A Business Continuity Plan (BCP) for a manufacturing company involves creating a document that outlines how a business will continue operating during an unplanned disruption in service.
It’s more extensive than a simple emergency plan and includes contingencies for business processes, assets, human resources, and business partners – every aspect of the business that might be affected.
For a manufacturing company, the BCP should address specific risks like supply chain disruptions, loss of or damage to critical machinery, or workforce unavailability. The plan should include:
- Business Impact Analysis (BIA): This will help identify and prioritize critical processes and the resources needed to support them.
- Recovery Strategies: These are plans for restoring operations to operational capacity after a disruption. This might include alternative sourcing strategies, machinery repair/replacement procedures, and workforce reallocation for manufacturing.
- Plan Development: Documenting the recovery strategies and processes to return to business as usual. This would involve detailed step-by-step action plans for different scenarios.
- Testing and Exercises: Regular testing of the BCP is crucial to ensure that the plan is effective and that staff are familiar with it.
- Plan Maintenance: The BCP should be reviewed and updated regularly to ensure it remains current with the business operations and any changes in the risk environment.
For example, the Business Continuity Plan Template provided by the California Office of Emergency Services includes procedures for all recovery phases as defined in the document’s Business Continuity Strategy. This template could be adapted to suit the specific needs of a manufacturing company.
Remember, the most effective BCPs are those that are tailored to the specific needs and operations of the business. While templates can provide a good starting point, it’s important to customize the plan to fit the unique circumstances of your manufacturing operations.
A business continuity plan (BCP) is crucial for any organization; manufacturing companies are no exception. A BCP outlines the steps a company will take in the event of a disaster or disruption to its operations, ensuring that the business can continue to function and recover as quickly as possible.
A BCP is essential in the manufacturing industry, where supply chain disruptions, equipment failure, and natural disasters are common occurrences.
A BCP for manufacturing should include a comprehensive risk assessment and management plan detailing the potential risks and vulnerabilities that the company faces.
This should be followed by a response plan outlining the company’s steps in the event of a disruption, including communication protocols, emergency procedures, and backup plans.
The BCP should also include a recovery and continuity strategy detailing how the company will return to normal operations as quickly and efficiently as possible.
Business continuity ensures that a company can continue to function in the event of a disruption or disaster.
This involves identifying potential risks and vulnerabilities, creating a plan to mitigate those risks, and implementing that plan in the event of a disruption. A BCP is a crucial part of business continuity, as it outlines the steps that the company will take to recover and continue operations in the event of a crisis.
Key Takeaways
- A business continuity plan is essential for manufacturing companies to ensure they can continue functioning during a disruption or disaster.
- A BCP for manufacturing should include a comprehensive risk assessment and management plan, a response plan, and a recovery and continuity strategy.
- Business continuity is the process of ensuring that a company can continue to function in the event of a disruption or disaster.
Understanding Business Continuity
Defining Business Continuity
Business continuity is creating a plan to ensure that a business can continue to operate in the event of a disruption.
A business continuity plan (BCP) is a document that outlines the steps a company will take to ensure that it can continue to function during and after a disruption. A BCP’s goal is to minimise a disruption’s impact on a company’s operations, customers, and employees.
Importance in Manufacturing
In the manufacturing industry, disruptions can significantly impact a company’s ability to produce goods and meet customer demand.
Disruptions can come in many forms, including natural disasters, cyber-attacks, and equipment failures. A well-designed BCP can help a manufacturing company minimize the impact of these disruptions and maintain business continuity.
A BCP for a manufacturing company should include a detailed inventory of all equipment and machinery, as well as a plan for how to quickly repair or replace any equipment damaged or destroyed during a disruption.
The plan should also include a list of alternative suppliers and transportation options in case the company’s primary suppliers or transportation methods are unavailable.
In addition to equipment and supplier considerations, a BCP for a manufacturing company should also include plans for employee safety and communication during a disruption.
This may include emergency evacuation plans, communication protocols, and plans for providing employees with necessary resources such as food, water, and shelter.
A well-designed BCP is an essential tool for any manufacturing company that wants to ensure that it can continue to operate during and after a disruption.
By creating a comprehensive BCP, a manufacturing company can minimize the impact of disruptions and maintain business continuity.
