As any business owner knows, supply chains are critical for a successful business. A supply chain is a set of suppliers, manufacturers, distributors, and retailers involved with producing and selling products.
Almost every business depends on its supply chains for smooth functioning. The supply chain, however, is vulnerable to risks as well. NIST standards have important implications for vendor information. Disruptions can happen throughout an organization and can affect the business majorly. The importance of a strong supplier chain risk management program is always high.
A supply chain risk management plan is an essential tool for any business that operates a supply chain with major suppliers, as it helps ensure that risks are identified and addressed in a timely manner and in a business ecosystem.
This blog post will discuss why having a supply chain risk management plan template is important and how to create one.
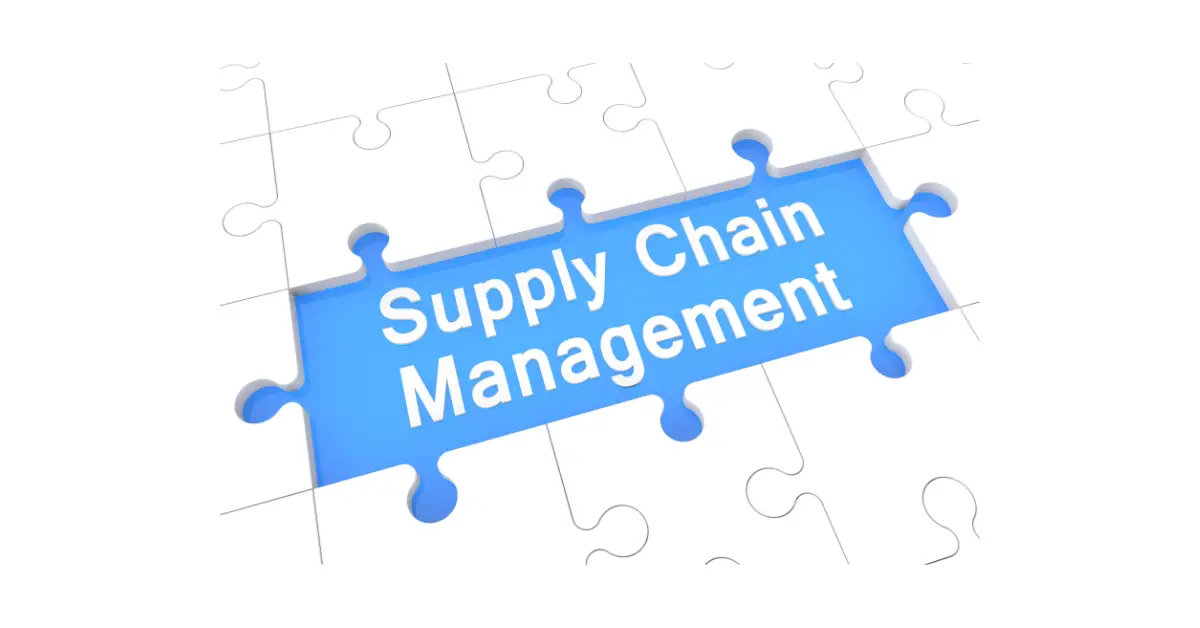
What Is Supply Chain Risk Management?
Supply chain risk management is the process of identifying, analyzing, assessing, and responding to potential risks within the supply chain. It involves looking at the entire supply chain and understanding the possible risks and their impact on operations.
A well-crafted plan can help businesses identify and mitigate potential threats before they become costly to supply chain management.
Supply chain risk control plans can be used to predict possible incidents to minimize disruption to the supply chain. The risk may arise from prior learning experiences and industry-common incidents.
Why Do You Need a Supply Chain Risk Management Plan Template?
Having a pre-drafted risk management plan template can be helpful in developing an effective strategy for managing your organization’s supply chain risks. A template allows you to easily identify any weak points in your current system and provide solutions to address them.
It also helps streamline the process of creating a comprehensive risk management plan because you don’t have to start from scratch each time.
It is essential to have a proper risk management plan in place for your supply chain. With the right measures and strategies, you can effectively minimize risks associated with global sourcing, manufacturing, transportation, storage, and distribution of products.
The main goal of any risk management plan is to ensure that any potential interruptions or delays are minimized in order to keep the supply chain running smoothly and efficiently.
