A Supply Chain Risk Management Plan is a document that outlines the procedures and processes needed to identify and mitigate any risks related to supply chain operations. It should include sections such as risk mitigation strategies, supplier onboarding processes, supply chain audit programs, and key performance indicators (KPIs) used to track progress.
Additionally, the plan should clarify the roles and responsibilities of the different stakeholders involved in the process. Examples of best practices for the successful implementation of a Supply Chain Risk Management Plan include:
1. Define a clear scope for the plan that is appropriate to your organization’s size and complexity.
2. Determine which processes will be included in the plan.
3. Perform a qualitative risk assessment to identify potential impact areas within the plan’s scope for each identified risk area.
4. Develop strategies for mitigating potential supply chain risks, such as diversifying suppliers, strengthening supplier relationships, improving tracking capabilities, reducing inventory levels, and implementing preventative maintenance systems or redundant backup systems where required.
5. Establish KPIs for tracking progress against goals set out in the plan (e.g., on-time delivery, quality assurance).
6. Implement measures to monitor and assess existing conditions against predetermined criteria stated in the plan (e.g., annual audits).
7. Provide training and guidance on executing supply chain risk management plans to personnel responsible for monitoring it within an organization (including third parties where applicable).
As businesses become increasingly global, they must recognize the potential risks associated with a global supply chain. The good news is that there are ways to mitigate these risks through the use of a supply chain risk management plan.
A supply chain risk management plan is an organized way of assessing the potential risks in your supply chain and providing strategies for managing them. Let’s explore what a supply chain risk management plan looks like.
Step 1: Establish Goals and Objectives
The first step in establishing a supply chain risk management plan is to determine what your goals and objectives are. This includes identifying any specific risks that may affect your business, such as quality control issues, delivery delays, or product recalls. Once you have identified these potential risks, you can then create strategies to address them.
Step 2: Assess Current Supply Chain Risks
Once you have established your goals and objectives, it’s time to assess the current state of your supply chain and identify any existing risks. This includes assessing both external factors—such as market conditions or geopolitical events—and internal factors—such as production capacity or employee turnover rates—that may impact your business operations.
Step 3: Develop Strategies for Managing Risks
After assessing the current state of your supply chain and identifying any potential risks, it’s time to develop strategies for how to mitigate those risks. This can include implementing stricter quality control procedures, diversifying suppliers, or developing contingency plans in case of unexpected disruptions in production or delivery schedules.
Additionally, it’s important to consider allocating resources toward monitoring changes in the marketplace and staying up-to-date on industry trends so that you can proactively respond to emerging challenges before they become larger problems down the road.
The supply chain’s efficiency is crucial to an organisation’s success. Globalization has created complicated supply chains, and their integration is making them more vulnerable to potential threats.
The long history of supply chain optimisation is focused on cost minimization, reduced inventory, asset maximisation and flexibility. COVID-19 shows that many businesses have no ability to assess the risk of global disruption in their supply chain relationship.
Fortunately, supply chain technologies could dramatically improve supply chain management and lead agile and resilient supply chains.