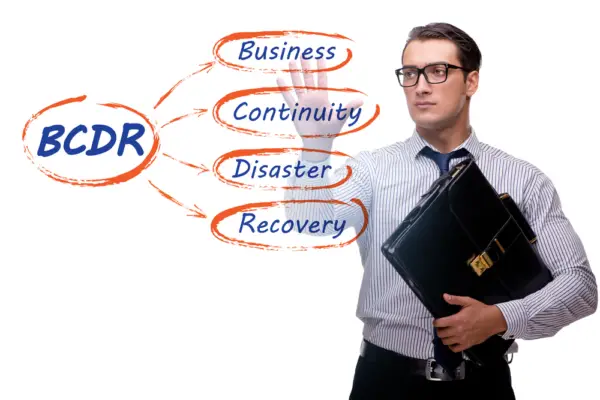
Elements of a Business Continuity Plan
A Business Continuity Plan (BCP) is a comprehensive document that outlines an organization’s protocols for responding to an operational disruption.
It is designed to ensure critical business functions can continue during and after a disaster or other emergency.
Key Objectives
The primary objective of a BCP is to minimize the impact of a disruption on the organization’s operations, customers, and employees.
This includes ensuring that critical business processes can continue during and after the disruption and that the organization can recover quickly.
Other key objectives of a BCP include:
- Identifying potential risks and threats to the organization’s operations
- Establishing procedures for responding to a disruption
- Ensuring that all employees are aware of their roles and responsibilities during a disruption
- Establishing communication channels for keeping employees, customers, and other stakeholders informed during a disruption
- Testing and updating the BCP on a regular basis to ensure that it remains effective and up-to-date
Critical Processes
A BCP should identify the critical business processes that must be maintained during a disruption. This includes production, distribution, sales, and customer service processes.
The BCP should also establish procedures for maintaining these critical processes during a disruption, including identifying backup facilities, equipment, and personnel.
Roles and Responsibilities
A BCP should clearly define the roles and responsibilities of each team member during a disruption. This includes identifying key personnel responsible for activating the BCP and ensuring critical business processes continue.
During a disruption, the BCP should also establish communication procedures for employees, customers, and other stakeholders, including identifying who will communicate with each group.
Overall, a well-designed BCP can help organizations minimize the impact of a disruption on their operations and ensure that critical business processes continue during and after a disaster or other emergency.
Risk Assessment and Management
When it comes to creating a Business Continuity Plan (BCP) for a manufacturing company, risk assessment and management are critical components.
Risk assessment aims to identify potential risks that could disrupt operations and cause financial loss. Once risks are identified, the company can create a plan to mitigate and manage them effectively.
Identifying Risks
The first step in risk assessment is to identify potential risks that could impact the company’s operations. This includes identifying risks to assets, such as equipment, facilities, and inventory, as well as to personnel, such as employee safety and health.
Other potential risks could include natural disasters, cyber-attacks, supply chain disruptions, and power outages.
To identify potential risks, a manufacturing company can conduct a risk assessment by reviewing historical data, conducting surveys, and analyzing industry trends. It is important to involve all stakeholders in the risk assessment, including employees, suppliers, and customers.
Business Impact Analysis
Once potential risks are identified, the next step is to conduct a business impact analysis (BIA). The BIA helps determine each risk’s potential impact on the company’s operations and finances. This includes identifying critical business functions and determining the impact of disruptions to those functions.
During the BIA, the company should identify the maximum time that each critical business function can be disrupted before it causes significant financial loss. This information can be used to prioritize the company’s response to each risk.
Overall, risk assessment and management are critical components of a BCP for a manufacturing company. By identifying potential risks and conducting a BIA, the company can create a plan to mitigate those risks and manage them effectively. This will help to ensure that the company can continue to operate in the event of a disruption and minimize financial loss.
