In the intricate world of business, the supply chain juggles numerous parameters, interconnecting a multitude of components across vast geographical spaces and timelines.
Within this complex system, uncertainty and unpredictability often precipitate a cascade of risks that can significantly impact business operations, profitability, and reputation.
Therefore, Risk Assessment plays an irreplaceable role in the realm of Supply Chain Management.
It functions as a vigilant sentinel and a litmus test that can not only mitigate disruptions and financial losses but also consolidate a company’s competitive edge.
This article will delve into the essentiality of risk assessment in the supply chain, offering an in-depth exploration of risk classifications, assessment tools and techniques, implementation steps, and resonating cases.
The Importance of Risk Assessment in Supply Chain
Risk Assessment in Supply Chain Management
Risk assessment in Supply Chain Management (SCM) signifies the determination and evaluation of risks that could potentially disrupt the regular functioning of the supply chain process.
It involves comprehensively examining the supply chain processes to identify potential vulnerabilities that may lead to disruptions, financial losses, missed deadlines, or harm to a company’s reputation.
Why is Risk Assessment Crucial in SCM
Evaluating risks in supply chain management is pivotal due to the interconnected nature of SCM.
As the supply chain relies heavily on multi-entity relationships for the procurement and distribution of goods, any disruption at any level can ripple down and impact the entire chain.
Therefore, being aware of potential risks and formulating strategies to mitigate them is crucial.
Preventive Risk Management in SCM
Preventive risk management is a forethought, proactive approach toward minimizing the chances of disruptive events within the supply chain.
It involves identifying potential risks, assessing their likelihood, and developing comprehensive plans to manage them.
Adopting preventive risk management can protect your supply chain from significant time lags, financial losses, and reputational damage.
Risk Assessment as a Competitive Advantage in Businesses
Risk assessment provides a necessary competitive edge in business environments by enabling firms to handle uncertainties and disruptions effectively.
By identifying and preparing for potential risks in advance, companies can avoid significant losses, keep their operations running smoothly, and stay ahead of the competition.
The end goal of risk assessment is to devise robust risk management strategies that minimize vulnerability and increase resilience.
Companies that prioritize risk assessment and management can maintain healthy relationships with vendors, keep costs down, enhance customer satisfaction, and ultimately, ensure business sustainability and success.
The Financial Implications of Risk Assessment in SCM
From a financial perspective, risk assessment in the supply chain is critically significant. A well-planned, thorough risk assessment can help a firm identify cost-effective strategies to deal with potential risks.
It can also ensure that businesses are not caught unprepared for disruptions, thereby saving considerable costs related to emergency response measures.
Role of Risk Assessment in Protecting Business Reputation
A thorough risk assessment is instrumental in maintaining and enhancing the reputation of a business.
If a company effectively manages disruptions, it earns itself a reputation as a trustworthy and reliable entity, thereby improving its brand image.
On the other hand, a business that neglects risk management strategies may significantly tarnish its reputation, leading to a decline in customer base and market share.
The significance of risk assessment in protecting a company’s stature cannot be emphasized enough.
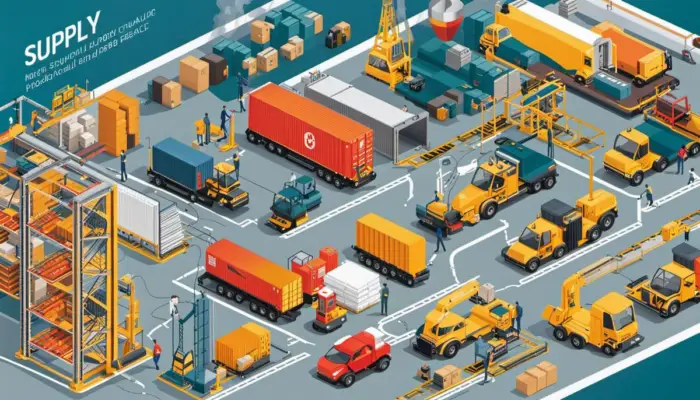
Classification of Risks in Supply Chain
Understanding Operational Risks within the Supply Chain
Operational risks in a supply chain can be categorized as potential obstacles that may interrupt the regular operations related to the supply chain.
These obstacles include machinery breakdown, labor disputes, security breaches, product recalls, or production delays.
The ramifications of such risks can vary from immediate financial losses and reduced productivity to strained corporate relationships and potential damage to the company’s reputation in the long run.
The probability of encountering these operational risks depends on the intricacy of the supply chain and the degree to which a company is equipped for risk management.
Disruption Risks in Supply Chain
Disruption risks in a supply chain refer to the interruption of the movement of goods or services from a supplier to a customer.
