The validation of manufacturing processes is essential to ensure that products meet their quality attributes before release. A validated process provides confidence that the process can consistently produce a product conforming to specifications.
A significant part of the validation program is assessing the statistical capability of the process to meet these specifications. Since most processes are never in perfect control, some risk remains that a nonconforming unit may be produced and shipped.
For this reason, a portion of the production run is typically sampled and inspected and determine sample sizes.
The selection of an appropriate sample size is critical to providing sufficient process confidence while ensuring the efficient use of resources. How, then, does one go about selecting an appropriate sample size?
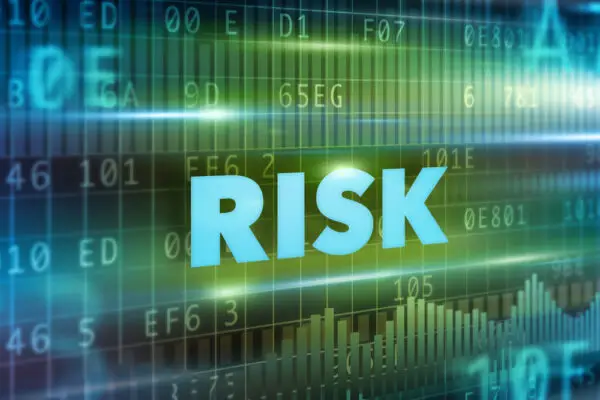
How do you establish sample size for process validation?
The appropriate sample size for process validation depends on several factors, including the complexity and variability of the process and the desired level of confidence in the results.
Generally, a larger sample size will increase the likelihood that any variations found are representative of the overall process rather than random chance. Guidance documents and industry practice prescribe a method of statistical analysis.
However, it is also important to balance this with practical considerations, such as cost and time constraints. One way to determine a suitable sample size is through the use of statistical power analysis and acceptance quality limits and acceptance criteria.
This involves determining the risk-based sample size necessary to detect certain levels of variation with a desired level of confidence, taking into account factors such as expected effect size and error rate.
What is risk-based validation approach?
The risk-based validation approach is a systematic methodology for determining the level of validation and documentation required for a particular process or product. This method takes into account factors such as the complexity and criticality of the process, as well as its impact on customer safety and product quality.
Prioritizing high-risk areas allows for efficient use of resources and minimizes regulatory compliance risks. Within this framework, processes and products are continually monitored and re-evaluated on an ongoing basis to ensure ongoing compliance.
Overall, the risk-based validation approach helps to streamline validation efforts while ensuring that regulatory requirements are met and quality is maintained. acceptance sampling levels might yield valid results based using a risk-based approach.
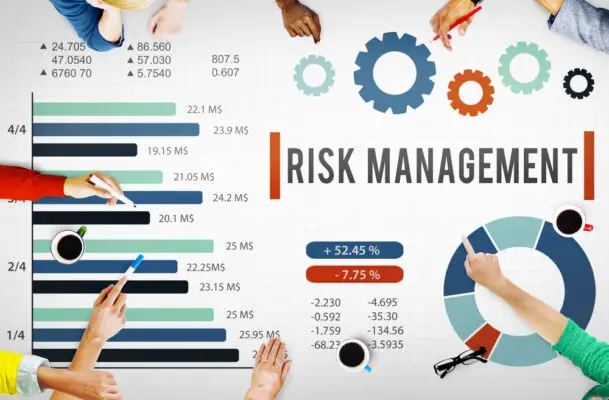
What is a good sample size for validation?
First, it is important to consider the stability and variability of the process or product being validated. If the process or product is relatively stable with low variability, a smaller sample size may be sufficient.
However, if the process or product is more variable with the potential for significant changes, a larger sample size may be needed to ensure that any changes are captured in the validation study. Additionally, regulatory requirements should also be taken into consideration. Different industries and regions may have specific guidelines for determining sample size in validation studies.
What is risk-based sampling strategy?
The risk-based sampling strategy, often used in process validation, involves assessing the likelihood and potential impact of failure points throughout the process. Sampling plans are then designed based on this risk assessment, focusing on critical components or steps with a higher likelihood and potential impact of failure.