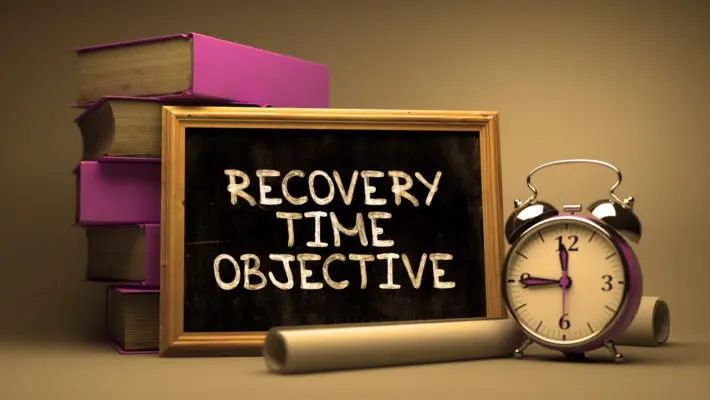
Response to Disruptions
When a disruption occurs in a manufacturing business, it is crucial to have a plan in place to minimize the impact and ensure business continuity. The response to disruptions should be swift and effective, with immediate actions taken to mitigate the effects of the disruption.
Immediate Actions
The first step in responding to a disruption is to assess the situation and determine the extent of the damage. This may involve shutting down certain operations or evacuating the facility if necessary. Once the situation has been assessed, immediate actions should be taken to prevent further damage and ensure the safety of employees.
Communication Plan
Effective communication is essential in responding to a disruption. A communication plan should be in place to ensure that all employees are informed of the situation and understand their roles and responsibilities.
The plan should include contact information for key personnel and procedures for communicating with customers, suppliers, and other stakeholders.
Disaster Recovery Procedures
Disaster recovery procedures should be in place to ensure that critical systems and data can be restored during a disruption. These procedures should include backup and recovery strategies and plans for testing and maintaining these systems.
Overall, a well-designed business continuity plan can help manufacturing businesses confidently respond to disruptions and minimize the impact on operations.
By having procedures in place for communication, immediate actions, and disaster recovery, businesses can ensure that they are prepared for any emergency.
Recovery and Continuity Strategies
Developing Recovery Strategies
Once a business has identified the potential risks and threats to its manufacturing operations, it’s important to develop recovery strategies.
Recovery strategies should be designed to minimize downtime and ensure the business can continue operating even in the face of an outage or other disruption.
One important aspect of developing recovery strategies is to identify critical resources and prioritize their recovery. This might include backup power sources, alternative supply chain options, or redundant production facilities.
By prioritizing the recovery of critical resources, businesses can minimize the impact of an outage and ensure that they can continue to operate.
Another important aspect of developing recovery strategies is to develop a backup plan for key business operations. This might include developing alternative production plans or identifying suppliers for critical raw materials.
By developing a backup plan, businesses can ensure that they can continue to operate even if their primary operations are disrupted.
Continuity of Operations
In addition to developing recovery strategies, businesses also need to ensure continuity of operations. Continuity of operations refers to the ability of a business to continue operating in the face of a disruption or outage.
Developing a business continuity plan is one important aspect of ensuring continuity of operations. A business continuity plan should outline the business’s steps to ensure that critical operations can continue in the face of disruption.
This might include identifying alternative production facilities or developing alternative supply chain options.
Another important aspect of ensuring operations continuity is establishing clear communication channels. This might include establishing a dedicated communication plan for employees, suppliers, and customers.
By establishing clear communication channels, businesses can ensure that everyone is aware of the situation and can work together to minimize the impact of an outage.
Overall, developing recovery strategies and ensuring continuity of operations are critical components of any business continuity plan for manufacturing.
By taking these steps, businesses can minimize downtime, ensure critical resources are prioritized for recovery, and continue operating even in the face of an outage or other disruption.
Implementation and Training
Once the Business Continuity Plan (BCP) for the manufacturing facility has been developed, the next step is to implement it. This involves training the staff, conducting testing and exercises, and ensuring overall preparedness.
Staff Training and Awareness
Training all employees on the BCP and their specific roles in implementing it is essential. This includes educating them on the potential risks and threats to the facility, the procedures to follow during an emergency, and the importance of maintaining business continuity.
Regular training sessions should be conducted to ensure that all employees know the latest developments in the BCP and are prepared to handle any situation. This will help to ensure that the staff is confident and knowledgeable in implementing the BCP.
Testing and Exercises
Testing and exercises are critical components of the BCP implementation process. Regular testing helps identify any gaps or weaknesses in the plan and provides an opportunity to address them before an emergency occurs.