This can be caused by unforeseen events such as natural disasters, terrorist attacks, trade wars, or pandemics.
Disruption risks can lead to increased costs due to supply shortages, delayed deliveries, decreased customer satisfaction, and potential loss of market share.
The likelihood of disruption risks depends on the supply chain participants’ geographic location, business continuity plans, and external uncontrollable factors.
Demand Risks in Supply Chain
Demand risks in a supply chain address the potential variability of customer demand. These risks can arise from changes in consumer tastes, economic fluctuations, competitor activity, or the introduction of new products.
The impact of demand risks on supply chains can include excess or inadequate inventory, loss of sales, increased lead times, and a ripple effect of disruptions across the supply chain.
Demand forecasting accuracy influences the likelihood of demand risks, the manufacturer’s flexibility to adapt to changes, and the marketplace dynamics.
Procurement Risks in Supply Chain
Procurement risks in a supply chain encompass the potential negative events throughout purchasing goods or services necessary for the organization’s operations.
These can vary from supply shortages, quality issues, price volatility, unethical practices, or supplier bankruptcy.
The impacts of procurement risks can lead to increased costs, compromised quality, delayed deliveries, reputation damage, and disruption in the overall supply chain operations.
The likelihood of procurement risks is contingent on the supplier’s reliability, contractual terms, raw material availability, and global market conditions.
Every risk in the supply chain should be closely evaluated, bearing in mind its potential impact and probability. This process is known as risk assessment, a crucial part of supply chain management.
It necessitates forming risk management strategies to alleviate these risks, minimize operational disruptions, and maintain a stable supply.
Ensuring organizational resilience in the face of uncertainties is a key objective of such strategies.

Risk Assessment Tools and Techniques
Understanding Risk Assessment in Supply Chain
Viewed as a vital component of a well-tailored business strategy, risk assessment in the supply chain plays a significant role in preparing organizations for the possible hurdles and vulnerable aspects of their operations.
Its predictive ability provides a paradigm for increased operational efficiency, ensuring a seamless and uninterrupted flow of goods and services from production facilities to end users.
Qualitative and Quantitative Risk Assessment Models
There exist two general classes of models that can be deployed in performing supply chain risk assessments, these being qualitative and quantitative models.
Examples of qualitative models include scenario analysis, expert opinion, and Delphi methodology.
Qualitative methods largely rely on expert knowledge and subjective judgment to estimate the likelihood and consequences of a risk event.
Scenario analysis, for example, involves developing hypothetical situations that could negatively impact the supply chain and assessing potential outcomes and responses.
This often involves brainstorming sessions with key stakeholders and individuals with specialist knowledge of supply chain operations.
Conversely, quantitative assessment models utilize computational and statistical techniques to gauge risk events objectively.
Risk simulation, for instance, is a standard quantitative technique that employs statistical models to imitate possible outcomes under various circumstances.
This process can help identify the most significant vulnerabilities in a supply chain.
Risk Assessment Tools and Techniques
The selection of the most appropriate risk assessment tool or technique hinges significantly on the nature of the supply chain, the resources, and the business’s risk appetite.
One broad-based tool is the Risk Matrix, a visualization tool that demonstrates the likelihood of a risk event and its potential impact on the organization.
The matrix aids in identifying the most critical risks and prioritizing risk response strategies.
Failure Mode and Effect Analysis (FMEA) is another widely used risk assessment tool. This involves examining potential failures in the supply chain processes and assessing their severity, occurrence, and detection levels.
This systematic approach enables the organization to evaluate and mitigate risks before they occur.
Supply Chain Operations Reference (SCOR) model, a process reference model developed and endorsed by the Supply Chain Council, provides a robust framework for evaluating and improving supply chain performance.
Real-World Examples
Across the globe, businesses apply various risk assessment methods daily to smooth operations and avert possible interruptions.
In industries such as automotive, the supply chain network spreads across many regions, making using quantitative risk assessment and tools like FMEA common practice.
They efficiently manage risks associated with the reliability of suppliers, production postponements, and logistical issues.
Meanwhile, in the electronics sector, supply chains endure swift technological changes and the risk of obsolescence.
Here, companies often utilize strategic scenario analyses to handle these risks proactively. This risk assessment approach fosters adaptive and prompt decision-making in a fast-paced market.
In essence, risk assessment within supply chain management is no small matter. It includes spotting possible risks, determining their potential impacts, estimating the likelihood of their manifestation, and enforcing suitable mitigation strategies.
With the aid of comprehensive qualitative and quantitative tools and systems, organisations are thus equipped to effectively handle risk, ameliorate their overall performance, and advance their strategic directions.