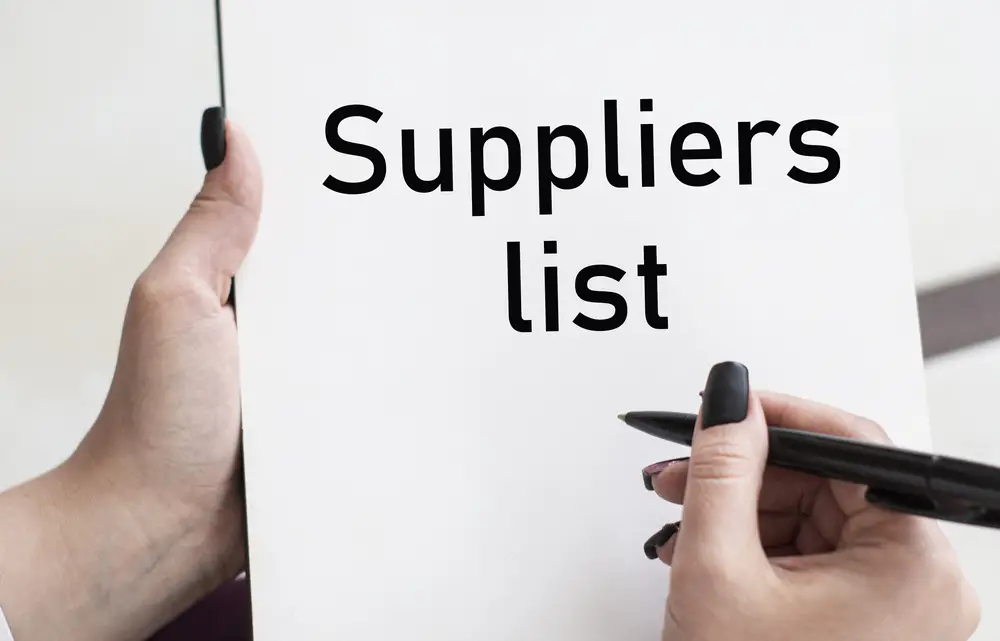
Unfortunately, supply chain risks continue to grow when global interconnections become increasingly interconnected and digital-based, and large-scale instability lurks everywhere, from environmental to economic factors.
The report says that the number of organizations experiencing multiple interruptions increased dramatically by 2025. The pandemic has affected consumers across the globe because even the average consumer has a good understanding.
Recent increased rapid operation intensities require robust supply chain solutions. As more information becomes available and information becomes more accessible, the risks increase in the delivery of products.
In their supply chain, unknown targets can be obtained from partner suppliers and third parties. Supplier risk management has been instrumental in organizational risk management strategies.
Overview of Supply Chain Risk Management
Supply chain risk management must be key to a business’s competitiveness. Global supply chains trade is growing, as is the market. The disadvantage of such a strategy is the vulnerability of supply chain tracking.
Some companies do things well, but some don’t! Companies with supply chains risks management are ready to minimize their effects. Diversification of supply chains from a geographical perspective lowers supply-side risk, and multi-sourcing commodities may reduce dependence on supply.
Best Practices for Supply Chain Risk Management
Managing supply chain risks is an essential part of any successful supply chain planning. It includes identifying, prioritising and managing risk to ensure that all supply chain-related activities are carried out safely and securely. The best practices for preventing supply chain risk include:
1. Utilizing technology to identify and monitor risks throughout the supply chain. This includes using analytics, data mining, predictive modelling or other software to identify potential risks.
2. Establishing business continuity plans to maintain operations in case of disruption or emergency.
3. Develop policies and procedures that provide clear direction on how the organization will handle potential risks.
4. Monitoring suppliers regularly to ensure compliance with quality standards, delivery timelines, etc.
5. Creating a culture of collaboration within the entire supply chain network by fostering strong relationships with suppliers, third-party logistic providers, etc.
6. Implementing strong security measures such as encryption tools and access control systems to protect confidential data from malicious actors or acts of nature (e.g., natural disasters).
7. Implementing automated tracking systems for shipment transit times and real-time alerts for schedule delays or order issues (if applicable).

Steps to identify supply chain risks & vulnerabilities
An SCRM plan works when the risk of reversible changes in your business is identified as inherent in a supply chain process. Suppliers you overlook are threatening your safety by being uninformed and underestimating them.
In this respect, excluding internal stakeholders from any procurement processes will make it difficult to respond to supply chain problems without the required capability.
Identify Risks
You now have an entire supply chain list to help you pinpoint any supply chain danger – known or unknown. These can include direct risks such as natural disasters, government shutdowns or recalls, lack of raw materials or indirect risks such as major suppliers issues that could stall business.
Segment supply chains using the methods outlined above. IT experts should have an excellent grasp of new cybersecurity threats and security vulnerabilities from third parties. Communications professionals will also know the risks of reputation and overall risk management.