The testing process should be designed to simulate different types of emergencies, such as natural disasters, cyber-attacks, and supply chain disruptions. This will help to ensure that the staff is prepared to handle any situation that may arise.
Exercises should be conducted regularly to keep the staff engaged and aware of the BCP. This will help to ensure that the staff is confident and knowledgeable in implementing the BCP.
Overall, the implementation and training phase is critical to the success of the BCP. By ensuring that all employees are trained and aware of their roles and responsibilities and by regularly testing and exercising the plan, the manufacturing facility can be confident in its ability to maintain business continuity in an emergency.
Continual Improvement
A business continuity plan (BCP) is not a one-time document that can be created and forgotten. It requires continual improvement to ensure that it remains relevant and effective.
This section will discuss two key aspects of continual improvement for a BCP: monitoring, reviewing and updating the BCP.
Monitoring and Reviewing
Monitoring and reviewing the BCP is essential to ensure it remains effective in changing circumstances. This involves tracking key performance indicators (KPIs) and measurable targets to ensure the BCP achieves its intended outcomes.
The Cascade Strategy Execution Platform is a useful tool for monitoring and reviewing a BCP. It provides real-time visibility into the progress of the BCP, allowing for roll-up reports that can be used to identify areas for improvement.
Automated workflows can also ensure that the BCP is followed consistently and that any issues are addressed promptly.
Updating the BCP
Updating the BCP is necessary to ensure that it remains relevant and effective. This involves reviewing the BCP on a regular basis and making changes as needed to reflect changes in the business environment or the organization’s priorities.
When updating the BCP, it is important to consider the organization’s resilience and its ability to adapt to changing circumstances. This may involve revising the BCP to include new risks or threats or updating the BCP to reflect changes in the organization’s priorities or resources.
Overall, continual improvement is essential for ensuring a BCP remains effective in changing circumstances. By monitoring and reviewing the BCP and updating it as needed, organizations can ensure that they are prepared to respond to any disruptions that may arise.
Plan Documentation and Templates
Business continuity planning is a critical aspect of any organization. It helps to ensure that a business can continue to operate in the event of a disaster or other unexpected event.
One of the most important components of business continuity planning is creating a business continuity plan (BCP).
BCP Template Overview
A BCP template is a pre-built framework that can be used as a starting point for creating a business continuity plan. These templates can be found in various formats such as Word, PDF, or on a platform such as Smartsheet.
Using a BCP template can help save time and effort when creating a plan, as it provides a structure and framework that can be easily customized.
When selecting a BCP template, choosing one specifically designed for the manufacturing industry is important. This will ensure the plan addresses manufacturing operations’ unique challenges and risks.
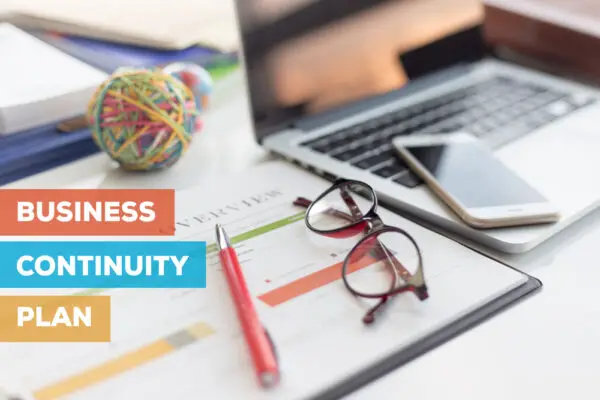
Customizing Your Template
Once a suitable BCP template has been selected, it is important to customize it to meet the organisation’s specific needs. This may involve adding or removing sections, modifying existing sections, or adding additional information.
It is important to ensure that the BCP is tailored to the organisation’s specific needs. This may involve conducting a risk assessment to identify the potential risks and vulnerabilities that the organization faces. Once these risks have been identified, they can be incorporated into the BCP to ensure that the plan addresses them effectively.
In conclusion, using a BCP template can effectively create a business continuity plan for a manufacturing organization.
A comprehensive and effective BCP can be created by selecting a template specifically designed for the manufacturing industry and customizing it to meet the organisation’s specific needs.