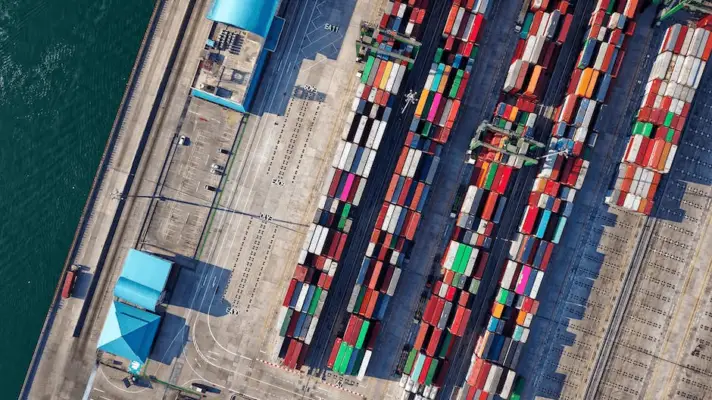
Steps to Implementing a Risk Assessment Plan
Step 1: Pinpoint Potential Risks within the Supply Chain
The process commences with pinpointing possible risks within the supply chain. Such risks can stem from internal processes, systems, or personnel and external factors like suppliers, clientele, government regulations, and natural catastrophes.
Risks can be operational, such as production delays or faults; financial, fluctuating prices or currencies; or strategic, for instance, alterations in market demands or competitive challenges.
Various tools can assist in identifying risks, including brainstorming sessions, reviews of past data, scenario analyses, and risk workshops.
To illustrate, a business might ponder over the risk of a significant vendor failing to deliver a vital component timely.
Step 2: Evaluate the Risks
Once the potential risks have been identified, they should be evaluated regarding their likelihood of occurrence and the magnitude of their potential impact.
This provides a means of prioritizing the risks and focusing on the most critical ones.
A risk map or matrix can be used to visualize and categorize the risks based on their probability and impact.
For instance, a risk with a high probability of occurrence and a high potential impact would be a top priority for management attention.
Step 3: Determine the Risk Response
After evaluating the risks, the next step is to formulate appropriate responses. These can include either mitigating the risk (by reducing its probability or impact), transferring the risk (through insurance or outsourcing), accepting the risk (if its impact is deemed tolerable), or exploiting the risk (if it also offers potential benefits).
For example, a company might decide to mitigate currency risk by using hedging instruments or transfer a delivery risk using a third-party logistics provider.
Step 4: Implement the Risk Response
The chosen risk responses must then be implemented. This involves designing and executing specific actions, procedures, or controls based on the risk response strategy.
The implementation should also consider the costs and benefits of the risk response and its alignment with the overall business strategy.
For example, a company might decide to implement advanced analytics and real-time tracking technologies to monitor and manage the delivery performance of its suppliers.
Step 5: Monitor and Review the Risks
The last step in risk management is to monitor and review the risks and the effectiveness of the risk responses.
This should be an ongoing activity, as the risk landscape can change over time due to changes in the supply chain and the external environment.
Regular risk audits, performance reviews, and feedback mechanisms should be implemented to ensure the risks are managed effectively.
For example, an organization might conduct a periodic risk workshop to review its progress and to identify any new risks that may have emerged.
Recognizing Successful Risk Assessment Practices
Considering how major companies like Toyota manage their risks provides useful insights into successful practices.
Renowned for its robust risk management system, Toyota employs a systematic risk identification, evaluation, and management approach.
This entails regular risk assessments, standardized risk evaluation and response methods, and potent risk culture.
Helpfully, these strategies have enabled Toyota to proficiently manage its global supply chain and quickly rebound in the wake of significant disruptions, such as the 2011 earthquake and tsunami in Japan.
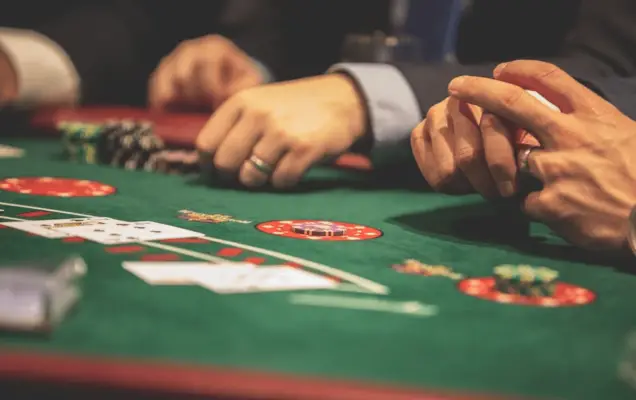
Case Studies of Risk Assessment in Supply Chain
Importance of Thorough Risk Assessment: Studying Mattel’s Toy Recall
To further reinforce the essence of comprehensive risk assessment, we can reflect on Mattel’s 2007 crisis, when the renowned toy manufacturer had to recall almost 20 million toys owing to safety concerns.