Quantify Risks
After knowing all the risks, you must prioritize them depending on their magnitude and severity. Probabilities for risks occurring and impacts. Complex organisations can take additional steps and complex scenario plans may be necessary.
Organizations with different locations or shipment types may require different risk management measures. Sometimes, you may be required to include a different internal chain when doing complex operations and mitigate risks in the risk environment.
Connect with your team
Supply chain management involves teams and teamwork. No one can understand and think through the risks in a supply chain. You’ll need members who work in various departments at an organisation, including finance, technology, human resources, customer care, procurement and communication.
They need to understand the supply chain to identify specific supply chain risks. Your team can assist in mapping your most important product or service, as well as assisting you in monitoring the quality. Keep in mind your supplier also makes up your team.
Auditing your supply chain risk
Supply chain audits are an important part of risk management and should be conducted regularly to assess the effectiveness of current processes and identify any areas that may need to be improved or modified. Audits help organizations ensure that their supply chains operate efficiently and safely while mitigating potential risks. The best practices for auditing your supply chain include:
1. Establishing a clear audit process with defined objectives. This includes setting out who will be responsible for conducting the audits, how often they will take place, and what information needs to be examined.
2. Establishing KPIs that can provide a benchmark against which progress can be measured over time.
3. Develop checklists to ensure all necessary steps are taken during each audit.
4. Document all findings, including positive results and any areas of improvement identified during the audit process.
5. Regularly review audit results and adjust processes accordingly where necessary to ensure compliance with safety standards, supplier agreements, etc.
6. Utilize digital technologies such as artificial intelligence (AI) or predictive analytics software where applicable to streamline the audit process and improve the accuracy of results.
McKinsey says most organizations don’t audit their supply chains. But any retailer that sells merchandise should audit its supply chain. However, all businesses benefit from a supply chain audit, which identifies ways to improve process efficiency and cost reduction.
Develop a Supply Chain Risk Management Strategy
The plan of this resource brings out the advantages of the supplier chain risk management strategy. You now have a chance at the mitigation phase in your risk management lifecycle. Prepare emergency plans for the threats identified.
Developing a comprehensive supply chain risk management strategy is essential for protecting an organization from potential losses or disruptions due to unanticipated supply chain changes. The best practices for developing such a strategy include:
1. Establish objectives and processes for managing and mitigating risks throughout the supply chain network.
2. Identifying potential risks based on industry trends and technology advancements and assessing your own internal processes and capabilities.
3. Develop contingency plans to address unexpected events or disruptions that could impact the flow of materials, services or information within the supply chain network.
4. Creating policies and procedures to ensure compliance with safety regulations, supplier requirements and other related standards
5. Utilizing analytics, data mining and predictive modelling tools to monitor performance metrics in real-time and identify improvement opportunities to reduce overall costs.
6. Educating stakeholders (suppliers, logistics providers, etc.) on risk management best practices to create a culture of collaboration across the entire supply chain network.
Common types of supply chain risk
Common types of supply chain risks include supplier disruptions, natural disasters and political instability, cyber security threats, customer demand volatility and counterfeiting. Supplier disruptions can occur due to a sudden change in market conditions or a lack of resources, while natural disasters and political unrest can have an immediate or long-term impact on the availability of supplies.
Cybersecurity threats can come from both external forces as well as internal processes, making it important for organizations to establish protocols for protecting data and other sensitive information.
Customer demand volatility can lead to supply chain imbalances if there isn’t sufficient planning to anticipate changes in demand trends, while counterfeiting is becoming increasingly prevalent across many industries due to technological advancements.
Risk mitigation strategies should focus on identifying and addressing these common sources of supply chain risk before they become unmanageable.
