is essential to protect workers from electric shock hazards in the injection moulding industry.
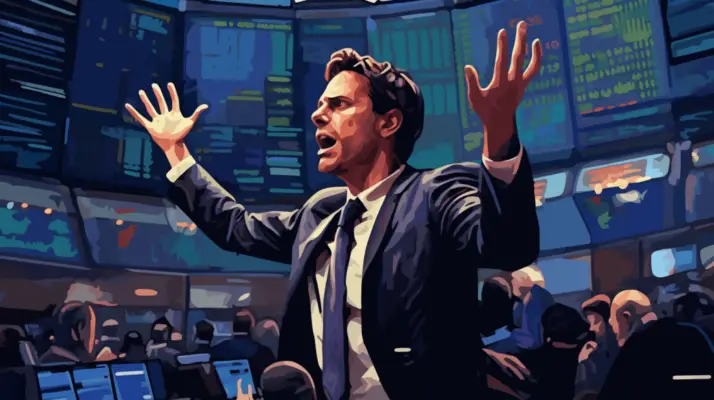
Broker-Dealer Risk Assessment Template
Molten Material
Molten material poses a significant concern in the plastics processing industry due to its high temperature and potential for severe burns. The molten plastic used in injection moulding is obtained by melting raw materials in a heated material hopper and forcing the molten plastic through a nozzle into the clamping mechanism.
This process requires careful handling of the heated material to avoid accidents and injuries. The clamping mechanism secures the mould, preventing any leakage or spillage of the molten plastic. However, exposure to molten plastic still presents a risk to workers.
The input material, which is the raw material fed into the machine, must be carefully monitored to ensure its quality and prevent any issues during the injection moulding process. Power safety measures must also be in place to prevent electrical hazards.
Despite these precautions, there is still an additional exposure risk involved in handling the extruded material, which can cause severe burns if contact is made. Thus, residual risk remains even with the implementation of safety measures.
HazardRisk LevelsControl MeasuresMolten PlasticHighEnsure proper training for handling and disposing of molten plastic. Provide appropriate personal protective equipment (PPE) such as heat-resistant gloves and aprons. Implement regular inspections of the machinery to prevent leaks or spills.Exposure to Heated MaterialHighEstablish clear and consistent protocols for handling heated material. Develop a comprehensive training program for all employees involved in the injection moulding process. Regularly inspect and maintain the machinery to ensure proper functioning.Power SafetyMediumConduct regular inspections of electrical systems and machinery to identify and address any potential hazards. Implement lockout/tagout procedures to prevent accidental startup of the machine. Provide training on power safety protocols and the proper use of electrical equipment.Residual RiskLowContinuously evaluate and update safety protocols to minimize residual risk. Encourage open communication between workers and management to address any safety concerns or near-miss incidents. Review and revise risk assessment procedures to ensure they meet industry standards.
Hazards and control measures
Trip Hazards
Trip hazards are a significant concern in the plastics processing industry, necessitating careful attention to ensure the safety of workers. In injection moulding, workers are exposed to various physical and toxicological hazards, such as molten material, which can cause severe burns and respiratory issues.
However, trip hazards also pose a significant risk in this industry.
To mitigate these risks, it is important to implement safety measures and maintain a hazard-free work environment. Here are five key considerations:
- Ensure proper housekeeping to eliminate clutter and ensure clear pathways.
- Regularly inspect and maintain equipment to prevent any electrical hazards.
- Use pressure indicators, sensors, and valves to monitor and control the pressure in the moulding process.
- Keep electrical equipment away from water or damp areas to prevent electrical shocks.
- Maintain good ambient air quality to prevent respiratory issues caused by exposure to hazardous fumes or dust.
Addressing trip hazards, companies can create a safer workplace and minimize the risk of accidents and injuries.
Safety Measures for Risk Assessment in Injection Moulding Processes
Safety glasses are essential to prevent eye injuries caused by flying debris or chemical splashes.
Safety devices such as interlocks and guards play a crucial role in ensuring that operators are protected from potential hazards during the operation of the moulding machine. Continuous improvement in safety measures can further enhance the protection provided by these devices.
Additionally, considering the health risks associated with exposure to hazardous substances and fumes, workers should be protected to minimize the risk of respiratory illnesses.
Personal Protective Equipment: Safety Glasses
Safety glasses are a crucial protective measure in injection moulding operations, safeguarding workers’ eyes from potential hazards. These hazards include flying debris, chemical splashes, and exposure to intense light.
Safety glasses provide ocular protection by creating a barrier between the eyes and the hazardous processes involved in injection moulding.
They are designed to be impact-resistant and typically have side shields for added protection. Safety glasses may also have tinted lenses to shield the eyes from intense light emitted during the process.
To emphasize the importance of safety glasses in injection moulding risk assessment, the following table provides examples of potential hazards and the corresponding protective measures:
HazardProtective MeasureFlying debrisSafety glassesChemical splashesSafety glassesIntense lightSafety glasses with tinted lenses
Hazard
Workers must wear safety glasses consistently and correctly, following standard operating procedures. Regularly monitoring airborne particle concentration readings, especially when working with ABS plastic thermal processing (acrylonitrile butadiene styrene), should be conducted to ensure a safe working environment.
Safety Devices
A critical aspect of ensuring the well-being of workers in injection moulding operations involves the implementation of various safety devices.
To protect workers from potential hazards, safety devices are used to minimize the risks associated with the process.