These toys, produced in China, were discovered to have unsafe levels of lead, causing significant damage to Mattel’s reputation and immense financial losses.
This case underscores how even with control measures in place, the company failed to foresee the risk due to shortcomings in its supply chain monitoring procedures.
Lack of proper risk assessment, specifically concerning supplier product safety, resulted in this unfortunate circumstance.
The Role of Risk Assessment in Automotive Supply Chain: Case of General Motors
Consider the case of General Motors (GM), one of the largest automakers in the world. They managed to avoid a significant risk during Japan’s 2011 earthquake and tsunami. The natural disaster caused massive disruptions in supply chains worldwide.
Yet, GM minimised the effect on its production due to implementing an effective risk assessment strategy.
The automaker used predictive data and risk analysis to anticipate possible disruptions. GM communicated closely with suppliers in Japan to maintain the flow of components, demonstrating a proactive approach to risk management.
Importance of Risk Assessment in Pharmaceutical Supply Chains: Case of Johnson & Johnson
The pharmaceutical industry holds high stakes in terms of risk due to the critical nature of its products.
An exemplary operation of risk assessment can be seen with Johnson & Johnson during the Tylenol poisoning case in the 1980s.
The efficient response plan led to the brand’s reputation of safety and trustworthiness. Johnson & Johnson’s quick recall of 31 million Tylenol bottles from retailers and households meant additional costs, but it prevented further damage.
This provides an outstanding example of how proper risk assessment and contingency planning can protect a company’s reputation and customer trust.
Failure of Risk Assessment: Case of Nike
Nike fell into a public relations crisis in the 1990s when activists and media outlets exposed child labor and poor working conditions in its overseas factories.
Nike failed to assess the risks associated with poor labor practices in its supply chain effectively.
This lack of risk assessment strategy significantly damaged the company’s reputation and sales.
After this controversy, Nike invested heavily in improving its supply chain practices and launched a Corporate Responsibility Report in 2005, emphasizing ethical and sustainable suggestions from its risk assessment.
How Airbus Navigated Supply Chain Risks during COVID-19
The COVID-19 pandemic has significantly impacted global supply chains, causing unexpected disruptions and challenges.
Airbus, the world’s largest airliner manufacturer, effectively applied risk assessment techniques to navigate the crisis.
The company conducted an extensive risk assessment to identify the most vulnerable parts of its supply chain.
These assessments allowed Airbus to prioritize resources, make strategic decisions about production, and create contingency plans for potential disruptions.
Airbus’s level of preparedness and resiliency reflects the importance of incorporating risk management into organizational strategy.
These case studies illustrate how risk assessment in supply chain management can mean the difference between failure and success.
It demonstrates how companies must be proactive regarding risk management rather than reactive.
The absence of adequate risk evaluation and mitigation can lead to significant losses both financially and in terms of reputation.
Companies must constantly evaluate and anticipate potential risks in their supply chains to ensure smooth operations and maintain their reputation.
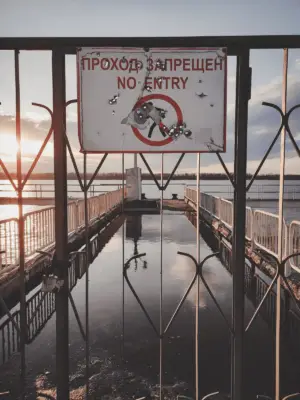
Conclusion
The vitality of risk assessment in supply chain management is undeniable, functioning as a cornerstone for thriving business operations.
It serves as both a shield and a guiding light – preempting calamities, reducing financial bleeding, and fortifying the company’s standing in the competitive landscape.
From understanding the vast array of risk categories and harnessing suitable tools and techniques for risk evaluation to constructing a robust risk assessment plan – the journey inculcates invaluable insights for both businesses and professionals.
The resonance of real-life cases amplifies the importance of diligent risk assessment practices, underscoring triumphs and missteps.
Ultimately, embracing meticulous risk assessment is a step towards molding resilient supply chains capable of sailing smoothly amidst the tumultuous waves of uncertainty.
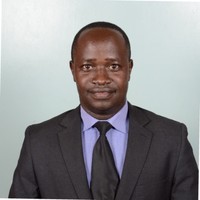
Chris Ekai is a Risk Management expert with over 10 years of experience in the field. He has a Master’s(MSc) degree in Risk Management from University of Portsmouth and is a CPA and Finance professional. He currently works as a Content Manager at Risk Publishing, writing about Enterprise Risk Management, Business Continuity Management and Project Management.