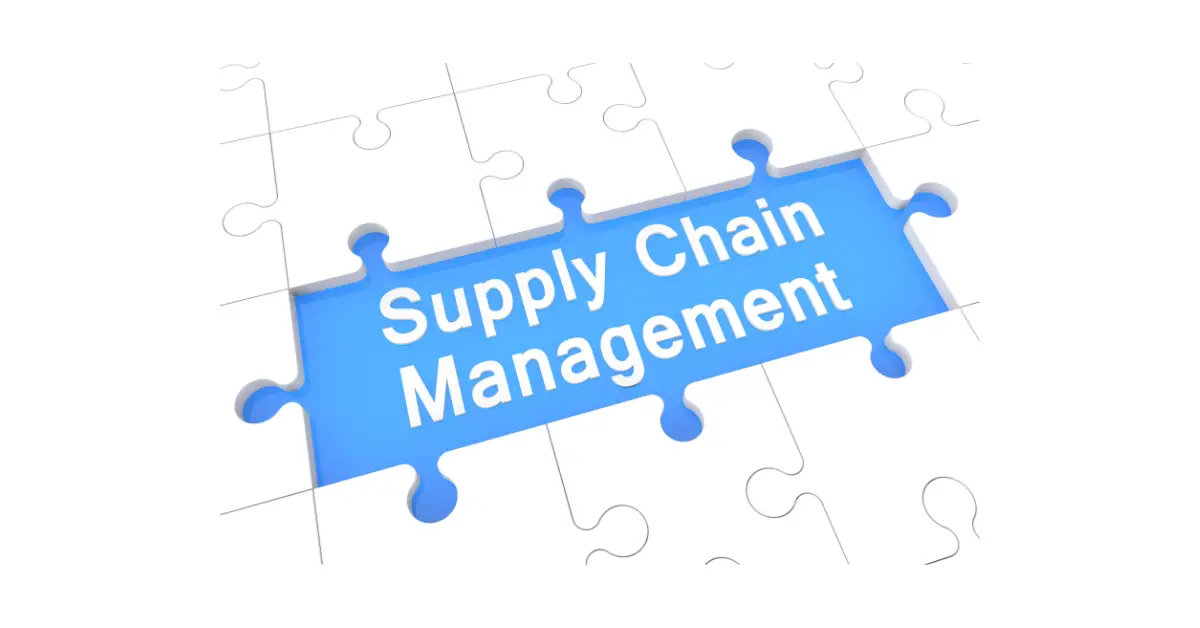
Supply Chain Risk Management vs Supply Chain Resilience
supply chain risk management focuses on identifying, analyzing and mitigating the source of risks within the supply chain network, supply chain resilience is the capacity to anticipate, adjust and adapt quickly to unanticipated events.
Supply chain risk management strategies strive to eliminate risks before they occur and maintain operational efficiency by proactively managing potential disruptions. On the other hand, supply chain resilience initiatives such as agile manufacturing and contingency plans aim to reduce recovery time by enabling organizations to respond quickly and efficiently in the event of an unexpected disruption.
Thus, while supply chain risk management seeks to minimize losses through proactive measures, supply chain resilience looks at ways of minimizing downtime so that operations can be resumed quickly after a crisis.
Supply chain resilience refers to the capacity to survive adaptation or transformation to the threats outlined above. BCI says resilience to COVId19 impacts has been key for many businesses. SCRM maintains this elasticity or guarantees supply chains will rebound.
Conclusion
A strong supply chain risk management plan is essential for any global business looking to remain competitive in today’s market. By taking steps such as establishing goals and objectives, assessing current risks, and developing strategies for managing those risks, businesses can protect themselves from unanticipated disruptions while remaining agile enough to take advantage of new opportunities when they arise. With a comprehensive risk management plan in place, businesses can rest assured that their operations will run smoothly even when faced with unpredictable market conditions or unforeseen circumstances
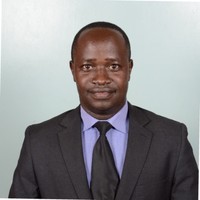
Chris Ekai is a Risk Management expert with over 10 years of experience in the field. He has a Master’s(MSc) degree in Risk Management from University of Portsmouth and is a CPA and Finance professional. He currently works as a Content Manager at Risk Publishing, writing about Enterprise Risk Management, Business Continuity Management and Project Management.