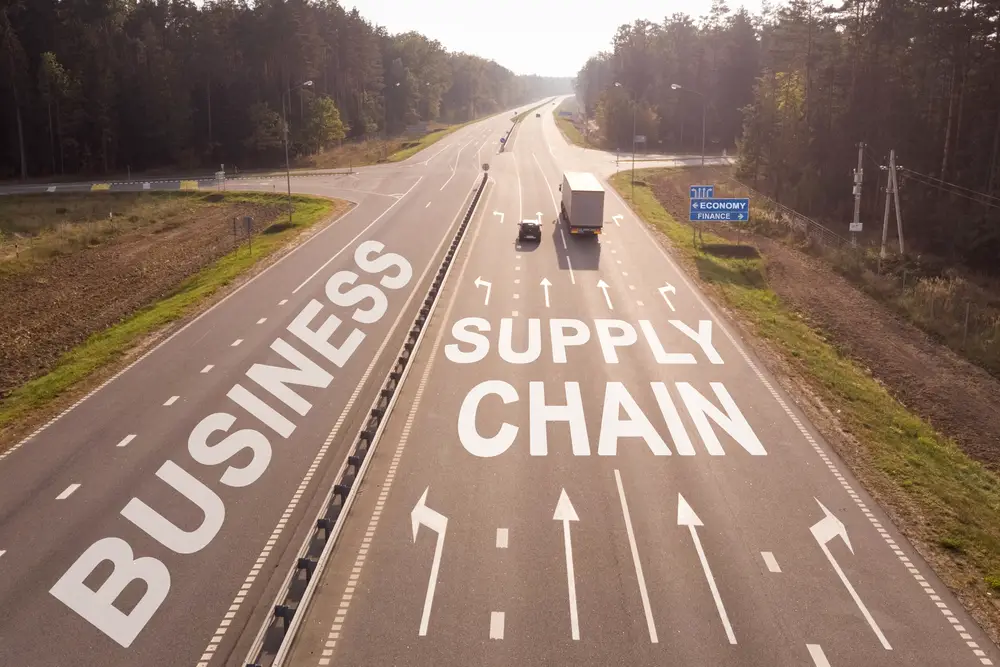
How To Create Your Own Supply Chain Risk Management Plan Template
Creating your own risk management plan template doesn’t have to be difficult or time-consuming. First, start by identifying all of the common risks associated with your particular industry and type of business operations (e.g., delivery delays, supplier bankruptcies, etc.).
Once these are identified, then brainstorm possible solutions for minimizing or eliminating each type of risk (e.g., diversifying suppliers or using third-party logistics providers). Finally, document these ideas into your own custom risk management plan template that you can refer back to whenever needed.
Now let’s take a look at an example template for developing a risk management plan for your supply chain:
1. Identify potential risks
Start by identifying all possible risks that could potentially affect your supply chain operations. This includes things like natural disasters, geopolitical unrest, supplier bankruptcy, etc. Make sure to include as many potential risks as possible so that nothing is overlooked.
2. Assess potential impacts
Once you’ve identified all possible risks, it’s time to assess their potential impacts on your business operations. For each identified risk, you should estimate the probability of it occurring as well as its potential severity if it does occur.
This will give you an idea of which risks need more attention than others when it comes to preparing contingency plans and mitigation strategies.
3. Formulate mitigation strategies
Next up is formulating mitigation strategies for each identified risk. These strategies should be tailored specifically for each individual risk in order to maximize their effectiveness in mitigating any negative impacts from occurring if they do happen. Some common mitigation strategies include setting up early warning systems, diversifying suppliers/distribution channels/etc., establishing alternate routes/transport methods, and increasing inventory levels/supply chain capacity.
4.Implement contingency plans
Finally, you should formulate contingency plans for each individual risk that outline what steps need to be taken if something goes wrong (e.g., an unexpected disruption occurs).
These plans should provide clear instructions on how best to respond and contain specific actions that need to be taken (e.g., rerouting shipments via alternate routes) in order to minimize any negative impacts from occurring while also ensuring minimal disruptions in operations overall.
Do you really need a supply chain risk management plan?
The Coronavirus pandemic has given us a chance to assess the benefits of a good supply system and the weaknesses of global supply chains. No supply chain has worked so smoothly before, or perhaps never before, and risk management plans are used to mitigate risks.
Even in companies whose supply chain risk management plan exists, there is no guarantee of the effects of these viruses. More than half of American manufacturing supply chains suffer from lockdowns.
Consider your risks
It’s impossible to plan what we aren’t able to imagine. Several risks in the supply chain can be seen without knowing the real cause and impact: global economic instability; unknown partner/suppliers finance problems; future climate and weather events; and, of course, pandemics and even pandemics.
These may appear invisible and therefore unpredictable now, however, which can lead to delays, higher costs, and reduced sales and customer services. Take a lesson from your past, and observe how things are going on in the present to see where we can expect to be.
Build contingencies
Companies need flexibility. They want a quick response to minimize delays, interruptions, or long-term damage. Unfortunately, many businesses do not have strong preparedness plans due to a lack of time to research their response plans to risk factors.
This method is the best way for everyone who knows how to react to predicted future scenarios. The models give companies some early access to a better position to react rapidly in a situation that arises.
Score your risks
There must be a clear definition of risks and what the impact of these risks will be on the supply chain. Therefore identifying risks can help gain an immediate sense of which risks are worthy of the best attention and how.
This risk scoring can be numbers, colors, or a graphic representation illustrating how risk is compared to risk within the supply chain to prioritize the right risk at the right time.
Conclusion
Having an effective supply chain risk management plan can save businesses time and money while helping them remain competitive in their respective markets. Developing a customized plan takes some effort but having a structured approach, such as utilizing a supply chain risk management plan template.
This can simplify the process—allowing you to quickly create an effective strategy for managing potential risks within your organization’s supply chain operations.
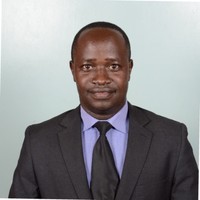
Chris Ekai is a Risk Management expert with over 10 years of experience in the field. He has a Master’s(MSc) degree in Risk Management from University of Portsmouth and is a CPA and Finance professional. He currently works as a Content Manager at Risk Publishing, writing about Enterprise Risk Management, Business Continuity Management and Project Management.