One important safety device is safety glasses, which protect the eyes from flying debris or splashing of hot materials.
Additionally, using fume hoods is essential in controlling the release of organic compounds and fumes that may be emitted during the moulding process.
Other safety devices include adjustable guards that prevent access to the moulding area during operation, temperature-controlled moulds to prevent burns from material hot, and ancillary equipment to enhance the safety and efficiency of the operation.
Implementing these safety devices is crucial in ensuring the protection and well-being of workers in injection moulding operations, especially when working with medical devices and nanocomposite materials.
Health Risks
Moving on from the discussion of safety devices in injection moulding, addressing the health risks associated with this process is important.
One significant aspect of health risk assessment in injection moulding is the evaluation of nanomaterial hazards. The risk assessment involves examining the potential risks posed by nanomaterials, such as nanoparticles released during the moulding process.
Additionally, the exposure to hazardous substances, such as ABS degradation fumes, in the temperature-controlled mould can lead to harmful health effects. These effects can range from DNA damage to lung damage.
For instance, exposure to styrene, a common component in ABS plastic, has been linked to adverse health effects, as reported by the National Institute for Occupational Safety and Health (NIOSH).
Considering the wide range of applications for injection moulding, including medical and aerospace applications, it is crucial to assess and manage the associated health risks thoroughly.
Respiratory Protection
Respiratory protection is crucial in addressing the potential health risks of inhaling hazardous substances during injection moulding. To ensure the safety of workers, it is important to implement proper measures. Here are three key aspects to consider:
- Temperature-controlled mould: Maintaining a controlled mould temperature helps reduce the emission of hazardous substances, minimizing the risk of respiratory exposure.
- Shock electrical and guard interlocks: Proper electrical systems and guard interlocks prevent accidental exposure to hazardous substances, ensuring worker safety.
- Source containment and maintenance program: Implementing source containment measures and a regular maintenance program helps prevent the release of hazardous substances into the air, reducing respiratory risks.
Incorporating these measures, the risk of respiratory exposure can be effectively managed in the injection moulding process.
It is essential to prioritize the health and safety of workers by providing adequate respiratory protection, particularly when handling hazardous substances in their dry form.
Frequently Asked Questions
What are the different types of injection moulding machines used in the industry?
Several types of injection moulding machines are used in the industry, including hydraulic, electric, and hybrid machines. Each type has its own advantages and disadvantages regarding precision, speed, energy efficiency, and cost.
How often should risk assessments be conducted in an injection moulding facility?
It should be conducted regularly to ensure workers’ safety and compliance with regulations. The frequency of these assessments depends on factors such as the size and complexity of the facility, but a general recommendation is to conduct them at least annually.
Are there any specific safety certifications or regulations that injection moulding facilities must adhere to?
Injection moulding facilities must adhere to specific safety certifications and regulations to ensure safe operations. These may include certifications such as ISO 9001 and ISO 14001. Also, compliance with regulations like OSHA standards and local environmental regulations.
What is the average cost of implementing safety measures in an injection moulding process?
The average cost of implementing safety measures in an injection moulding process can vary depending on various factors, such as the size of the facility, the level of automation, and the specific safety measures required.
Are any specific training programs available for employees working with injection moulding machines to enhance safety awareness?
Training programs are available for employees working with injection moulding machines to enhance their safety awareness. These programs aim to educate employees on the potential risks and hazards involved in the process, They also provide them with the necessary skills and knowledge to mitigate those risks.
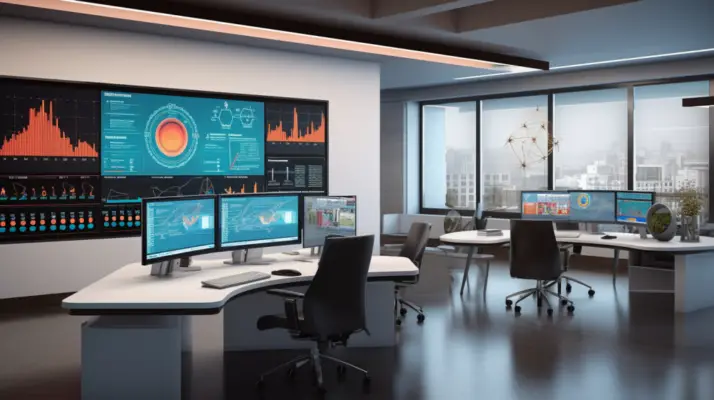
CIS Risk Assessment
Conclusion
The injection moulding process is a widely used manufacturing technique that comes with its own set of risks. These risks include:
- Machine malfunctions.
- Exposure to hazardous materials.
- Potential injuries from moving parts.
To ensure the safety of workers and reduce the risk of accidents, it is important to conduct a thorough risk assessment. This assessment should include:
- Identifying potential hazards.
- Implementing safety measures such as machine guarding and proper training.
- Regularly reviewing and updating safety protocols.
Following these safety measures, the injection moulding process can be carried out with minimal risk to workers.
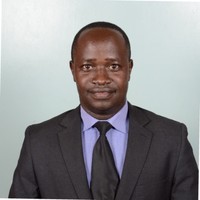
Chris Ekai is a Risk Management expert with over 10 years of experience in the field. He has a Master’s(MSc) degree in Risk Management from University of Portsmouth and is a CPA and Finance professional. He currently works as a Content Manager at Risk Publishing, writing about Enterprise Risk Management, Business Continuity Management and Project Management.