Cost risk analysis is a vital tool used in project management to assess and evaluate potential cost overruns and financial risks associated with risk financing costs along with a project. It involves a detailed analysis of various factors, such as the project scope, available resources, and market conditions, to determine the likelihood and impact of cost uncertainties.
Cost risk analysis is a critical process that helps project managers make informed decisions, prioritize resources, transfer costs, and develop contingency plans to mitigate potential risks. In this context, this article will provide an example of cost risk analysis and how it can be used to identify and manage financial risks in a project.
Cost risk analysis is a process used to evaluate the cost-related risks of a project. It helps determine the likelihood of unforeseen costs and estimate how much they could be.
This process involves assessing all potential risks associated with the cost of a project, from materials to labor costs, so that you can take preventive measures and make decisions accordingly. Let’s go over what it looks like in action.
What Does Cost Risk Analysis Look Like?
Using a cost risk analysis example, let’s say you are starting a construction project and want to research the probability of additional costs due to construction materials and labor. To do this, you must first identify all the possible external cost risks associated with these two factors—materials, labor, and unexpected events
and then assess the likelihood of each one occurring with the help of an expert in the field or an appropriate software tool. Once you have identified these risks, you can develop strategies for preventing them or minimizing their impact on your budget.
For example, if there is a high risk of additional costs due to changes in material prices during your construction project, you can create contingencies for those scenarios by negotiating fixed prices for certain materials before work starts or by setting aside extra funds for potential increases in cost.
Similarly, if there is a high risk of labor-related issues resulting in higher-than-expected costs, you can look into ways to minimize this risk by hiring experienced contractors who will provide quality work at reasonable rates or by putting extra manpower on standby in case more workers are needed during peak times.
In addition to identifying and mitigating potential risks associated with materials and labor costs, it is also important that you consider other potential cost risks, such as weather conditions or changes in legislation that could affect your project timeline or budget.
Examples of risk control costs
Internal cost risks
The internal actions of a company can cause internal risks. In general, a project requiring less work can result in extended schedules, which increase costs and time. The longer the project, the greater the risk transfer costs and expenses. All right.
Consequently, this threat also affects schedule as well as performance and quality. Internal risks can be avoided if you plan correctly and manage the project correctly. External costs are also very expensive and can be unpredictable.
TCOR is typically calculated using the total cost of risk per $1,000 of revenue
Since TCOR requires that revenue numbers be used for measurement/quantification, firms have a good opportunity to track their cost of risk and management programs at the same time maximizing internal cost-effectiveness.
In its capacity as a measurement tool, TCOR provides actionable information to determine how effectively a risk-management and control program can be implemented.
All risk-related costs are used to calculate TCOR
For their TCORS calculations, the organizations need to determine and assess their costs, these typically begin with insurance premiums paid, commissions for agents and brokers, and administration costs.
Pay attention to the areas where costs may increase
Project costs are usually divided into three main groups *direct and indirect costs, often the cost risks from this class. In addition, it should be taken into account how much labor is required to reduce the potential cost of ballooning equipment.
Risk Management Administration Cost
These expenses typically include internal and external expenses such as claims reporting and investigation. TCOR has traditionally reflected its revenue percentage as an indicator for benchmarking effectiveness controlling risk and efficiency year after year. TCOR can be used as an important part of a business risk management process to improve its risk management capabilities.
Taxes and Fees
Taxes, fees associated with administrative costs, and placing an RRFP, are required. TCOR. These taxes are paid to state agencies that administer and regulate insurance placement.
Measure performance with Earned Value Management (EVM)
Earned value management helps track performance for tasks and packages. The analysis combines present performance with projected performance. Using these methods can be helpful for managing a project but you cannot depend solely on EVM as they change quickly.
Using the EVM, you will cover a variety of potential risks and their consequences using the Contingency Budget. Earned values refer to your budget earned primarily through your work. The proposed project budget is $20,000.
Conclusion
Cost risk analysis is an invaluable tool when planning any kind of major project involving significant financial commitment. By taking into account all possible sources of risk associated with both materials and labor (as well as other external factors) ahead of time,
you can dramatically up risk control and reduce the chances that unforeseen expenses will derail your plans and cause costly delays down the road. If done properly, cost risk analysis can be a powerful ally in helping ensure that your projects stay on track – and within budget!
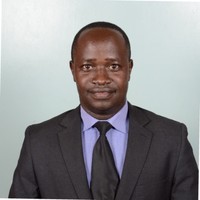
Chris Ekai is a Risk Management expert with over 10 years of experience in the field. He has a Master’s(MSc) degree in Risk Management from University of Portsmouth and is a CPA and Finance professional. He currently works as a Content Manager at Risk Publishing, writing about Enterprise Risk Management, Business Continuity Management and Project Management.