This strategy allows for targeted monitoring and more efficient use of resources, as it prioritizes areas of greater concern. It can also be combined with other sampling strategies, such as a statistical approach, to provide a comprehensive evaluation of product quality.
The sample is taken through a risk analysis process with confidence and reliability levels determined. Validation protocols and process validations of the medical device need more samples to determine risk levels and a sampling plan.
Traditional Approach to sampling for Continuous Data
The approach most commonly used for sampling continuous data is derived from Military Standards. These standards recommend several fixed sample sizes based on the lot size and desired assurance level.
For example, a lot size of 1,000 with a desired assurance level of 95% requires a minimum sample size of 30 units; 1,000 with 99% assurance requires 100 units.
Military Standards MIL-STD-105E and ANSI/ASQ Z1.4 between 1988 provided guidance on selecting appropriate sample sizes. While this provides good general guidance, it has several shortcomings when applied to modern manufacturing processes:
- Assumes normal distribution which may not be a valid assumption.
- Levels of assurance are rather arbitrary (e.g., what’s the difference between 95% and 99%?)
- Does not factor in variability due to special causes which can adversely impact process performance.
- The table was developed based on military applications which often differ significantly from commercial manufacturing processes
In recent years, modern statistical methods have been proposed which offer significant advantages over traditional approaches such as those listed above.
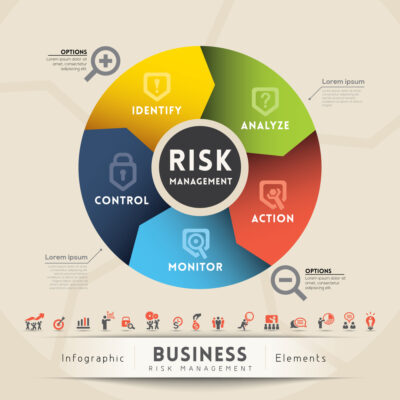
Advantages of Risk-based Sampling Methods:
Risk-based methods are founded on statistical principles and provide improved guidance for determining acceptable sample sizes in today’s complex manufacturing environments. In contrast to the fixed sample sizes recommended by traditional approaches, risk-based methods allow the selection of an optimal sample size specific to each situation and risk level.
This results in efficient use of resources as sample sizes can be smaller when process variability is low and larger when variability is high due to special causes (e.g., new operators, the changeover from one product to another). Other benefits include:
-Improved certainty regarding the probability that nonconforming units will escape detection – Facilitation of meaningful comparisons among different lots or batches (i.e., like processes can be compared directly)
– Scales linearly with increases in lot size so that very large lots (>1 million) can also be sampled efficiently
-Enables apples–to–apple comparisons among products with different specifications (yields are directly comparable regardless of failure definitions)
– Assessment of risks associated with multiple quality characteristics within the same lot – Ability to incorporate factors specific to the application such as costs associated with false positives/negatives, and reviewer agreement.
Conclusion
There are many factors to consider when determining appropriate sample size for process validation purposes. In the past, traditional methods involving fixed sample sizes were commonly used; however, modern risk-based approaches offer several advantages over these older methods.
Some benefits of using risk-based methods include improved certainty regarding the probability that nonconforming units will escape detection, facilitation of meaningful comparisons among different lots or batches, ease of scaling up for large lots, and enabling apples–to–apple comparisons among products with different specifications.
Although no method is perfect, risk-based approaches provide a sounder statistical foundation than traditional methods and offer greater flexibility in taking into account factors specific to each situation. As such, they should be given serious consideration when planning process validation activities.
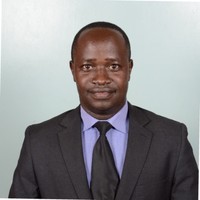
Chris Ekai is a Risk Management expert with over 10 years of experience in the field. He has a Master’s(MSc) degree in Risk Management from University of Portsmouth and is a CPA and Finance professional. He currently works as a Content Manager at Risk Publishing, writing about Enterprise Risk Management, Business Continuity Management and Project Management.