Support and Resources
Internal and External Support
Creating a comprehensive business continuity plan for manufacturing can be a daunting task. It is important to have internal and external support to ensure the plan is effective.
The first step is to establish a governance structure that includes key stakeholders from various departments within the organization. This group should develop policies and procedures that align with the organization’s goals and objectives.
In addition to internal support, it is important to have external support from business continuity experts. These experts can provide valuable insights and guidance on best practices for creating a successful plan. They can also offer tips on effectively communicating the plan to employees and stakeholders.
Additional Resources
Various resources are available to help manufacturing companies create a business continuity plan.
These resources can include templates, checklists, and guides that can be customized to fit the organisation’s unique needs. Some resources may be free, while others may require a fee.
Contact information for these resources can be found online or through professional organizations such as the Business Continuity Institute or the Disaster Recovery Institute. It is important to carefully evaluate each resource to ensure it aligns with the organization’s goals and objectives.
Overall, having internal and external support and access to additional resources can greatly enhance the effectiveness of a business continuity plan for manufacturing.
By working together and utilizing the right tools, organizations can create a comprehensive, effective, and adaptable plan.
Challenges and Considerations
Manufacturing companies face unique challenges when creating a Business Continuity Plan (BCP). In this section, we will explore some challenges and considerations that manufacturing companies must consider when creating a BCP.
Supply Chain Challenges
Manufacturing companies are often at the supply chain’s midpoint, which means they have partners and commitments on both sides of the supply chain.
As a result, supply chain disruptions can significantly impact a manufacturing company’s ability to deliver products to customers on time. Therefore, it is essential for manufacturing companies to have a clear understanding of their supply chain and to identify alternate suppliers in case of supply chain disruptions.
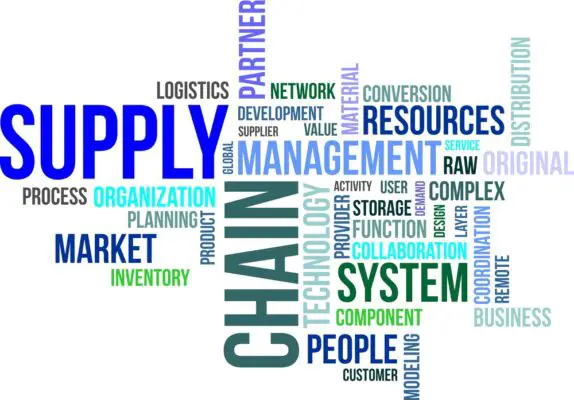
Adapting to Industry Changes
Manufacturing companies must be able to adapt to industry changes quickly. For example, the COVID-19 pandemic has resulted in global supply chain issues and disruptive events affecting manufacturing companies worldwide.
Therefore, manufacturing companies must have a BCP that can help them minimize the risk of financial loss and unplanned downtime during critical events such as severe weather activity, man-made disasters, and hazardous materials incidents.
Manufacturing companies must also be prepared for technology failures that can disrupt their operations. Therefore, it is essential to have a BCP checklist that includes procedures for maintaining and repairing computers, networks, and other technology systems.
In addition, manufacturing companies must ensure that their BCP addresses customer satisfaction and brand reputation. A BCP should include solutions for maintaining quality during emergencies and minimizing the impact of supply chain disruptions on factory utilization rates.
In summary, manufacturing companies must take into account supply chain issues, global supply chain issues, disruptive events, severe weather activity, man-made disasters, hazardous materials incidents, supply chain disruptions, technology failures
Customer satisfaction, brand reputation, financial loss, unplanned downtime, and factory utilization rates when creating a BCP. By doing so, they can ensure that they are prepared for unexpected events and minimise disruptions’ impact on their operations.
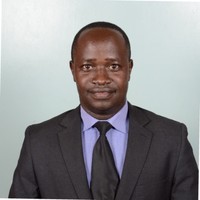
Chris Ekai is a Risk Management expert with over 10 years of experience in the field. He has a Master’s(MSc) degree in Risk Management from University of Portsmouth and is a CPA and Finance professional. He currently works as a Content Manager at Risk Publishing, writing about Enterprise Risk Management, Business Continuity Management and Project Management.